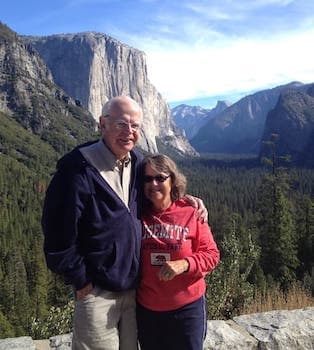
Curated with aloha by
Ted Mooney, P.E. RET
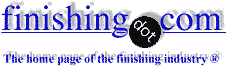
The authoritative public forum
for Metal Finishing 1989-2025
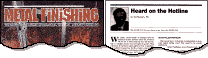
-----
Brown contaminant on stainless steel after plating
Q. We manufacture connectors with nickel contacts sealed into stainless steel shells. We send the parts to a plating shop to have the contacts (isolated from the shell with our sealant) nickel and gold plated. When the parts are returned, we are seeing brown contaminant that looks like rust on the stainless steel parts. It appears to get worse over time as if the a chemical reaction is continuing. It should be noted that after we seal the contacts to the shell, we sandblast with 80grit Al2O3 followed by #10 glass bead to clean the stainless shell and contacts.
I'm trying to find out if this is a problem with our abrasion process or if it is a rinsing issue after plating. The plater uses city water in a common drag out tank, which does not sound like good practice. Also, is it likely that if the parts were slightly wet when shipped back could this cause the problem?
Any help is appreciated.
Engineering Manager - Melbourne, Florida, USA
August 4, 2012
A. It is difficult to understand exactly what you mean. If we have to plate onto "old" nickel, in the presence of electrically isolated stainless steel, then the required "activation" (reduction) step to prepare the raw nickel surface will remove the passivation from the stainless steel (also activate the stainless) so that then the stainless rust.
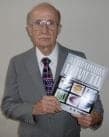
Robert H Probert
Robert H Probert Technical Services

Garner, North Carolina
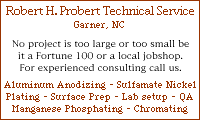
August 6, 2012
A. This is just an idea to investigate about it.
Could it be due to stainless steel contamination with iron, or chromium removed from surface?
- Bucaramanga Santander Colombia
First of two simultaneous responses -- August 7, 2012
Q. Robert, thanks for the response. here is our process sequence:
1. ELNI beryllium-copper contacts
2. oxide the contacts and oxide the stainless steel body
3. seal the contacts into the body using our sealant material
4. mask the seals with a dissolvable maskant
5. abrade the pins and stainless body to remove the oxide followed by glass bead
6. toluene wash to clean sand/glass and remove the maskant
7. re-mask and wire the contacts for plating
8. send out to plating shop for electrolytic nickel followed by gold on the contacts only
9. toluene wash to remove maskant.
at this point we commonly see brown "rust" on the stainless body. It is always worse in threaded holes.
- Melbourne, Florida, USA
A. What I am trying to say is that the activation step that the plater has to use to get adhesion of the electroplating on the pins IS ALSO ACTIVATING (THE REVERSE OF PASSIVATION) THE STAINLESS STEEL BODY - SO THAT IT RUSTS. Let's try a citric acid ⇦ this on eBay or Amazon [affil links] type of passivation on the stainless steel AFTER the electroplating has been done. Best passivation is done with nitric acid but that would strip your gold and nickel, but citric acid type passivation would be safe on top of the gold. Off line I can put you in touch with vendors of proprietary citric acid passivation solutions, but try it with a sample solution in a beaker [beakers on eBay or Amazon [affil links] first.
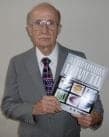
Robert H Probert
Robert H Probert Technical Services

Garner, North Carolina
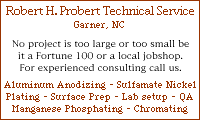
August 8, 2012
A. WHAT SS DO YOU USE, FREE MACHINING SS OR SS 316/304?
WHY DOES THE PROCESS LOOK COMPLICATED?
CAN YOU NOT GOLD PLATE THE CONTACTS AND PASSIVATE THE SS, AND THEN ASSEMBLE THE SUB ASSEMBLIES?
WHY DO YOU SAND BLAST THE BeCu CONTACTS AND HOW DO YOU CONTROL THE DIMENSION BEFORE PLATING?
ELABORATE YOUR PROCESS IN LINE WITH THESE QUESTIONS -- I WILL GIVE CERTAIN DOE FOR OVERCOMING THE SITUATION.
I DON'T WANT TO ASSUME THINGS WITHOUT ADEQUATE REASONS
- CHENNAI, TAMILNADU, INDIA
August 19, 2012
Q, A, or Comment on THIS thread -or- Start a NEW Thread