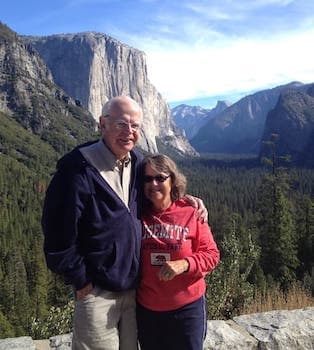
Curated with aloha by
Ted Mooney, P.E. RET
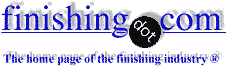
The authoritative public forum
for Metal Finishing 1989-2025
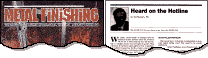
-----
Corrosion of SST Springs and Platings
Q. A torsion spring; We have used Elec. Nickel/Hi-Phos at .001 and only achieved 100hrs salt w/white and red rust on SQ music wire. Also Zinc Cobalt clear at .0005 an achieved 40 hrs salt. Have moved to 17-7 SST because of strength and corrosion issues. 1.) Should SST be passivated, or use Electropolishing? 2.) Is there a better way to approach corrosion resistance in correspondence to material selection? 3.) Special coatings, powder.....?
Info; Product is an external part, and under a continuous working load.
Info; Product is desired to have a working life of 10 years.
Any help would be appreciated.
Thanks
aerospace - Mpls, Minnesota USA
2000
A. Dan:
Surface finish and coatings for springs must take into account corrosion and mechanical issues. Reliable material and surface finishing specification cannot be developed from the information that your have provided. If you are using stainless steel, a passivation treatment of some kind is advised to obtain good corrosion resistance following heat treating, coiling, etc. Electropolishing is a great passivation treatment, but may be overkill for your application. I hope that you are aware that many surface coatings will diminish the fatigue resistance of your spring.
Good Luck.
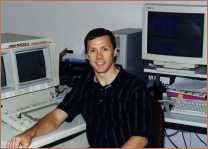
Larry Hanke
Minneapolis, Minnesota
2000
A. Dan: In order to obtain optimum corrosion resistance, you need to passivate the surface to increase the chromium to iron ration on the surface. The highest chrome oxide ratios can be obtained by using our CitriSurf products. It is a safe, easy process and gives the best results in most cases. In order to understand your exact conditions better in order to recommend a process to do this, please contact me. Regards,
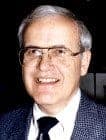

Lee Kremer
Stellar Solutions, Inc.

McHenry, Illinois
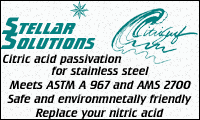
2000
A. Dear Colleague,
My recommendation would be to use a passivating solution of either nitric acid, or perhaps phosphoric acid.
I know the use of this chemistry incurs some attention to environmental issues, however, there is really no substitute for the correct technology.
citric acid will chelate free iron, but will not directly passivate the stainless steel surface.
Best regards,
- Australia
2000
Q, A, or Comment on THIS thread -or- Start a NEW Thread