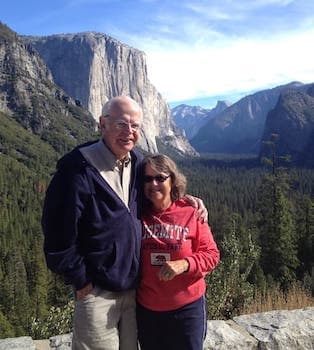
Curated with aloha by
Ted Mooney, P.E. RET
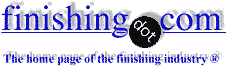
The authoritative public forum
for Metal Finishing 1989-2025
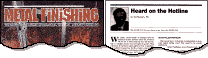
-----
How to rework PCBs with signs of corrosion
March 3, 2015
Q. Hi All, I have PCB boards detected with signs of corrosion. The boards are with Immersion Ag finishing and passed through wave soldering process. Do you know of any rework method that I can use to save those boards and any supplier who performs such rework?
Also, any test that helps to verify the reliability risk after the rework?
Thanks in advance for your time and feedback!
- Penang, Malaysia
March 8, 2015
A. Hello, because the boards have already been through wave soldering it will be difficult to rework them. You could try making up a 10% solution of fluoboric acid, use a medium bristle brush, dip the brush in solution and scrub the surface. Rinse in DI water and dry immediately. Wear gloves and eye protection. I don't know what type of components that have been wave soldered, so I won't suggest full immersion.
Mark BakerProcess Engineer - Phoenix, Arizona USA
![]() |
March 10, 2015 Q. Hi Baker, many thanks for the suggestion. The corrosion signs were detected at different locations of the PCBA such as in the vias with mostly at BGA locations. - Penang, Malaysia A. Unless you know what the corrosion is, chemical dipping could cause even more problems. ![]() Geoff Smith Hampshire, England March 9, 2015 |
March 22, 2015
Q. Thanks Geoff.
Sorry for the delayed response as my gmail was down on last 2 weeks and thanks for the input.
i do have the similar concern for the chemical dipping as one of the key root cause of this issue is contributed by the excessive flux that was not properly handled during the process.
Thus, tried to gather as much as possible methods and will approach that with lowest risk.
- Penang, Malaysia
Q, A, or Comment on THIS thread -or- Start a NEW Thread