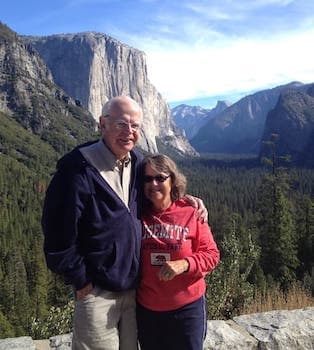
Curated with aloha by
Ted Mooney, P.E. RET
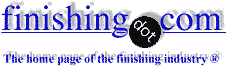
The authoritative public forum
for Metal Finishing 1989-2025
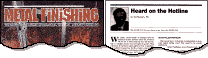
-----
Cooling zinc in emergency pot
August 12, 2012
Q. We have a hot dip continuous galvanizing line with a pot kettle of 80 tons capacity.
we have an emergency tank that can be filled with molten zinc in emergency cases quickly.
This emergency tank is manufactured from 50 mm wall thickness steel plates and has 2 dual burners to keep zinc at high temp. We have a planned evacuation of the main pot to the emergency tank.
We will not need to run the main pot for the next 6 months and we don't want to the zinc in the emergency in liquid state, so the team suggests to let the zinc cool down till solidification and when we need to run the line again we will heat up till the zinc becomes liquid again.
The problems that we are afraid of are:
1- The zinc may destroy the tank wall during cooling or heating process.
2- Is it possible to heat 80 ton block till it melts, because when we made this for 1st time we used 30 kg zinc plates and fill the pot with water, and heated up until the zinc melted, but it took about a week.
Please advise.
- 10th of RAMADAN, EGYPT
A. Sir:
For success in what you wish to do much depends on two items:
(1) What is the steel chemistry of your emergency pot?
(2) How are you trying to heat this pot?
The pot (kettle) must be almost pure iron. Much silicon, phosphorus, aluminum, or copper in the steel will react quickly with the zinc and destroy the kettle.
The heating of this kettle must be relative "even" all along the side walls (not from the bottom) having only about 10,000 Btu's/square foot passing through the walls/hour.
If you can describe more what you intend a more complete answer could be given. Expect the zinc to pull away from the freezing zinc about an inch or two.
Regards,
Galvanizing Consultant - Hot Springs, South Dakota, USA
A. Dear Mr. Milad,
Here are some of my contributions to add to Dr. Cook's comments.
This is a common practice that is carried out by some CGL plants.
You are freezing the zinc to save energy and manpower, am I right?
When zinc freezes, it will contract. Since the freezing zinc adheres to the pot wall, there will be stress on the zinc pot. To remove the stress, allow the zinc to freeze until approximately 300 °C. If there is no thermocouple feedback, visually it will be when the top center of the molten zinc starts to cave in. At this point, start the burners again to heat the side walls until the zinc that adheres to side wall melts. Since the main zinc block have already contracted, you will hear a loud noise as the pot wall separates from the frozen zinc. At this point the burners can be shut down.
As for remelting, it depends on your burner capacity. Just start heating after the normal ramp up of the furnace temperature.It will take approximately half the time of your initial melt out. Please take note that excessive furnace temperature will shorten the pot life span.
This method is suitable for zinc pot with perfect rectangular shape. I mean pots without awkward structure where the frozen zinc can still create stress even though it does adheres to the pot walls.
Good luck
Voo
- Karachi, Sind, Pakistan
A. Sir:
I trust that you used the correct welding rod for your emergency zinc kettle? If not then the zinc may attack the weld material or the kettle wall next to the weld.
Regards,
Galvanizing Consultant - Hot Springs, South Dakota, USA
Q. Sir,
I am sorry we don't know the steel chemistry of emergency pot, but we already moved zinc from main pot to emergency several times and move zinc back to the main pot without any problems.
Emergency dimension is 5 m X 1.5 m X 1.5 m.
We are heating by 2 Pyronics dual fuel burner #24-XDF-A-S
along the side wall 5 m length. Burner level is at mid-height of the walls.
- 10th of RAMADAN, EGYPT
Second of two simultaneous responses -- August 16, 2012
Q, A, or Comment on THIS thread -or- Start a NEW Thread