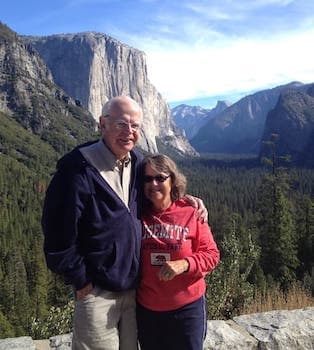
Curated with aloha by
Ted Mooney, P.E. RET
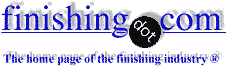
The authoritative public forum
for Metal Finishing 1989-2025
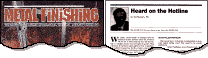
-----
How to make large diameter, super thin copper dish
May 21, 2013
Q. Hello,
The part I want made is a rather extreme part and it is very tough to
manufacture, I have been having a lot of trouble finding any suppliers
that believe they have the capability to create this, so if anyone can
do it, or can recommend someone else, please do!
Anyway, what it is that I am looking to create a 52" diameter,
10" deep copper "dish", with a final thickness of
0.0007".
I'm really looking for whatever fabrication process that could make
this work. I've looked into Hydroforming, Metal Spinning, Stamping,
Electroforming, Electroplating, Chemical Vapor Deposition...
This is very new for me and my company so if anyone things that a part
like this is within their capabilities, or if anyone has any
suggestions for any special manufacturing considerations, alternate
fabrication techniques, viability of different processes, etc. please
feel free to share them!
Thanks in advance!
- Rochester, New York, USA
A. Hi Peter. I'm confident that it can be done by electroforming,
and pretty confident that electroforming is the best approach.
You'd need to start with a 52" dia., 10" deep panhead
mandrel made of aluminum, stainless or even wax and then electroform
the copper onto it. The advantage of stainless steel is that it would
be reusable to make thousands of the electroformed dishes; the
disadvantage is it sounds very difficult to remove such a large
delicate object from the mandrel even if the adhesion is very low. The
advantage of aluminum is that it can be dissolved away in caustic
soda.
The thinnest, flimsiest strip in many feeler gauge sets is
.002", and your dish is 3x thinner, so it's really thin, and hard to
imagine how you're going to handle it except by keeping it on the 52"
dia., 10" deep panhead mandrel anyway :-)
NASA and/or their contractors in Huntsville, AL have
electroformed rather similar objects. Try Binging or Googling
"Darell Engelhaupt". Good luck.
Regards,
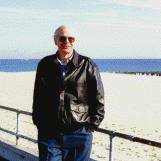
Ted Mooney, P.E.
Striving to live Aloha
finishing.com - Pine Beach, New Jersey
A. Just to follow up on what Ted said: This is a relatively straightforward electroforming job. Depending on how uniform the final thickness must be, you'll likely need some specially shaped anodes and/or shields, however much more complex shapes are electroformed every day.
The question is - how do you support and handle this without a backing/reinforcement? I can only imagine that you simply leave it attached to the mandrel, which could be metal or one of many plastics.
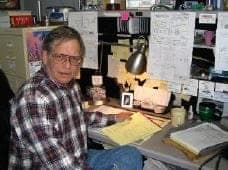
Jeffrey Holmes, CEF
Spartanburg, South Carolina
First of two simultaneous responses -- May 25, 2013
A. I agree with Ted. Electroform is the obvious answer to the question as asked, although obtaining a constant thickness on this size may need a little trial.
But that is only the start of your problems. How are you proposing to handle, store, transport, mount it etc.?
I have many times been given similar jobs, only to find that the real problem is entirely different and requires an entirely different approach.
If, for example, you intend to mount this on a ring, then that could be part of the mandrel design and become an integral part of the electroform. One example I was given involved making a similar thin and delicate part which then had to be glued to a support. The solution was to simply plate onto the final support and eliminate the near impossible gluing stage.
You will need to share much more information before you can expect useful guidance.
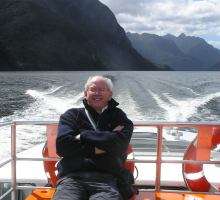
Geoff Smith
Hampshire, England
Second of two simultaneous responses -- May 28, 2013
adv.: Supplier of Copper Anodes, Nickel Anodes, Bismuth Metal, & Other Metal Products for Industry & The Arts
Q, A, or Comment on THIS thread -or- Start a NEW Thread