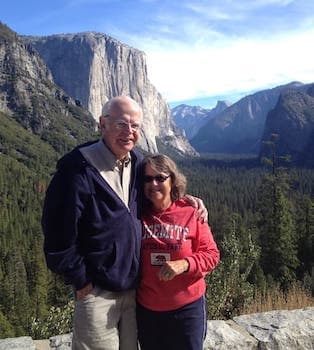
Curated with aloha by
Ted Mooney, P.E. RET
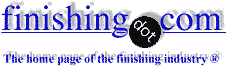
The authoritative public forum
for Metal Finishing 1989-2025
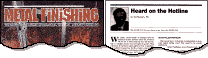
-----
Nickel and gold plated components failing; is gold too thin?
Q. Dear sir,
We have this stamped component like a small cover (2 mm x 1 mm x 1 mm) of [substrate] material Moly Perm alloy Grade 923 (Ni 80%, C 0.04%, Mo 4%, balance Fe). Drawing specification stated Hard Gold 0.000005 thick over Nickel Sulfamate 0.00005-0.000075 thickness. With this plating, it must pass 96 hours in aggressive acidic sweat test in oven with temperature of 60 °C.
Our process is as follows:
Alkaline Soak clean (80 °C, 1 mins), rinse,
Wood's nickel strike (3 volts, 2 mins), rinse,
Nickel Sulfamate (38 °C, 20 mins), rinse,
Gold plating 1 (33 °C, 0.2 ASD),
Gold plating 2 (49 °C, 0.2 ASD), rinse (without any sealant use).
We are able to achieve the thickness required but fail badly on the sweat test. Corrosion on edges of the inner side of the cover and corrosion signs of tiny pin holes. Low current density areas were definitely failing the sweat test.
Are there any ways to improve this process?
How could we prevent pin hole corrosion with this material?
Is our Wood's nickel strike good enough to withstand corrosion, or any good recommendation for pretreatment improvement?
Can we pass the aggressive sweat test without sealant in this process?
Please kindly advice this issue and helping hands is much appreciated.
employee - Hong Kong
June 25, 2015
by Reid & Goldie
-- hard to find & expensive; if you see a copy cheap, act fast!
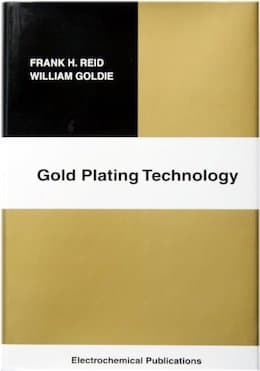
on eBay or
AbeBooks
or Amazon
(affil links)
A. Hi Joel. Are the plating thicknesses you've offered us in meters or what units?
Are the thicknesses thus 50-75 µm (2-3 thousandths of an inch) of sulfamate nickel followed by 5 µm (2 ten thousandths of an inch) of gold? That sounds like quite substantial thicknesses.
Or are the thicknesses in inches -- in which case I wouldn't credit 5 millionths of an inch of gold with offering even 96 minutes of sweat resistance :-)
The Wood's nickel is not for corrosion resistance but for good adhesion to your nickel alloy substrate. Are you performing bend tests or other adhesion tests to verify that the Wood's nickel is doing the job? If you are getting good adhesion, and the appearance is right, and the specified thicknesses are reasonable, you can start looking for specific defects in your process ... but if the plating isn't adhering it can't offer corrosion resistance.
Regards,
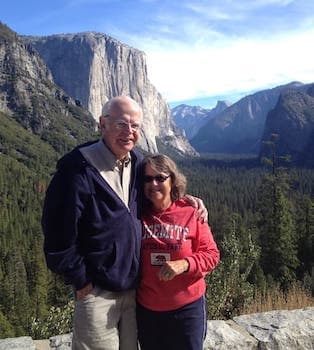
Ted Mooney, P.E. RET
Striving to live Aloha
finishing.com - Pine Beach, New Jersey
Q. Dear Sir,
Thanks for your reply.
Sorry for the thickness error, Hard Gold 1.5 µm thick over Nickel Sulfamate 1.5 µm thickness. With this plating, it must pass 96 hours in aggressive acidic sweat test in oven with temperature of 60 °C.
Our process is as follows:
Alkaline Soak clean (80 °C, 1 mins), rinse,
Wood's nickel strike (3 volts, 2 mins, 0.4 ASD), rinse,
Nickel Sulfamate (38 °C, 20 mins, 0.5 ASD), rinse,
Gold plating 1 (33 °C, 0.2 ASD, 45 mins),
Gold plating 2 (49 °C, 0.2 ASD, 15 mins), rinse (without any sealant use).
We have no problem with adhesion and bend test but find difficultly in the sweat test.
Is nickel sulfamate able to withstand corrosion?
Is sealant necessary for achieving better result in sweat test?
Are there ways to reduce the pores in Gold plating to prevent corrosion?
Are we heading the right direction towards better sweat test result, please advise.
Thanks
- Hong Kong
A. Hi again Joel. Typographical errors are not a problem -- we all make them. But I suspect additional errors and get the feeling that maybe someone is telling you what they are doing, but the information may be getting scrambled. Surely you can't be Wood's Nickel Striking at a lower current density than you are nickel plating at?
by Larry Durney
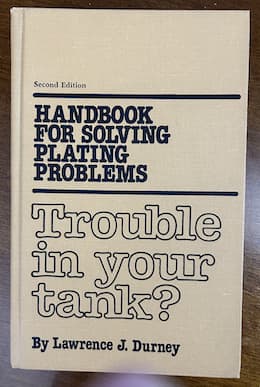
on Amazon
(currently UTL
on AbeBooks & eBay)
(affil links)
Your sulfamate nickel plating is actually only 1.5 µm (0.00006")? It's hard to believe that it can offer much corrosion resistance at that thickness, so I'd say you are relying strictly on the gold for corrosion resistance (which is probably good, because leachable nickel will result if the gold is breached, and that's probably a big problem in an application that uses a sweat test).
For troubleshooting the process, please see if you can find a copy of Lawrence Durney's "Trouble in Your Tank?" .
as it presents an organized and detailed way to approach such plating problems, but you may be able to simply try a nitric acid porosity test or Dimethylglyoxim test (see topic 0644) to determine if the gold plating isn't doing the job. If you feel the gold plating is being done right but is still too porous, pulse plating can reportedly reduce porosity.
Where did this spec come from? You say you have a drawing, but is this an internal design you are responsible for, or is this jobbing work? Did anyone run samples yet verifying the feasibility of this process or something similar? A sealant would probably improve the corrosion resistance, but are we blue-skying ways to pass a sweat test, or complying with a spec on a drawing?
Thanks for the details of the process, but if you could also explain where you fit into the design-production cycleand whether the parts are barrel plated or rack plated, it might help. Good luck.
Regards,
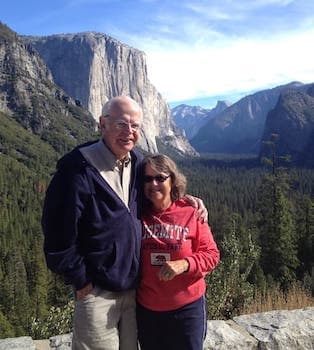
Ted Mooney, P.E. RET
Striving to live Aloha
finishing.com - Pine Beach, New Jersey
A. Hello Joel, As Ted had pointed out in his post, the Ni Sulfamate coating would not be thick enough to offer corrosion resistance. Try conducting a controlled test on a non production part. On each plating cycle increase Ni plating thickness by 25%. After the sweat tests you will be able to determine if the thickness is to be increased. If the Ni Sulfamate thickness you are using is an inside or customer generated engineering spec, it should be reviewed and changed. It doesn't sound like the spec is a common industrial or Mil spec to me. Good luck, hope this helps.
Mark BakerProcess Engineering - Phoenix, Arizona USA
Q. Dear sir,
Thanks for all the reply.
Is there any ways to improve on the gold plating as mentioned above and how are we able to reduce the porosity problem.
Please advise.
Help is much appreciated.
Joel
- Hong kong
A. In the late 60's, I consulted for a guy that was gold plating (.175 to .250 microns - 7 to 10 microinches) about 100/000, per day, magnetic SS knives, forks, and spoons for Standard Oil, who gave them away at their stations with a fillup. Nickel was applied first, of course. A 500,000 batch of these was sent to the Asian stations by boat. Every piece was affected by the salt. On each piece, there were several obvious brown spots from the salt atmosphere attacking the nickel and SS though the pores. 7-10 microinch gold plating is very porous. Also, the SS was very cheap and had many inclusions and this created pores in the plating.
The first reaction was to strip and replate, at least the gold. They quickly installed a salt spray cabinet. I did some experiments and found that the part passed the salt spray tests with only mild cleaning and a short soak in a nitric acid/potassium dichromate solution. It surely passivated the Ni and SS in the pores. It also completely removed the brown stain. From that point on, the HNO3/K2Cr2O7 dip was the last tank in the cycle for every piece plated.
To me, there seems to be similarities between this problem and yours.
- Nevada, Missouri, USA
Multiple threads merged: please forgive chronology errors and repetition 🙂
Flash gold fails perspiration test
Q. Dear Sir ,
We are Performing Flash gold plating prior to nickel plating on brass substrate.
base metal - brass
nickel plating - 4 microns
flash gold - 0.1 microns
After gold plating we perform perspiration test for 24 hours, and check this tape test.
We are finding some residue of gold plating on tape.
So please share the thoughts that how flash gold with stand 24 hrs perspiration test .
We do not use any lacquering procedure as it will not be feasible for us to perform.
metal components - noida , India
February 4, 2017
A. Hi Utkarsh,
I'm not familiar with the test you mention, however, the nickel should stay active and not allowed to dry out before gold flash. If the nickel starts to dry up a bit an oxide can form and then the gold won't stick very well.
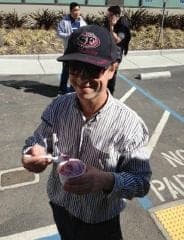
Blake Kneedler
Feather Hollow Eng. - Stockton, California
Q. Hello Sirs,
Is it possible to make gold flash plating layer of 0.005 Micron thick? Or how much minimum layer thickness possible for gold flash?
I'm not more aware of gold plating, Can you guide me, please?
- Kolhapur, Maharashtra, India
April 10, 2019
A. Hi Arjun. Yes, it's possible to apply a gold plating layer of 0.005 Microns thick, but that answer is probably of little help to you. But I don't know what the real question is, and am having a hard time imagining a gold deposition layer of 0.005 microns being useful for anything at all. Even the extremely thin gold immersion deposits are 10X this thick. Sorry.
Regards,
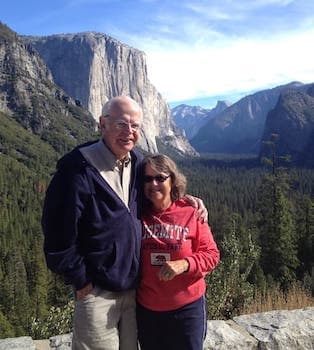
Ted Mooney, P.E. RET
Striving to live Aloha
finishing.com - Pine Beach, New Jersey
Q. Thank you, sir.
Yes, You are right, 0.005 micron layer may not be useful for anything.
But we have to get just like golden appearance on nickel undercoat for electrical brass contacts instead of 0.1 micron thick gold plating.
So, can you guide me on my queries below?
1 Is it a controllable process of 0.005 micron gold flash on nickel undercoat, or we should go for 0.01 micron?
2 Which will be better 0.005 micron or 0.01 micron thick as an only surface color concern?
3 Is it will get the same golden appearance as like 0.1 micron gold plated?
I hope to know more here. Thanks in advance.
- Kagal, Kolhapur
A. Hi again Arjun. You're asking for help doing something I've never heard of, sorry :-)
Why would only the 'color' be important in a electronic contact application, and for how long would it be important? Diffusion and/or wearing away in almost no time is a serious factor for thin coatings on contacts and 0.05 micron is the thinnest gold layer I am familiar with even for an immersion gold temporary solderability protection layer, and you want to go 5X to 10X thinner than that on contacts. Why? Although I don't know for sure, I doubt that a coating of 0.005 to 0.010 would be visible.
You work for an electronics company -- maybe you can get tutoring from your experienced engineers on this subject? If not, yet again, please tell us who you are and what this whole thing is about. Like why you would want a coating 10X thinner than apparently anyone else in the world :-) Thanks! Good luck!
Regards,
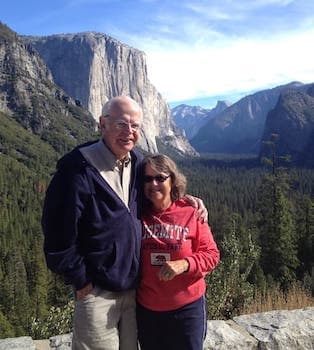
Ted Mooney, P.E. RET
Striving to live Aloha
finishing.com - Pine Beach, New Jersey
A. It is, of course, possible to plate any thickness down to zero.
To put this in perspective, 0.005 microns is 5 nanometres
The wavelength of visible light is 400-700nm.
A gold atom is about 0.14 nm diameter so we are considering about 30 atoms thick. With the normal distribution of plating thickness some areas would be expected to get almost none.
Such a thickness would inevitably be highly porous and require sophisticated equipment to measure it.
I cannot imagine any possible use for such a deposit.
Is it possible that someone has misread a spec or confused the units?
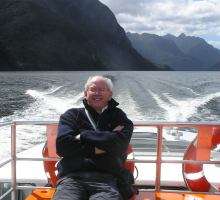
Geoff Smith
Hampshire, England
Q. I am continuing to comment here with my earlier conversation regarding gold flash --
Now we have some experiments on gold flash within the 0.03-0.06 micron range for electrical contacts and our product requirements have been complied with. But nowadays the plater is not responding. So I would like to hear if this is feasible or not with this layer thickness. Or any other option?
- Kolhapur, Maharashtra, India
by C W Zanariah Ngah
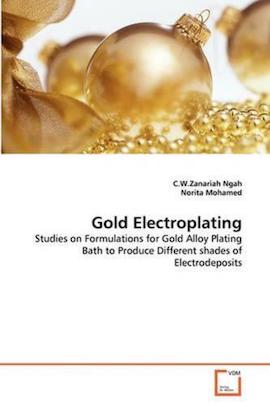
on eBay or
AbeBooks
or Amazon
(affil links)
A. Sorry but I'm still not quite getting it, Arjun. Three postings later and you're not answering the question of what you're trying to do, and we're still just guessing what you're after, and still guessing whether there is a repeated typo or there isn't, and guessing what kind of "other option" you are looking for, and we can't seem to get clarification from you :-(
But I'm now suspecting that by 'contacts' you mean more or less permanent mating surfaces on connectors of some sort rather than contacts in switches or relays. And I guess you want them to 'look like' gold mating surfaces irrespective of how they function. In certain consumer applications like HDMI cables, gold is sometimes plated onto connectors for the sales appeal of the gold look even though it doesn't do anything, and nickel plating functions just as well; I think I recall Consumer Reports offering that appraisal. Is that what we're talking about here?
So I guess the question really comes down to what is the minimum thickness for gold that is visible and will look like gold without any need to function like gold. I have heard that 7 millionths of an inch, or 0.18 microns of gold is visible. So I guess that at 0.03-0.06 microns it might be visible and exhibit a faintly gold look.
Still, it should be remembered that if the material cost of gold as plated is $120 per gram, or about $2300 per cm^3 of gold, then $2.30 of gold (0.001 cc) would cover 1 square meters at 0.1 micron thick, so we're probably not talking actual savings by going down to 0.03 microns; let alone going from 0.03 to .01 or .005 microns.
A wild guess of why your plater is being non-responsive is because you've given him the impression that you expect significantly lower prices for this significantly thinner plating? ... whereas at those thicknesses the cost of the gold itself is actually an insignificant part of his costs. Further, the principal difference between a successful money-making plating shop vs one which is losing money is the percentage of rejects, and plating at these crazy low thicknesses will surely cause the reject rate to escalate. Best of luck!
Regards,
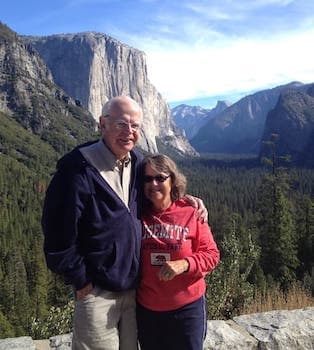
Ted Mooney, P.E. RET
Striving to live Aloha
finishing.com - Pine Beach, New Jersey
Q, A, or Comment on THIS thread -or- Start a NEW Thread