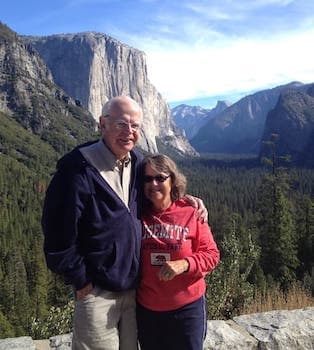
Curated with aloha by
Ted Mooney, P.E. RET
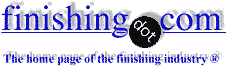
The authoritative public forum
for Metal Finishing 1989-2025
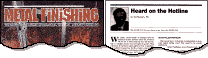
-----
Acid Copper Plating over Zinc
March 21, 2013
Q. Good morning, afternoon, or evening!
After meddling, reading, and experimenting I think I have all the stuff I need to finally do this, but first I need some feedback.
I'm wanting to plate copper or nickel on to some leaves and seed pods that a friend of mine brought back from a rain-forest in Central America.
The current plan is to vacuum stabilize the material using a thermostabilizing polyester resin, apply a conductive zinc paint (Cold Galvanizing Compound. I tested it previously, it works), and plate.
I'm thinking that a high throw acid copper bath would be best for the initial plate on both, but I'm not sure it would work.
The proposed bath composition for the acid copper is as follows.
75g/L Copper sulphate
188g/L Sulfuric Acid
60ppm Chloride
I'll be shooting for 2 A/dm^2, for the current density.
For the nickel I'm going to be using a 'Bright' Watts bath over the initial copper.
240 g/L Nickel sulphate
60 g/L Nickel chloride
45 g/L Boric acid 45 g/L
Shooting for 4 A/dm^2 current density.
Now, besides the obvious 'do you think it will work' question, I'm wondering if any of you have done something like this on the small scale?
I'm not dealing with large volumes, usually I'm dealing with 500 mL or less of plating solution, which makes the agitation and circulation of the bath MUCH easier. With these smaller volumes I am curious to know if excessive circulation of the plating bath will cause any problems, the filter setup I have right now is running at 3 L per hour. So is the higher circulation going to cause any issues?
Last question, I've yet to locate any sources or information regarding wetting agents for this project. Honestly I'm unsure if they are necessary for such small batch stuff running at lower power, but why haven't I been able to find any? Propitiatory again?
I've spent years reading on this forum, I think this is actually the first time I've asked a 'real' technical electroplating question.
So let me take a moment to address two things:
1. Thank you all for inadvertently educating me in the chemistry and curiosity related to this field.
2. I have a proper lab setup and disposal plan. I don't want to release this stuff into the environment.
Blacksmith - Boone, North Carolina, USA
A. Good day Mark.
Wow, cool idea about plating on the pods. I think 500 ml solutions are extremely small given the surface areas and time you will be plating. Concentrations will change quickly and dramatically.
3 L per hour filtration = 6 bath turnovers, that's quite impressive.(Hope your parts won't go swimming)
Yes, wetters are proprietary, as are brighteners for both copper and nickel. (Saccharin and formaldehydes do comprise brightener components for nickel- BUT you didn't read it here!) Mechanical burnishing may help here.
Plating acid copper directly on zinc will prove to be problematic, given the acidic nature of the copper solution attack on zinc based substrate.
Normally, a barrier plating of cyanide copper is required to "seal" the zinc prior to acid copper.(You DON'T want to go the cyanide route based on your lab scale!)
Why not try nickel only as an initial strike to seal the items,acid copper to build thickness. Burnish to brightness/smoothness, and finish with nickel again.Good cleaning, rinsing between solutions.
I understand you have a proper lab set-up, indicating you are familiar with electroplating and are conscientious regarding disposal.
KUDOS TO YOU!
Hope I didn't blow the wind out of your sails, and best of luck on your project!
Regards,
- Toronto, Ontario, Canada
Second of two simultaneous responses -- March 22, 2013
Q. As an additional to to the previous, the cold galvanizing spray paint is only 93% zinc with the remainder being composed of the solvent, propellant, and adhesive.
Yesterday I made my first attempt. The zinc coating, while conductive, immediately dissolved in the copper bath. I've decided to call that one a beta test, I'm thinking that the acid concentration in solution was too high. What would you suggest as a pH buffer?
Blacksmith - Boone, North Carolina, USA
Eric, what you say there makes a great deal of sense. I'll try doing a nickel strike before the copper plating, makes a good bit of sense.
All the same though I'm having a heck of a good time fiddling with this.
Blacksmith - Boone, North Carolina, USA
A. Good day Marc.
Unfortunately, you cannot buffer an acid copper solution.(The sulfuric gives it the throw)
But, you can "buffer" a nickel solution, i.e., run a watt's nickel at elevated pH -- say 4.6-4.8. This pH will render the efficiency somewhat slower, however all you are attempting to do is lay down some metal to "seal" the zinc prior to acid copper where you are building thickness etc.
Also , there are formulations of other nickel solutions which may suit your purpose, i.e., sulphamate runs at higher pH values.
Don't forget the zinc deposit you have sprayed is EXTREMELY thin in nature, and within it are non-conductive elements.(Years ago I have used nitrocellulose lacquer and "dusted" the parts with graphite powder while the lacquer was still "wet" to gain some measure of conductivity/metallizing prior to plating)
I think 4 A/dm 2 (40 ASF) is too high, it will "burn" off/through the Zn to the substrate.
Maybe 0.5-1-0 A/dm 2 to start to get deposition started and later increase for thickness.
Hope this helps (there are MANY ways to skin a cat/fillet a fish/etc.......)
Regards,
- Toronto, Ontario, Canada
Third of three simultaneous letters -- March 22, 2013
Q. Would a standard Wood's strike bath work?
Bath formulation as follows:
45g/L Nickel Chloride
100ml/L HCl
1.5 A/dm^2 for current density.
Ref: https://www.pfonline.com/articles/woods-nickel-strike
Marc Banks
Blacksmith - Boone, North Carolina, USA
A. Good day Marc.
We need to remember that HCl will strip zinc/zinc plated items. Wood's @ 10% HCl will strip Zn. Normally, plating on Zn requires an acid for activation, H2SO4 @ 0.5-1.0%. Avoid acidic/low ph solutions for plating zinc/zinc alloys. Again, I will reiterate using a higher pH plating solution, such as a Watt's Ni at 300 g/l NiSO4, 40 g/l NiCl (keep it low=Cl will cause base metal attack), 38 g/l H3BO3 at elevated pH values, or even a sulfamate/ semi bright Ni. Hope this helps and good luck.
Regards,
- Toronto, Ontario, Canada
Second of two simultaneous responses -- March 25, 2013
Q. Eric,
Good call on buffering the pH of the Watts bath, getting much better results. Still not 100% happy with the results, but it's quite good at this point.
I took a shot at a Wood's strike bath; didn't come out well at all.
Blacksmith - Boone, North Carolina, USA
A. Hi Marc. A Wood's bath is needlessly aggressive and inefficient. It's purpose is to activate stainless steel or old nickel plating by attacking and dissolving it while simultaneously depositing a very thin fresh coat of nickel. Not to be confused with Watts bath, which is "standard" nickel plating.
Regards,
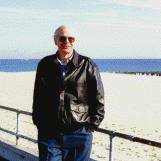
Ted Mooney, P.E.
Striving to live Aloha
finishing.com - Pine Beach, New Jersey
March 26, 2013
March 26, 2013
Q. I've been having a consistent problem with the plating peeling off from the surface on the actual pods.
I sealed them using a vacuum stabilization process, but I think that my problem lies there.
I think that they didn't seal as well as I had hoped, so the plating solution is getting behind them and oxidizing the woody material behind the zinc. I think that it was an issue with some of the waxy coating on the seed pods.
Test pieces that were not the seed pods came out rather well using an electroless alkaline nickel strike.
Ref: http://www.nickelinstitute.org/~/Media/Files/TechnicalLiterature/ElectrolessNickelCoatings_10055_.pdf
Marc Banks
Blacksmith - Boone, North Carolina, USA
A. There are readily available conductive paints consisting of copper powder in an acrylic base, made for what you are trying to do. ("Safer Solutions" is one) You can plate directly out of an acid copper bath and avoid adding an additional step. Probably cheaper and safer to just buy the right conductive paint, than adding a nickel strike. Sealing of organic items to be plated is recommended by some, I can't say as I mostly plate non-porous items.
Taylor Markow- Eugene, Oregon, USA
A.
----- Render surface conductive:
Lacquer plus graphite or copper dust
Buy a conductive paint that serves for that purpose I know that they exist but no idea where you can get those.
Could be used metallization with silver?
Palladium chloride activator? one step or two steps to create nucleation sites.
----- Apply a layer of electroless bath to make a conductive film if you have not created it yet:
Electroless copper
Electroless nickel
If you applied a layer of zinc you can choose an alkaline nickel or cyanide copper or electroless baths but they must not affect the layer of zinc.
Using the Watts bath over zinc will contaminate it due to zinc attack because of the acidity of Watts bath.
- Bucaramanga Colombia
A. Woods strike will not work. You could try a sulfamate strike at the highest allowable pH and go in hot.
Sulfamate at the higher pH plates much faster and thicker, so you might get away with it.
- Navarre, Florida
May 9, 2020
Q. Peace unto you; good day sir, my name is Ron, I am a coin collector. I've been trying to plate some old Nazi coins to restore them. From reading some of your answers, perhaps my volts are too high. I'm using 4, 1.5 volt batteries in a vinegar ⇦in bulk on eBay or Amazon [affil links] and peroxide. Coins show copper on it but then came right off when I tried to clean it up a little. Should I go to 3 or even 2 batteries? Also, I've read sugar in the bath helps produce a shine, is that true. What would you suggest I try. By the way, these are zinc coins. I think they should be treated with copper, then a silver like outer plate.
Ron Dolinar- Jacksonville, Florida.
A. Hi Ron. You posted your question on a thread about choosing the right voltage for plating, but we moved it here because the heart of it is that you can't acid copper plate onto zinc at any voltage because the copper will immersion-deposit (very little adhesion) even with no electricity applied.
In industry, the usual approach is to cyanide copper plate, but cyanide plating is so dangerous as to be out of the question for hobbyists. Another approach is a proprietary alkaline copper plating solution from EPI / Electrochemical Products Inc. [a finishing.com supporting advertiser] and possibly others. There was a patent (US3082156A) for nickel plating on zinc die castings, and decades ago I saw similar proprietary nickel plating on zinc diecastings but I don't know if anyone offers it today or not.
Regards,
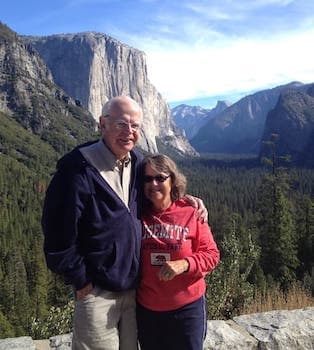
Ted Mooney, P.E. RET
Striving to live Aloha
finishing.com - Pine Beach, New Jersey
May 2020
May 16, 2020
A. 19th-century cyanide-free copper plating solution: Tartrate based copper plating bath.
copper sulphate
⇦ this on
eBay or
Amazon [affil links] 35-40 gms,
Potassium sodium tartrate
⇦ this on
eBay
or
Amazon [affil links]
180-190 gms,
sodium hydroxide 50-60gms,
20 °C temp.
0,3-1,5 A/dm2
Hope it helps and good luck!
- Zagreb, Croatia
Thanks Goran! I was aware of the use of potassium sodium tartrate (Rochelle Salt) in cyanide copper plating, where it assists the cyanide in complexing the copper, but had never heard of using it without cyanide as you've introduced here. I wouldn't be terribly optimistic about its ultimate ability to produce satisfactory copper plating on zinc diecastings, but Rochelle salt is so harmless that it's certainly worth adding to the experiments :-)
Regards,
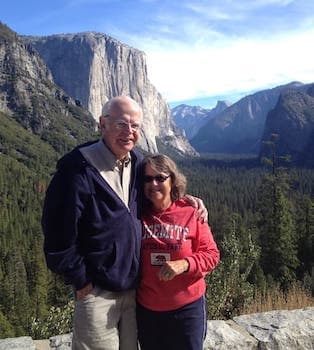
Ted Mooney, P.E. RET
Striving to live Aloha
finishing.com - Pine Beach, New Jersey
May 2020
May 17, 2020
A. That is only recipe from old book (A Complete Treatise on the Electro-deposition of Metals by G.Langbein, New York 1891, page 186), so called Weils copper solution. As far as I Know before 70 -60 years Russians published small monograph on tartrate based plating solutions. Useful link:
https://www.researchgate.net/publication/268362604_Electrodeposition_of_Copper_from_Non-Cyanide_Alkaline_Solution_Containing_Tartrate
- Zagreb,Croatia
Thanks again Goran.
Regards,
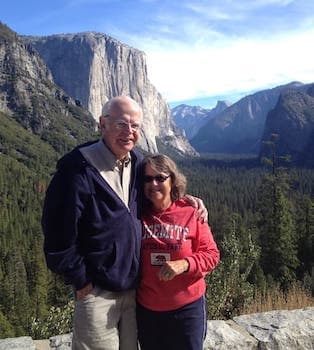
Ted Mooney, P.E. RET
Striving to live Aloha
finishing.com - Pine Beach, New Jersey
May 2020

Q, A, or Comment on THIS thread -or- Start a NEW Thread