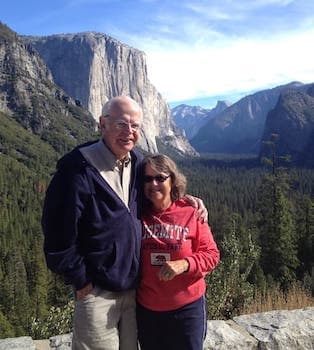
Curated with aloha by
Ted Mooney, P.E. RET
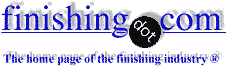
The authoritative public forum
for Metal Finishing 1989-2025
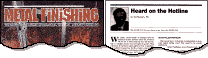
-----
Stainless Steel Corrosion Problem
I am working with a factory that produces stainless steel (304) wire mesh products. They claim that the steel is 18 Cr 8 Ni, yet the steel seems to corrode/rust during our tests in saline solution. I'm fairly new at this so I am trying to get a straight answer on the cause for this. Do SS wire mesh products of this sort need to be finished to prevent rusting? Is this a problem of poor finish or is it that the material is not what the factory says it is?
I appreciate any feedback that can be provided.
- San Francisco, California
2000
2000
Jeff,
May I suggest you approach a major supplier of s.s. ... one name that comes to mind is ATLAS STAINLESS STEELS of Welland, Ontario.
They have a very comprehensive catalogue and also corrosion data on the 400 and 300 series.
For salt brine, then 304 should fail, I'd think ... at least it would be easily attacked. Not enough nickel in it and too much iron!
I doubt that it is a question of 'finish' but of quality. And one pays more for quality, doesn't one?
Surely (have a look in your yellow pages for stainless suppliers) you have some s.s. mfgs in the USA who would have comparable corrosion resistance data. Try them. OK?
Cheers!
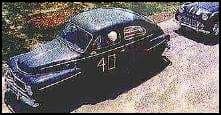
Freeman Newton [deceased]
(It is our sad duty to advise that Freeman passed away
April 21, 2012. R.I.P. old friend).
Jeff:
The stainless has to be passivated. Welded wire mesh is especially difficult to process due to the material overlap. I would be happy to process some samples for you to help overcome problem.
- Toccoa, Georgia
2000
The problem could be with the material or surface condition. Dan is correct that the best corrosion resistance will be obtained if the SS is passivated and that the mesh is a problem because of the overlapping wires. Passivation will not help if you have the wrong material or if severe surface contamination is present.
It is also possible that the test method is inappropriate for this material. Have you successfully tested similar materials with the same test method? Because of the crevices formed by the overlapping wires of the mesh, even passivated 304 will eventually corrode in a strong saline solution. Analysis of the wire material will tell you if you have the right alloy. Passivation testing per ASTM A380
may give you some insight about surface condition, but further analysis may be required to look for unusual surface contamination.
Good Luck.
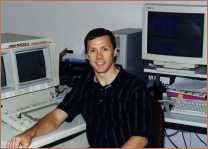
Larry Hanke
Minneapolis, Minnesota
2000
Jeff: The wire needs to be passivated. There are a number of companies who are using our CitriSurf products for the same application in industry, obtaining excellent results far surpassing what you can get with nitric acid. You will get excellent corrosion resistance with a safe and economical process. We can show you how to do this in house, and would be happy to have a representative call on you to show you how to do it. Lee Kremer
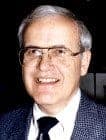

Lee Kremer
Stellar Solutions, Inc.

McHenry, Illinois
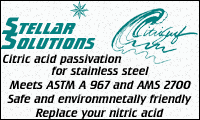
2000
Jeff:
For the ultimate in passivation, try electropolishing. The finish is superior to passivation by any other process.
For additional details, please visit our web site through the link below.
Metal Coating Process Corporation - Charlotte, North Carolina
2000
Dear Colleague,
My recommendation would be to use a passivating solution of either nitric acid, or perhaps phosphoric acid.
I know the use of this chemistry incurs some attention to environmental issues, however, there is really no substitute for the correct technology.
citric acid will chelate free iron, but will not directly passivate the stainless steel surface. It cannot be a better passivating agent than nitric acid.
citric acid is marketed as an environmentally friendly product, not a true passivator.
Best regards,
- Australia
2000
I agree with Mr. Hill. There is no substitution between the Nitric process and the Citric process. You will achieve much more superior results from the Nitric process. We have tried both and would not consider using the Citric based process.
Hunter Cutchin- Easley, South Carolina
2000
Everyone please ignore my ignorance on the subject of stainless steel corrosion. I am trying to find out some information on the corrosion or the lack thereof of stainless in an oxidizing environment specifically that contributed by liquid sodium hypochlorite.
If anyone has any printed matter on the subject, please respond. Thank you very much.
- St. Croix, VI, US VIRGION ISLANDS
2001
Q, A, or Comment on THIS thread -or- Start a NEW Thread