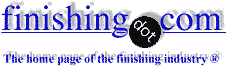
-----
Correlation between Nitinol thickness removal after electropolishing and corrosion resistance
Q. Hi! Can anyone help me to understand the correlation between the amount of material removed (during the electropolishing) from Nitinol and the corrosion resistance of Nitinol? Is there any literature out there that reports in this topic? There are a couple of articles that correlate oxide thickness and corrosion resistance of Nitinol, but I cannot find anything on the topic I posted yet. Any information will be greatly appreciated. Many Thanks!!
Boon
- Sylmar, California, USA
September 5, 2012
A. If more than 3 microns are removed during electropolishing - then no significant effects on corrosion resistance are seen in correlation with material removal rate. Also corrosion resistance increases by additional passivation treatment that increase thickness and uniformity of the oxide film.
When less than 3 microns are removed, the corrosion resistance depends on rate of material removed, since the outer thin layer has different Ni-Ti alloy composition, and it is important to remove this layer.
Moreover during the first few seconds of electropolishing, the process of the metal dissolving goes very unevenly, since the initial oxide layer has uneven thickness and composition along the metal surface. As a result on some areas the old oxide layer still can be seen, on another areas - the new formatted oxide film appears. By increasing duration of electropolishing the whole metal surface becomes uniform. It is clearly seen if you examine the electropolished surface after 1,3,10, 30 and 100 seconds.
The above observations are true for acid-free electropolishing method. The newly developed Ultrapolishing does not require additional passivation procedure, and the uniform metal surface is created in less than 20 seconds. We do not have such data for methanol-based nitinol electropolishing, since we do not use this method.
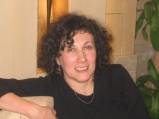
Anna Berkovich
Russamer Lab

Pittsburgh, Pennsylvania
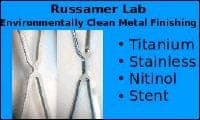
September 6, 2012
Q, A, or Comment on THIS thread -or- Start a NEW Thread