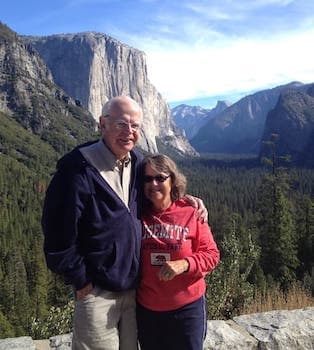
Curated with aloha by
Ted Mooney, P.E. RET
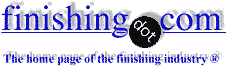
The authoritative public forum
for Metal Finishing 1989-2025
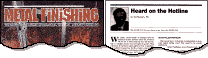
-----
Zinc Plating "Service Condition" (SC), Thicknesses, & Corrosion Resistance

Q. I am rebuilding 3 piece aluminum wheels (1st time) which are bolted together via 40 each M8-1.25 X 25 mm flange bolts. I need to buy new bolts as torque is critical. Existing bolts appear to be zinc plated steel. Given that these will be on car wheels exposed to all types of road conditions I've been trying to understand what ASTM B633 service condition rating I should be looking for. SC4 I assume but I was hoping to find someone knowledgeable in this area to help me to use the correct bolts.
FG GrimesAuto Mechanic - Bentonville Virginia
June 24, 2023
A. Hi, FG. Wheel bolts can be made from aluminum, titanium, electroplated steel, and perhaps other materials). Steel bolts can be zinc plated, zinc alloy plated, chrome plated, etc. If you are replacing them it is obviously important to double check that they were zinc plated if you are seeking the same look.
Zinc plating is covered by ASTM B633, some aspects of which are very rigid, some aspects rather loose. In one way "Service condition" (SC) is a rigid requirement (greater plating thicknesses are required as you go from SC1 (mild) to SC4 (very severe), and meeting those minimum thicknesses is not optional. But in another way, the spec is rather loose (because which SC an application falls into is handled with a few examples rather than an exact SC for every possible application).
But with the bloviating out of the way, automobile wheels are an extremely corrosion-prone application, and doubtless SC4 :-)
Luck & Regards,
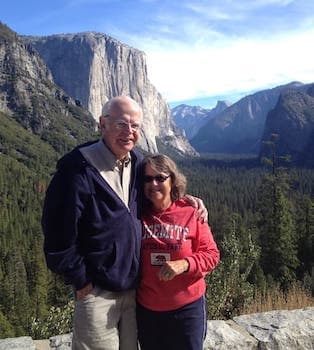
Ted Mooney, P.E. RET
Striving to live Aloha
finishing.com - Pine Beach, New Jersey
⇩ Related postings, oldest first ⇩
Q. Good afternoon,
Some of you know me, not all of you do, but my name is Fred Robinson and I have been a member of the Copper State Bolt & Nut Co. family for about 15 years now. Having years of experience with the various coatings, finishes, performances, thicknesses, etc., I still come to the realization that valued people like yourselves will probably forget more about coatings and finishes, then I will ever learn in a life time. Some of you are valued suppliers and others are well known sources of information (valued supplier of information if you will). I will thank you all in advance as I approach you with the following list of questions in search for much needed information that doesn't seem to be fully defined by the ASTM specifications:
ASTM B633
ASTM F1941/F1941M-16
1) Is or would a plating requirement of ASTM F1941/F1941M-16-Fe/Zn-15A be supported to have a better than 6 hour resistance to first appearance of white corrosion? (See Table A1.1 for 12A contrasts)
2) Is or would a plating requirement of F1941-Fe/Zn-15A be supported by the ASTM F1941 to have a better than 72 hour resistance to first appearance of red corrosion? If so, how many hours before first appearance of red corrosion (maybe 90? Since 8µm = 48hrs & 12µm = 72?)?
3) Is or would a plating requirement of B633 Type I (15 Microns) not be supported by the ASTM B633, having no resistance to first appearance of white corrosion? (See attached or below B633-11 Table 2 for reference)
4) ASTM B633 does not appear to include a performance table like the one found in F1941. What would be the salt spray performance to first appearance of red rust for plating to that of ASTM B633, Type I, SC3 (12 microns)? What would it be if the thickness were increased to 15 microns (Type I remains)?
5) Is the resistance to first appearance of white corrosion a greater number of hours if a fastener was plated to F1941-Fe/Zn-15AT (trivalent) versus being plated to a hexavalent F1941-Fe/Zn-15A?
6) Is the resistance to first appearance of red corrosion a greater number of hours if a fastener was plated to F1941-Fe/Zn-15AT (trivalent) versus being plated to a hexavalent F1941-Fe/Zn-15A?
7) If trivalent does in fact have a greater resistance to both white and red corrosion, then how many microns of trivalent would be equal to that of 15 microns of hexavalent?
Again, thank you all very much for your time and consideration in this matter. Have a good day.
Regards,
Copper State Bolt & Nut Co. - Phoenix, Arizona, USA July 31, 2015
A. Hello Fred!
I work in a company which zinc plates and chromates bolts, screws, nuts and other fixation systems for the construction, automobile and electronic appliance industries. We work with these and other specs (these are kind of old, but some of our clients ask for them) and I think I can answer some of your questions.
1) Yes, it should resist more than 6 hours in most cases. If this spec existed, you would NEED the parts to resist at least 6 hours without white corrosion. You could use a cheap conversion coating and comply with all other requirements.
2) It should resist more than 72 hours, could be 96. This spec does not exist, so we can only extrapolate!
3) Without any conversion coating, there is no white corrosion resistance. Zinc will corrode almost immediately.
4) That standard does not include a method to evaluate corrosion resistance measurement for type I, only defines conditions for the usage of the part to be plated. "Severe" conditions are the recommended for an SC3, and "Extreme" for an SC4 (25 microns). Many platers manage with both standards making SC2 III equivalent to Fe/Zn 8C using only the higher spec (120 hours).
5) Generally, yes. Clear passivation with trivalent chromates is superior than hexavalent. This does not apply for yellow! But... you can lower costs and get some (cheap) trivalent products that are the same as hexavalent.
6) Yes, you delay the appearance of white corrosion, and the red corrosion appears later.
7) It depends on the process of chromating. If the process is well performed, with a good product, I think you can achieve 96 hours without red rust with only 5 microns. Less than 4 microns, passivation of zinc is not homogeneous for trivalent (in my experience with bolts and screws).
Regards!
TEL - Autoperforantes - Cañuelas, Buenos Aires, Argentina
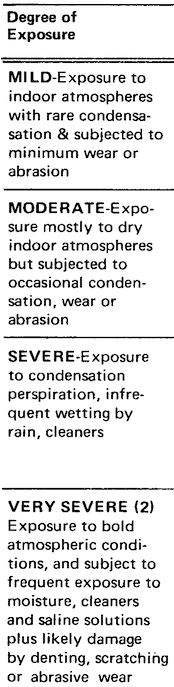
Does ASTM B633 cover steel hangers?
Q. Hi,
Does standard ASTM B633 cover steel hanger?
What is the definition of severe, mild, ... in this standard?
Thanks in advance
arash
- Tehran,Iran August 18, 2015
A. Hi Arash. I don't know what kind of steel hangers you are referring to, but ASTM B633 is a standard for zinc plating of steel items. I don't know of any reason that it wouldn't be applicable for the hangers you are thinking of.
I don't think B633 actually "defines" service conditions; but
1). it specifies the minimum plating thickness for them: Very Severe = 25 µ; Severe = 13µ; Moderate = 8µ; Mild = 5 µ; and
2). it gives typical examples. I don't have a copy handy, but the MFSA Quality Metal Finishing Guide (avail. from www.nasf.org) offers these examples.
Regards,
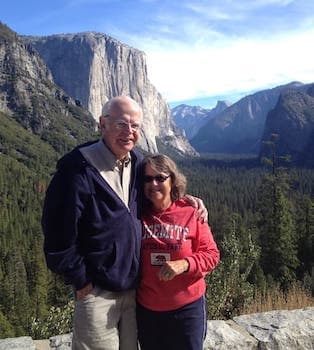
Ted Mooney, P.E. RET
Striving to live Aloha
finishing.com - Pine Beach, New Jersey
Q, A, or Comment on THIS thread -or- Start a NEW Thread