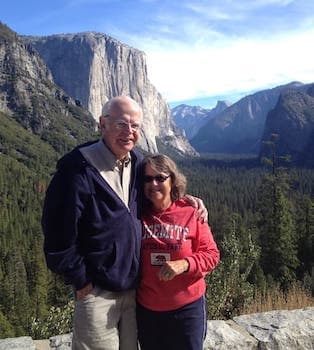
Curated with aloha by
Ted Mooney, P.E. RET
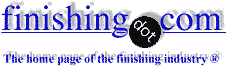
The authoritative public forum
for Metal Finishing 1989-2025
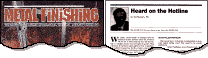
-----
Powder Coating plus Galvanizing Problems and Their Solutions
Q. I have been asked to powdercoat 6 mm galvanized steel for a major roadworks contract, they call up a powder coating spec, AS/NZS 4506 Class 3 and Class 5, or BS 6497 to be used, I am having trouble finding these spec's, can you or anyone reading this help.
At the moment, we clean the galv surfaces with a phosphoric acid wash, then dip in a chromate pre-treatment and then de-gas and powdercoat. This works for us and testing shows 1000+ hour salt spray. However I must paint to the spec the customer requires and supply a certificate of conformance with the finished product, so I need to know what the actual spec is.
Any help would be appreciated.
Regards
Mark Michelenamel finishes - Sydney, NSW, Australia
2005
May 31, 2009
A. Hi, Mark. We linked your mention of BS 6497 to a source for that one. Regarding AS/NZS 4506, Standards New Zealand warns that "This document has been withdrawn without replacement" ... so hopefully your customer will accept the current spec and forget the withdrawn one :-)
Regards,
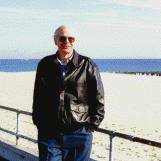
Ted Mooney, P.E.
Striving to live Aloha
finishing.com - Pine Beach, New Jersey
Galvanize/primer/powder coat
Q. I am a supervisor for pole manufacturing company in Ontario Canada, I would like to know if putting primer on galvanize and then powder coating, would it help the gassing out faster?
Ansel Richardssteel - Ontario, Canada
2005
2005
I am not sure if you are referring to a powder primer or a liquid paint. Before attempting a two-coat process, you might switch to a TGIC Polyester coating, and see if that eliminates the problem. TGIC coatings allow the gasses to pass through the liquid coating much better than Urethanes (during the cure process).
What chemistry are you using?
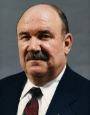
Daryl Spindler, CEF
decorative nickel-chrome plating - Greenbrier, Tennessee
Q. Plan to start a commercial vehicle manufacturing unit in India which will go online in late 2006. We plan to use metallic color powder coatings instead of wet paint as exterior and interior paint on both the driver's cabin as well as the cargo body. What specifications would you recommend as the best?
Ashlyn AntonyAuto manufacturing - Kerala, India
2005
2005
A. Sorry for the delay in getting back to you - I was on Holiday for a few weeks.
There are three types of powder coatings that do well in exterior use: TGIC Polyester, Polyester Urethane and Acrylic.
Aluminum wheel manufacturers apply a base coat of TGIC polyester powder, machine the wheels, and then apply an acrylic top coat to provide gloss and to protect the exposed aluminum. Acrylic powders contaminate the polyester products, and cannot be sprayed in the same booth. It has been my experience that the ventilation must be such that the acrylic cannot drift over to the TGIC booth in the air.
The TGIC Polyester base coat may allow the outgassing from the galvanize to occur through the powder as it liquefies, and prevent a problem with subsequent coatings.
You should perhaps discuss this application with a powder coating manufacturer to discover what kinds of problems might occur, and get some kind of commitment from them in terms of performance.
Automotive manufacturers are using powder coatings over frames, engine blocks and other non-exposed parts, but not so much on the body of the vehicle.
My experience has been that for a decorative finish you would be much better off using a liquid primer followed by a catalyzed liquid acrylic or urethane top coat.
Is your reason for using powder coating environmental?
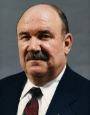
Daryl Spindler, CEF
decorative nickel-chrome plating - Greenbrier, Tennessee
Improving adhesion of TGIC powder on hot dip galvanized steel
Q. Are there any products that would improve the adhesion of our powder coating over newly hot-dip galvanized steel that does not have major environmental issues or require the use of an automated 5 stage wash system?
We are a manufacturer of steel products in Phoenix, Arizona. Our products are used in the Phoenix area only and normally we do not have issues with serious rust issues since our climate is very dry. Our powder coating is done in house and is a simple batch booth and oven. Our cleaning process is simple. After cutting, all components are hand washed with a degreaser/cleaner. After fabrication and before powder coating we use a manual power washer to clean off any soot from the welds. This has worked very well in Phoenix and the rust that we do get is surface rusting from scratches to the finish.
We have been interested in offering our product nationally, however, as we currently finish our product, I would not want to offer it as is. We have been researching hot-dip galvanize after our fabrication is done and then powder coating. We have done some tests with our TGIC powder over freshly galvanized product and mostly it has been very good but we have noticed a few failures in adhesion. Our galvanizer recommends a zinc phosphate pretreatment, but we worry about the environmental issues and the necessary equipment. One powder supplier recommended Picklex®
[affil links] but after talking to the company, I feel it is too expensive since the manufacturer told me I could not dilute it.
fence company - Phoenix, Arizona
2006
A. Hi Scott,
You are getting good advice from your galvanizer. If your products are going to be offered nationally, then they will see many environments that are more corrosive than the climate in Phoenix.
Zinc phosphating is the pretreatment of choice for galvanized surfaces, but you might be successful with an iron phosphate system that utilizes a high-performing final rinse. If you are using a high-quality powder coating, all the better.
- Naperville, Illinois
2006
A. Hi Scott. George is right. You really should have a phosphatizing pretreatment whether or not the metal is galvanized. It's important for a lot of reasons . . . it's just that its importance is most quickly perceived on galvanized work because it also improves the paint adhesion.
As for the environmental impact of proper finishing, please consider the billions of dollars of annual corrosion, the countless acres wasted to junk yards and ugly scrap piles, and the continuous and unsustainable waste in re-mining, re-smelting, re-manufacturing, re-packaging, re-transporting, re-selling, and then landfilling millions of tons of metal items to replace improperly finished junk that only lasts a couple of years when it would have easily lasted decades if finished properly.
Phosphates are environmental round-off error! Don't ever let anyone talk you into the penny-wise & pound-ludicrous proposition that easily avoidable early corrosion and unsustainable constant replacement is environmentally preferable to the tiny environmental footprint of proper metal finishing. It is a disgrace when environmental groups focus on the ounce of phosphate while ignoring the tons of steel it saves.
Regards,
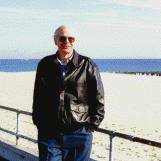
Ted Mooney, P.E.
Striving to live Aloha
finishing.com - Pine Beach, New Jersey
March 1, 2013
Why would 16 month old hot dipped galvanised powder coated gates rust?
July 22, 2014Q. I have a linear gate that is 16 months old. I have now noticed that there is considerable corrosion on the 26 mm x 1.5 mm upright bars and the upper and lower beams.
According to the instruction manual supplied with the gate, all steel is hot dip galvanised and powder coated (I would expect at least 20 years), yet the manufacturer's website for the product states "Hot Spray Galvanise".
The rust is red which I believe would indicate that the base steel has corroded and worked thru both protective coatings, or am I on the wrong track?
Any advise really appreciated
Facilities Manager - Fareham, Hampshire, UK
A. Hi Phillipe. I can see in the background of that photo something else: galvanized guardrails. Certainly your galvanized plus powder coated fencing should be expected to be in in at least as good shape as guardrails they were only galvanized. It sure looks like that fencing is utterly unsatisfactory. Additionally, either the fencing is hot dip galvanized or it's not (I suspect not), and the manufacturer certainly ought to know what they are selling.
Regards,
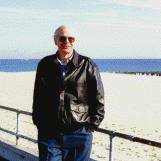
Ted Mooney, P.E.
Striving to live Aloha
finishing.com - Pine Beach, New Jersey
July 2014
July 25, 2014
A. I believe the devil is in the detail.
"Hot Spray Galvanising"?
I strongly suspect that the structure has not been Hot Dip Galvanised at all.
I can imagine that it has been given a thermal spray.
This is totally inappropriate for a tubular structure.
Obviously, the thermally sprayed Zn has no chance of entering the hollows.
That accounts for the red rust forming from the apertures into the hollows.
Less easily explained is the red rust forming on the vertical external members.
Perhaps these were undersprayed with the Zn coating?
Whoever did this job can only be described as a rank amateur.
In OZ we have a Fair Trading Department of Govt.
Any Building product supplied is deemed to have a 7 year minimum implicit warranty.
This is regardless of any other condition of contract.
I suggest that the goods you have are not of merchantable quality.
I hope your supplier, or his replacement, learns from this very obvious mistake.
Hope this helps,
Regards,
Bill
Trainer - Newcastle, NSW Australia
![]() |
July 2014
Regards, ![]() Ted Mooney, P.E. Striving to live Aloha finishing.com - Pine Beach, New Jersey A. Yes, Trainer - Newcastle, NSW Australia July 28, 2014 |
Many thanks for all your opinions; these have been taken on board.
Once again many thanks.
- Fareham.uk
July 25, 2014
A. This steelwork does not give any indication of having been galvanized.
With powder coated galvanized steel you don't get red rust. You might (in a poor powder coating job) get white rust, but not red.
It's not easy to tell if there's galvanizing under powder coating to an inexperienced eye, so would be easy to sell the job as if it had been galvanized.
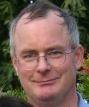
Geoff Crowley
Crithwood Ltd.
Westfield, Scotland, UK
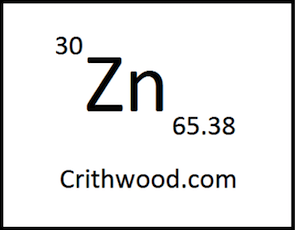
July 29, 2014
A. These pieces seem to be NOT hot dip galvanized, I can't see any drainage and ventilation holes on the vertical pipes.
Ozge SaracogluFreelance Metallurgical & Materials Eng. /IWE-EWE Welding Eng. - Turkey Izmir
September 25, 2014
Gentlemen, thank you for your constructive answers -- they are much appreciated. With all your doubts after some considerable time, the manufacturers sent a representative who agreed that the work was not of "satisfactory quality"; they have promised a new gate within 5 weeks. So once again thank you very much.
- fareham, Hampshire, United kingdom
September 26, 2014
----
Ed. note: Readers may also be interested in the more general topic of thread 1341, "Adhesion problems on hot dip galvanizing".

Q, A, or Comment on THIS thread -or- Start a NEW Thread