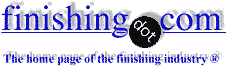
-----
"Shrinking" anodized parts
September 18, 2013
Q. I have a part that is building anodize coating but it is not increasing in size as expected per the 720 rule. When I run it at 15 ASF to build a 1 mil coating, the coating thickness comes out to be 0.8 mils but the part doesn't grow significantly in size. As I try to put more anodize on, it gets thicker, but the part stays the same size or even starts to shrink. I have ran parts up to 1.5 mils thick, but the part was only 0.3 mils bigger in diameter. The parts are dyed black so I need at least 0.8 mils.
It is 7075-T6, it is 19" long, 0.88" OD and 0.85" ID. Other parts from this same lot of material have anodized just fine. I've been running the parts on a titanium spring rack. I've run them at 7.5, 15 and 30 ASF. My tank is 22.1 oz/gal sulfuric acid and 65 F. This is the only part that I'm having this issue with, everything else is running as expected.
I initially thought I was running at to high of an amperage because the shape of the part was actually shielding most of the interior, but I still had the same problem at 7.5 ASF. The only solution I have is to make the parts to size and anodize.
Any other ideas? Thanks!
Chemist - Davenport, Iowa, USA
A. If they are being measured at the same temperature, I would suspect that you are losing metal in the pretreatment cycle.
I would take a couple of scrap parts, measure very carefully, process with the rest of the load up to just before going into the anodizing tank. Remove, rinse well and let set for several minutes and measure.
- Navarre, Florida
A. Justin
If you are not discounting surface area on the ID, you might be dissolving the anodize as fast as your are growing it. Assuming there are no intersecting side holes, your surface area is .72 sq. ft., but your effective surface area is closer to .41 sq. ft. To verify, run parts for 150, 225, & 300 amp-minutes each and look at the results. Your ASF affects the rate at which you grow the coating.
- Colorado Springs, Colorado
September 30, 2013
Q. I was measuring the parts just before they were being anodized but after the pretreatment was complete, basically as the rack was going into the anodizing tank. I ran the parts at 7.5 ASI because I thought maybe the ID was shielded by the OD due to the shape and it still dissolved the part during anodizing, I found the longer it ran, the more it would dissolve, but none dissolved in the first 15 minutes.
The day after I posted my question here, I ended up experimenting and running the parts in my hardcoat tank at the anodize current density. The parts anodized just fine. So I then dropped the tank temperature of my anodize tank from 65 to 55 F and the parts anodized just fine.
My thought is maybe I have too much surface area to volume (104 in2 : 0.78 in3) and that was somehow causing the surface to dissolve away as it was forming due to heat generated at the surface of the part? (Thin wire vs thick wire with same current running through it, the thin wire will heat up quicker) Has anybody else had this kind of experience with high area to low volume ratio parts?
Thanks for your replies!
- Davenport, Iowa, USA
Q, A, or Comment on THIS thread -or- Start a NEW Thread