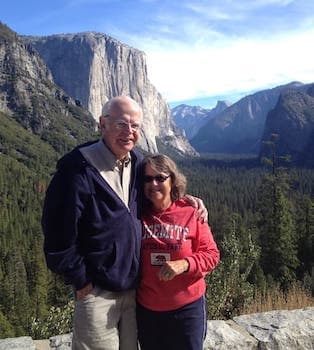
Curated with aloha by
Ted Mooney, P.E. RET
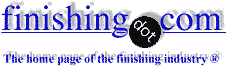
The authoritative public forum
for Metal Finishing 1989-2025
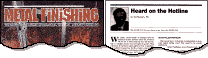
-----
Explanation of zinc phosphating theory
October 20, 2008
Q. Gentlemen, I have an Anodizing installation and am interested in starting a Zinc Phosphate line what are the similarities and differences.
John DeGarmoeAnodizing - Lancaster, Kentucky, USA
October 22, 2008
A. No comparison at all. Anodize is an electrolytic process while zinc phosphate is a chemical process.
While a proper formulation will put a light coat on aluminum for paint prep, it is virtually colorless and difficult to control visually. On steel, it imparts a definite color, so is easier to spot problems.
Abrasive blasting is the preferred method of providing a clean active surface. You can acid etch, but the rinse needs an additive to get a good coat.
I used a calcium modified zinc phosphate and got wonderful results. I would definitely start with a proprietary process.
- Navarre, Florida
A. Hi John.
Similarities:
They are both metal finishing processes, so some preliminary things are the same. Mechanical pretreatment may be necessary, and a poor finish can be the result of poor mechanical preparation.
They both involve a series of steps rather than a single process. Non-electrolytic alkaline cleaning is the first step. But the chemistry is usually stronger before zinc phosphating because it is done on steel parts which are more robust against strong alkali than aluminum parts.
Next is usually some form of acid dip in both cases, but with rinsing between each step.
The anodizing step uses electricity whereas zinc phosphatizing does not.
Finally there will be process steps after the anodizing or phosphating. It might be wax or oil or electropainting after phosphating vs. the dyeing and sealing you use in anodizing.
Differences:
Anodizing is done on aluminum, zinc phosphating is done on steel. Anodizing is an immersion process; zinc phosphating can be, but is often a spray process instead. The chemistry, the purpose, and the corrosion protection mechanisms are totally different.
Luck & Regards,
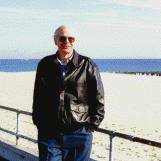
Ted Mooney, P.E.
Striving to live Aloha
finishing.com - Pine Beach, New Jersey
November 3, 2012
Q. I would like to understand the theory of standard zinc phosphating a little bit better. I am involved in powder coating. According to study material that I have, during the zinc phosphating process zinc phosphate crystals form at anodic points on a mild steel surface. Am I correct in assuming that this can be explained by saying that the mild steel surface is a mixture of two or more materials (like iron, carbon, manganese, etc) and that when immersed in the phosphate solution some sites on the surface will be anodic and other cathodic in relation to each other depending on the alloy mix in a particular area? The zinc phosphate is attracted to the anodic points again due to electrode potential?
Then going further the books say that to get a finer crystal which is desirable you need to create more anodic sites, so that more crystals crowd into the same space, and thus are smaller because they stop growing when they touch each other.
To achieve this the process of activation or conditioning is practiced. The study material I have informs that mildly alkaline suspensions of titanium salts may be included in a pre-dip directly prior to the zinc phosphate tank. This creates a large number of anodic sites on the mild steel surface to which the zinc will be attracted. What is the mechanism there? Does titanium loosely deposit onto the mild steel due to electrode potential as per the electrochemical series? Or if not, what attracts it to the surface?
I would really appreciate it if someone could explain the process to me in layman's terms.
In-House Finishing Shop Manager - Johannesburg, Gauteng, South Africa
A. Hi Dean,
You've got most of it correct. Two excellent research papers explain the phosphating process better than any I have read.
PE Tegehall & NG Vannerberg, "Nucleation and Formation of Zinc Phosphate Conversion Coating on Cold-Rolled Steel," Corrosion Science, v. 32, 635 (1991).
EL Gahli & RJA Potvin, "The Mechanism of Phosphating of Steel," Corrosion Science, v. 12, (583 (1972).
- Naperville, Illinois

Q, A, or Comment on THIS thread -or- Start a NEW Thread