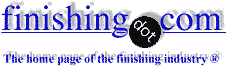
-----
Problems & Solutions with chemical coloring in automatic line
August 13, 2013
Q. Dear Sir,
I use chemical coloring in automatic line to color into gold anodized aluminum parts (chemically polished). The process is carried out correctly, but the parts from the lower rack are darker than those from the top. The rack length = 1 meter, and the coloring time = 45 seconds. The lower part enters and leaves the bath in additional time of 5 +5 seconds. What can be the problem?
Is the coloring bath too strong, or too fast?
electroplating - Bydgoszcz, Kujawsko-Pomorskie, Poland
A. Check the thickness from bottom of rack to top of rack. If the bottom is thicker, then it is adsorbing more dye, then experiment with shielding until you can get uniform thickness all over the rack.
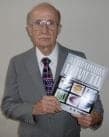
Robert H Probert
Robert H Probert Technical Services

Garner, North Carolina
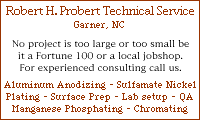
August 14, 2013
A. 3 things come to mind:
1. Parts on the bottom of the rack are getting a thicker coating (are you using a lead-lined tank by chance?)
2. Parts on the bottom of the rack are overheating during anodizing, causing larger pores, resulting in more dye absorption.
3. Uneven dye tank temperature (bottom of the dye tank is hotter than the middle/top). Easily solved by agitation/filtration.
45 seconds is way too fast in my opinion, it does sound like your bath is too strong. If the bottom part of your rack is in the bath for an additional 11% of the total dye time, I would think this definitely could be an issue with such a short dye time.
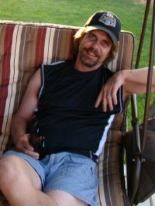
Marc Green
anodizer - Boise, Idaho
A. Karolina
If I read your post correctly, the bottom of the rack is seeing up to 25% longer dye time which could easily account for the variation. A longer immersion time will help reduce the variation but you will likely need to adjust the dye bath parameters to achieve the desired color.
- Colorado Springs, Colorado
Thank you all for your help. I'll follow your advice and try to fix the problem.
Kind regards
- Bydgoszcz, Poland
September 9, 2013
Q. My customer produces door handles; he uses AlMg3 alloy which consists of:
[(Fe0,07)(Si0,05)(Cu0,005)(Zn0,003)(Ti0,14)(Mn0,006)(Mg2,98)(Ni0,006)(Sn0,000)(Pb0,002)((Be0,004)((Cr0,001)(Al96,7)]
The heat/melt is low-pressure.
Unfortunately, the parts cannot be electropolished (sulfuric acid, phosphoric acid, 95 °C) and anodized.
After anodizing the parts are porous, coarse and do not shine.
The parts made of cold-drawn aluminium do not cause such problems.
Is it the matter of alloy composition? Is there any component missing?
I would really appreciate your help.
electroplating - Bydgoszcz, Kujawsko-pomorskie, Poland
Q, A, or Comment on THIS thread -or- Start a NEW Thread