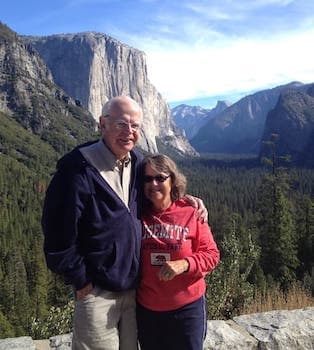
Curated with aloha by
Ted Mooney, P.E. RET
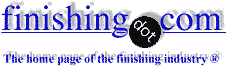
The authoritative public forum
for Metal Finishing 1989-2025
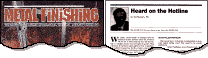
-----
I need an alternative to black hard anodize on 2024 aluminum
January 22, 2013
Q. We are a precision machine shop. Our customer manufactures blood centrifuge equipment. Because of the high G forces involved they have chosen to use 2024 aluminum forgings. The plating requirement is for .002" hard anodize dyed black and nickel acetate sealed. Out of the 4 key platers we use 3 have either burned parts or pitted them. I know it is very difficult to plate but we cannot afford to lose any due to the amount of time and material we have invested in the part. I want to discuss plating alternatives with our customer and would appreciate your professional feedback and suggestions. Coating thickness is critical so the print dimensions will not have to be modified.
I am looking for a coating thickness of .001" with excellent adhesion and moderate lubricity. There is also the factor of distortion of the material at high G forces. The coating cannot crack or peel. I am considering TFE Electroless Nickel as one alternative. What about an epoxy paint or some sort of powder coat. Can powder coat thickness be controlled to that extent? For security reasons I cannot attach a photograph.
Quality Manager - Auburn, California, USA
A. Hi. The electroless nickel plating with TFE sounds reasonable to me. Another alternative would be black e-coating; I'm sure it can be done with polyester e-coat, and I think epoxy e-coat is feasible as well. Good luck.
Regards,
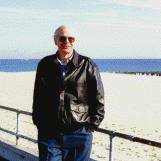
Ted Mooney, P.E.
Striving to live Aloha
finishing.com - Pine Beach, New Jersey
January 25, 2013
February 5, 2013
A. We have had good luck with hardcoating using some Clariant additives that allow you to hardcoat at elevated temperature without burning and provide a smoother surface RMA finish on the parts being processed. In fact we just took over a job where other people were burning/pitting some A356 alloy with conventional hardcoat. See if any of your local sources can provide that service. "It can be done!".
It may be worth noting that our line is of the "manual" variety where our trained people are continuously monitoring the process. A lot of times people lean too hard on the caustic etch and the surface finish is destroyed before it even hits the anodize bath.
It might be easier to work this angle than try to re-invent the wheel especially for a medical type application!
- Bridgman, Michigan USA
Q, A, or Comment on THIS thread -or- Start a NEW Thread