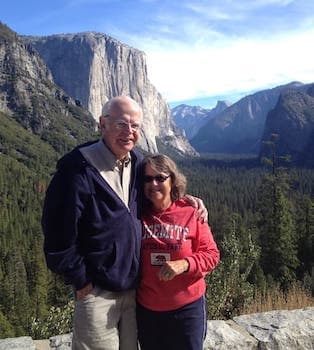
Curated with aloha by
Ted Mooney, P.E. RET
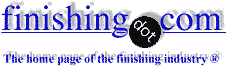
The authoritative public forum
for Metal Finishing 1989-2025
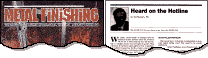
-----
Chrome plating corrosion in diesel fuel
October 2, 2012
Q. The application in question is a 2s diesel engine, which runs on heavy fuel oil, HFO (varying contents of sulfur, sodium and vanadium). The materials in question: liners cast iron and the piston rings are chrome ceramic rings (basically a chrome multilayer with some hard particles, Alumina included in the multilayer.
The problem:
chrome plating is turning green and wear rate is very high.
Facts:
1) The liners present corrosion signs, as burning of HFO creates sulfuric acid and water. The lube oil is quite high BN (BN70) to neutralize the acid from combustion. In some cases the surface of the liner is green (I assume it's iron hydroxide caused by the change in pH from acid to alkaline). It is generally accepted that the liners will corrode due to the presence of sulfuric acid, coming from combustion. To prevent that, the liners are kept "warm" so cold corrosion is avoided. Some other liners appear with black lacquer marks which come from the gypsum from the lube oil.
2) Piston rings present signs of corrosion with a few layers or in very bad cases lead to total coating detachment. Sorry I cannot attach pictures but there have been cases where a single area from the top layer is removed and the other layers are intact.
3) As a failure mechanism of the chrome layer we see a widening of the micro-crack network and wear rates extremely high.
4) In some other engines with the same coating they are running fine.
What strikes us is the chrome getting attacked in such a severe way. I know chrome can be attacked by chlorides and possibly by sulfur dioxide (anyone with a mechanism for this? - Read in a a paper from from ASM but no reference to the mechanism). To an extent also can be attacked by sulfuric acid, as long as there is no passivating environment.
Anyone with similar experiences on chrome platings? Facing such a severe attack on chrome, wear rates extremely high, and appearance green!
Any comments or help would be very appreciated.
Best Regards
- OPorto, Portugal
A. Hi,
The only way to avoid corrosion in hardchrome is to do Electroless nickel / hard crome. Or pulse plating.
In a salt spray chamber protection is 45 hour.
EN/Cr 600 hour
PP plating 600 hour
= Thats mean no corrosion.
Hard chrome is not a corrosion protection, because of the microcracks/ macrocracks. Depends on hardness or the chemistry in the chrome solution. Also the anodes are important to check. I don't understand why they don't use a deposit like double layer with EN or PP chrome plating?
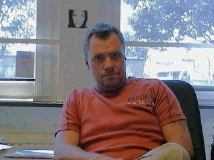
Anders Sundman
4th Generation Surface Engineering
Consultant - Arvika,
Sweden
Q, A, or Comment on THIS thread -or- Start a NEW Thread