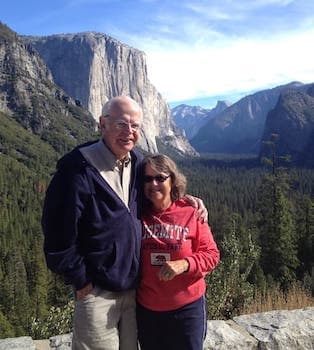
Curated with aloha by
Ted Mooney, P.E. RET
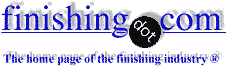
The authoritative public forum
for Metal Finishing 1989-2025
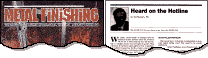
-----
Passivation problem on 4130 Steel
June 12, 2014
Q. We have a first article to submit to and aerospace company. Is a small pin that calls out for 4130 steel to be passivated per Type 6.
The parts came back from the platers today and the are completely deformed and tarnished, we will have to make them again but I want to make sure that there is no error in the drawing by asking for passivate on 4130 steel, we have never seen this requirement in 20+ years. My boss says 4130 is not "passivable" and I think that the type is what went wrong on this; I think the vendor performed type 2 which requires higher temp than type 6 and it over cooked the parts.
CNC Machine shop employee - Nogales Arizona USA
July 2014
A. Hi Ana. I think your boss is right. AISI 4130 is a low alloy steel, not a stainless steel. Low alloy steels cannot be 'passivated' in the same sense as stainless steels.
Regards,
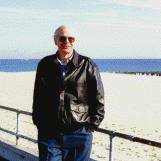
Ted Mooney, P.E.
Striving to live Aloha
finishing.com - Pine Beach, New Jersey
October 12, 2017
Q. Hello,
I too have a customer asking to passivate 4130 prior to Cad plating. Since we do not Cad Plate here my question is more for my interest than anything.
What would be the "normal" process?
Thanks,
Micheline
- Rincon, Georgia USA
A. Hi Micheline. The cad plating process is "normally" about the same as the zinc plating or zinc alloy plating process except with a cadmium plating tank substituting for the zinc plating tank, i.e., usually something like:
Soak Clean - Electroclean - Acid Dip - Plating Tank - optional Nitric Acid Brightening - Chromate Conversion Coating ... with appropriate rinsing between each step.
Conventionally, cadmium plating has been cyanide based and to a large extent still is, but there are acid-based cadmium processes available.
Regards,
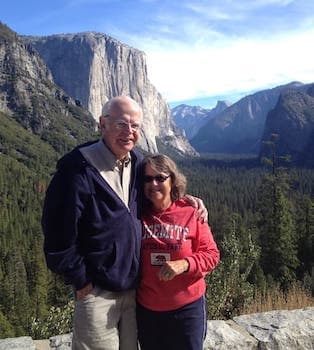
Ted Mooney, P.E. RET
Striving to live Aloha
finishing.com - Pine Beach, New Jersey
October 2017
October 12, 2017
Q. Thanks,
One more question. What is the typical make-up of the acid dip?
- Rincon, Georgia USA
A. Hi. Most acid dips for production plating are about 15% HCl. Obviously you need very good rinsing of the acid before entering a cyanide based plating tank. If you are doing cadmium sulphate though, some people would probably advise trying sulfuric acid for activation instead of HCl to minimize chloride contamination.
You probably realize these things, but for the benefit of newbies who may be reading this:
1. Remember that you don't build a production plating line based on theoretical reactions, but only after plating lab tests have demonstrated the viability of the process.
2. When you get a spec which doesn't make sense to you, like passivating low alloy steel, or passivation before electroplating, it's critical to try to sort it out with the specifier.
Regards,
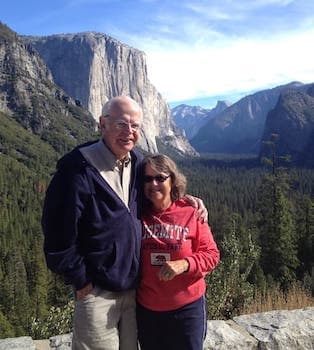
Ted Mooney, P.E. RET
Striving to live Aloha
finishing.com - Pine Beach, New Jersey
October 2017
Q, A, or Comment on THIS thread -or- Start a NEW Thread