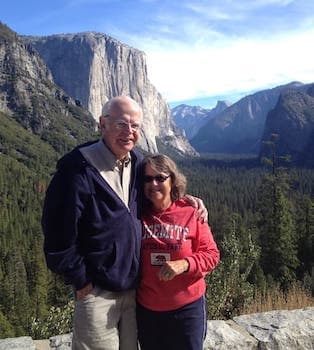
Curated with aloha by
Ted Mooney, P.E. RET
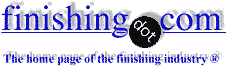
The authoritative public forum
for Metal Finishing 1989-2025
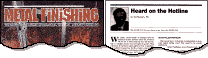
-----
Protecting chuck from corrosion when doing brush plating on lathe- mounted work
April 10, 2013
Q. I operate a nickel brush plating operation for restoring mounting surfaces of bearing components. The components to be plated are held in a steel 3 jaw lathe chuck which is mounted to a turning head spindle. The chuck is exposed to plating chemicals which include acid for etching. The acid attacks the steel surfaces of the chuck and causes corrosion/difficult operation. Is there an inert protective coating that can be applied to the chuck surfaces to prevent corrosion? I have been using Teflon but the coating quickly breaks down on sliding surfaces within the chuck.
Thanks to anyone for advice.
Toolmaker - Whittier, California, USA
A. Hi Mike. Electroless nickel, or an electroless nickel with Teflon process sounds promising to me. Good luck.
Regards,
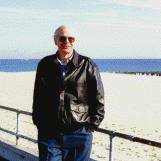
Ted Mooney, P.E.
Striving to live Aloha
finishing.com - Pine Beach, New Jersey
April 11, 2013
A. I would only recommend electroless nickel if the chuck and its internal parts are made of wrought steel. In such case the layer should be rather thick, around 0.003".
If it is cast steel or worst, cast iron, EN will surely fail very soon due to the porous nature of castings. Another option would be a 0.005" thick layer of an elastic nickel such as Watts or sulphamate (over 0.005" or more) applied over properly undersized surfaces followed by a careful re-machining to original dimensions. If you can find and afford it, your best choice would be a stainless steel chuck.
Monterrey, NL, Mexico
Q, A, or Comment on THIS thread -or- Start a NEW Thread