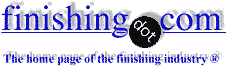
-----
Best attachment method for Rifle Gas Block
January 4, 2013
Q. Hello all. Total novice but curiosity is getting the best of me. Just a quick question for the experts. I am wanting to attach a sling swivel mount onto a rifle gas block.
Long story short the Ruger Mini 14 factory folders have their sling swivels already integrated on the side of the block. I would like to replace the existing Ruger factory gas block with an aftermarket adjustable ASI aluminum gas block. My question is; which method is best for trying to accomplish this? I would assume that welding might compromise the integrity of the stainless steel of the block and that could have catastrophic consequences (plus I've heard that stainless is tough to weld if you don't know what your doing, which would be me). Would brazing or solder be an option? Keep in mind that there are going to be high barrel and block temperatures to contend with which may effect the jointed area??? I also would assume that using an epoxy of some sort would not have the desired affect because of these high operating temperatures? I tried to do some research on temperatures affecting jointed areas but to be honest I'm not even sure hot the block and barrel get. Any thoughts or insights would be greatly appreciated. Thanks in advance.
-Tom
Hobbyist - Columbus, Ohio, USA
A. Tom,
Unfortunately you can't weld Stainless and Aluminum together (Well you can, but it requires a multi-million dollar friction stir machine and careful process control.) nor can you braze or solder aluminum and steel together.
But that doesn't matter since the mini 14 gas block is bolted on. You'll simply unscrew the four hex head bolts holding the old gas block together, this can be hard since Ruger deforms the ends of the factory screws to prevent them from backing out, then you take the new gas block and install it. Use new screws only, high temp loctite and torque the screws to 32-36 in/lbs (Try to use a wrench in in-lbs since 3 ft-lbs is going to be hard to control precisely.) Make sure to tighten the screws evenly otherwise you'll end up with sight windage issues, so if one side of the gap between the gas blocks is noticeably larger than the other you may want to back one side out one turn at a time and tighten the other side.
As to the general question of heat and joining processes, for most purposes brazing will be good enough. Most brazing takes place at around 1500-3000 °F, well above what anyone would let their rifle or pistol get too. Soldering however stops at 800 °F which a semi-auto battle rifle can easily reach furring sustained fire on a warm calm day. Now, Class III's which fire sustained full auto burst's can reach red hot heat, which is more than enough to weaken if not liquefy most brazing filler, and so attachments should be fitted via welding.
In no case should an end user try to solder, braze or weld anything onto his or her firearm though as the heat from the torch can and will distort and anneal the barrels, which is bad for accuracy and safety.
- Mt Clemens, Michigan, USA
Q, A, or Comment on THIS thread -or- Start a NEW Thread