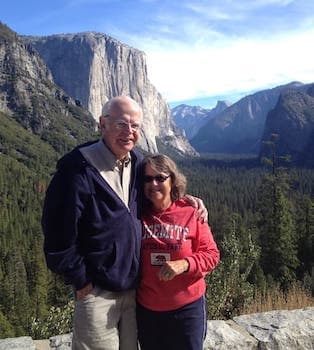
Curated with aloha by
Ted Mooney, P.E. RET
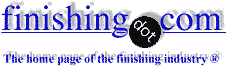
The authoritative public forum
for Metal Finishing 1989-2025
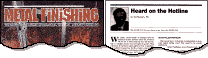
-----
Coating/plating for mild steel part that will survive 50 dishwasher cycles
July 23, 2013
Q. Hi,
I have a mild steel ring with zinc plate and clear passivate glued to ABS on a washable part. The plating thickness is not specified on the drawing. I need the part to survive in the dishwasher for about 50 x 1 hour cycles. Am looking for advice on the best plating option, perhaps a sequence of finishing and any knowledge on minimum thickness.
I have to use mild steel as the substrate as the ring engages with a magnet in use on the product.
product designer - Melbourne, VIC, Australia
A. Hi Anthony. I may be missing something, but I think the component should be made of 18/0 stainless steel. This is magnetic and is the material that less expensive flatware is made of, so it will certainly be reasonably satisfactory for cleaning in a dishwasher. Good luck.
Regards,
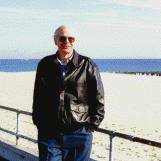
Ted Mooney, P.E.
Striving to live Aloha
finishing.com - Pine Beach, New Jersey
July 2013
A. I thought that flatware was 18/8, not 18/0.
James Watts- Navarre, Florida
A. Hi Jim. Both 18/0 and 18/8 have been widely used for a long time. Because of the high cost of nickel, and the desire of some people for nickel-free stainless, the 18/0 is increasingly popular especially at the low end. Oneida for example switched many of their traditional 18/8 patterns to 18/0 (www.oneida.com/buying-guides/flatware-buying-guide).
Regards,
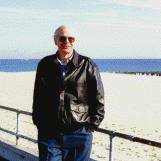
Ted Mooney, P.E.
Striving to live Aloha
finishing.com - Pine Beach, New Jersey
July 2013
July 30, 2013
Q. Hi Ted,
Thanks for the advice. I have looked at 430 stainless but the problem is that the non-austenitic grades do exhibit spot red rust in the dishwasher but more importantly for my application, the magnetic permeability of stainless is around 1000 G/Oe compared to around 2000 G/Oe for mild steel. I need to have the higher value, hence wishing to pursue a plating approach. I have done some investigation on combination of Zn and sealant coatings which may be good enough. I would greatly appreciate any advice on how to specify these.
Thanks
Anthony
- Melbourne, VIC, Australia
A. Hi Anthony. You are probably limited to RoHS-compatible trivalent chromating on the zinc plating. The severity of this duty cycle probably hinges upon which dishwasher detergent is used, as both lemon detergent and alkalis (some are stronger than others) attack zinc plating.
The thickness of the zinc plating across the surface of the part tends to vary widely, so you probably need to specify the minimum thickness rather than the average. It is usual to specify the minimum for any area that can be touched by a 3/4 inch diameter ball, but I'm not sure whether that would be a good spec for your particular part.
Unless cost is critical, I would probably specify a minimum thickness of 0.0004" touchable by the ball. This is not based on knowledge of what thickness would actually survive for 50 cycles (I don't know), but simply to make sure your parts are not handled as "commercial zinc finish" -- not a real spec, but a common industry synonym for "cheap", with a thickness of 0.00015" - 0.0002" and sometimes priced by the pound and produced with no real expectation of durability.
There are many available specs for zinc plating; probably ASTM B633 is the most common. Good luck.
Regards,
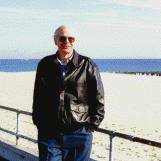
Ted Mooney, P.E.
Striving to live Aloha
finishing.com - Pine Beach, New Jersey
July 2013
Hi Ted,
Just to close off. We tried increasing the Zinc thickness as proposed and yes it delays the time to white rust. Probably good enough for our application but marginal. We also tried Nickel plating and this worked much better, however Nickel is hard to glue to the ABS substrate. In the end we have used SUS 441, it offers enough magnetic coupling for our purpose and of course is more robust in the dishwasher.
- Melbourne, Australia
A. What about color anodizing? 400-series color well. It will survive dishwasher cycles, since it survives high pressure sterilization of color-coded medical instruments.
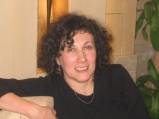
Anna Berkovich
Russamer Lab

Pittsburgh, Pennsylvania
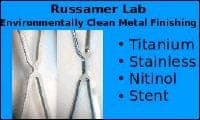
September 11, 2013
Q, A, or Comment on THIS thread -or- Start a NEW Thread