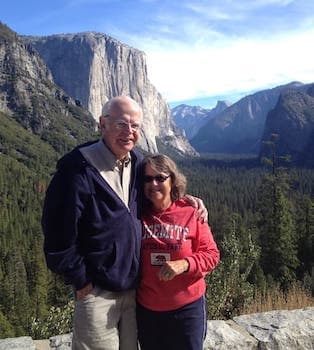
Curated with aloha by
Ted Mooney, P.E. RET
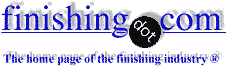
The authoritative public forum
for Metal Finishing 1989-2025
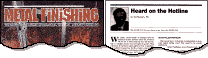
-----
Excess Sludging in Acid Etching of Aluminum
Q. Good day.
My acid etch bath is for etching aluminum. The composition is Phosphoric Acid, sulfuric Acid and Oxitol, operating temperature 35 to 55 °C. The solution is used to de-rust, descale and degrease in one step. There is sludge build up due to the aluminum deposits and my boss wants the the solution to be without sludge. I wanted to know if that is possible and if so what can I use to minimize the sludge?
Regards
Mulelu
Employee - Gauteng, South Africa
October 25, 2021
A. Hi Mulelu,
I know this response is late, and I apologize. It's sadly a fact of acid etches. Mine is phosphoric and ammonium bifluoride (old cClepo sat-n-mask formula) and oh my goodness, the SLUDGE. It's so bad our racks sometimes come out with mud on the tips.
Really, the best you can do is tank filtration, but of course the solution is so savage that it eats pumps. We just manage it by letting the sludge build up to a point where the line tech starts getting grumpy, and then change the tank.
Please pass along to your boss that it's normal, and that feedback from the line technicians will tell you when to give up and start over. If it is working correctly on parts, it's a good tank.
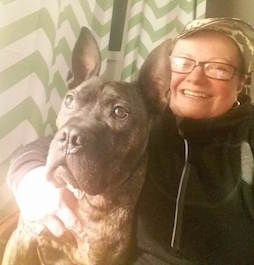
Rachel Mackintosh
lab rat - Greenfield, Vermont
December 24, 2021
⇩ Related postings, oldest first ⇩
Q. I am a chemical engineer who is new to finishing. We have a 1400 gallon aluminum etching tank containing a tri-acid formulation comprised of 10% nitric acid, 6.5 oz/gal chromic acid, and hydrofluoric acid to maintain an etch rate of 0.001" /surface/hour (added as ammonium bifluoride), maintained at ambient temperature. We recently removed a year's worth of sludge, which came out to 440 gallons, which, based on our throughput, seems excessive to come primarily from precipitated aluminum (our dissolved aluminum content is 1.5 oz/gal, after 2 years) - in addition to the fact that it's of a very similar color to chromium trioxide. Given that all of the expected solid components (chromium trioxide, ammonium bifluoride, and ammonium fluoride) are highly soluble in water, it seems more likely that we're dealing with solids that never enter solution instead of solids that precipitate out of solution (I'm looking into changing from our poorly-designed air agitation system to an eduction system to resolve this). The only issue is that I've noticed a visible thick layer of precipitate within our sample bottles even an hour after sampling, which leads me to wonder if there's some reason why precipitation would spontaneously occur from this solution.
A further argument for chemicals never entering solution rather than precipitating out of solution is smaller than expected responses by the tank to solid chemical addition. One of our primes has spec that provides a rule of thumb that an addition of ABF of 0.37 g/L should produce an increase in etch rate of 0.1 mil/surface/hr. The increase that we obtain, 0.2 mil/surface/hr, is generally obtained by adding 25 times more ABF (150 lbs) than would be calculated from this relationship. The conventional knowledge in the lab is that the concurrent addition of nitric and/or chromic acid blunts the increase, but given that the total nitric and/or chromic acid levels are increasing by only 20-40%, I would not expect to see such a hindrance. Another alternative could be dissolved metal, but again, the hindrance seems high. The response to chromic acid addition is also lower than expected.
Can anyone provide comments on our sludge formation and sluggish etch rate increase that could confirm or correct my working theories? Are there any other quantitative properties of the tank that I should investigate that would clarify the situation?
Thank you,
Process Engineer - Long Island, New York
May 29, 2012

Q, A, or Comment on THIS thread -or- Start a NEW Thread