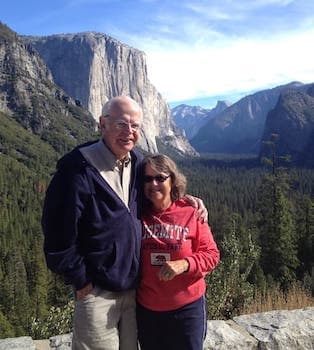
Curated with aloha by
Ted Mooney, P.E. RET
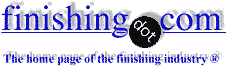
The authoritative public forum
for Metal Finishing 1989-2025
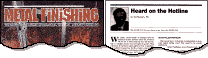
-----
Master electrician questioning corrosion and possible current leak in fountain
July 25, 2012
Q. Very odd (and probably dumb) question regarding the increase of corrosion to dissimilar conductors while submerged in, or in the presence of large amounts of directly contacting water, and any coating that may be applied to mitigate the corrosion and prevent current leaks/loss.
I am a Master Electrician in Wisconsin; recently because of the terrible construction economy, I have been taking on commissions from clients to build custom lighting fixtures, including exterior fixtures.
Being a Master with almost 20 years of experience and having completed a great number of projects in the design/build field, I initially felt no qualms about trying my hand at any fixture, including one's intended for exposure to wet locations and submerged locations; I've done a great deal of "ground vault" work in the past.
The responses I received from my clients were universally positive; I began to experiment a little with custom-built lighted fountains - I built the fountains and lighting fixtures from old glass china, excluding uranium glass.
In order to maximize light output, efficiency, to minimize the cost and speed up construction, I designed LED arrays powered by computer power supplies enclosed in a NEMA-3R housing; I used the 12V leads to power arrays of 3-4 V 20 MW while 10 mm LED's; I used the standard practice of resistor sizing and installation; I potted the arrays with a combination of epoxy, covered with copious quantities of silicone.
Now remember this is "proof of concept" and not in a customers possession.
I energized the fountain pump, then the LED arrays; I discovered a bit of detectable current passing through the water; "Equipotential bonding" came to mind, so I grounded the plaster of the fountain base to the concrete beneath the non-conductive pool it was sitting in, to a rod I placed in the earth, and then back to my panelboard.
I still had detectable current (as in I could feel a 'tickle' around my cuticles and the cuts on my fingers when my hands were submerged and the rest of my body was making an earth contact) and my GFI receptacles weren't tripping (two in series).
I then thought I had defective GFI's; I replaced them. No trip, no change on being able to feel the current.
I no longer have an oscilloscope, it was stolen; I can't really think of any way to find out where that current is leaking from/to or why my GFI's won't trip.
Perhaps something to do with the computer power supply? I imagine its capacitance may "disguise" a mild current leak from the GFI; the comparator may not be able to "see" what's happening past the caps?
Anyway, I recently discovered a series of 'pinholes' in my LED array potting; many of the conductors were heavily corroded; upon disassembly many of the electrodes on both the anode and cathode were so corroded that they crumbled when no longer supported; after less than 60 days of intermittent operation of both fountain and fixtures, I would not expect to see so much damage; the LED's are, of course, irreparably damaged and so I'll replace them, but I wanted to know if the speed of the oxidation and corrosion were increased when DC current is present at voltages greater than whatever exist naturally between dissimilar metals; I'm thinking that because the conductors I used are copper and the electrodes on the LED are of a different and ferrous material, there's some serious galvanic corrosion taking place and I need to mitigate that as much as possible while also preventing any water from reaching the conductors.
I'm also slightly concerned about the conductors being corroded by the silicone; I think this may also be a bit of a problem.
I would greatly appreciate any input and especially suggestions of the right questions to ask so that I can figure these things out in the future by myself, and of course any kind of coatings that may be applied to solve the problem.
Thank you very much!
- Greendale, Wisconsin, USA