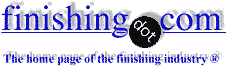
-----
AAMA 2605 Anodic Coating
Q. Hi Everyone,
I need to provide a spec for the anodic coating of aluminium we use in our products. I've come across the AAMA 2605 classification which is exactly what our aluminium needs to be, however I cannot find specifics on how to achieve this finish (other than proprietary coatings). Is there a publication that details the different options regarding anodizing [concentration/time/temp plus sealing process] that produce specific thickness known to pass AAMA 2605?
I suspect that any coating verified to this standard would be proprietary information but I'd like to have someone tell me that rather than jump to potentially erroneous conclusions.
Thanks!
Product Designer - Newark, Delaware, USA
July 16, 2012
A. Hi Ben,
I have just had a look at AAMA 2605 and this is a specification for organic coatings, not anodic coatings. The only mention of a surface treatment is conversion coating, again this is not anodising.
I am based in the Aerospace industry, so am not really up on commercial specifications, but if you want to go down the anodising route then have a look at MIL-A-8625, this describes 3 types or anodising, normally called Type I, Type II and Type III anodising. If you find what you are looking for there you then need to decide on a top coat, otherwise you will not meet the requirements of AAMA 2605.
Aerospace - Yeovil, Somerset, UK
July 19, 2012
August 30, 2012
Q. Hi Brian,
Thanks for the response! Sorry for my delayed reply, I've been continuing my research though and I'm trying to reach a conclusion on this issue: it appears that there's no formal performance-based standard written for inorganic (electrolytic) coatings -- how then does the industry ensure that their processes create a product that performs to customers' standards?
Here's the crux of the situation:
We are ordering aluminum anodized for an outside application (not exactly architectural but that would be quite similar). As a customer, we don't particularly care how it's accomplished, but we'd like the coating to be black for at least 10 years (the warranty on our products). Additionally, since we have multiple vendors, we need to make sure the "blac" coming from each one matches.
I would prefer not specifying an entire process because (a) I'm not an expert so I don't know what the best process is exactly, and (b) I don't actually care about the process, all I care about is the end result.
What is a typical way customers spec. out this kind of thing to anodizers?
Do we need to simply indicate that the product should have a lightfastness of 10 on the international blue scale (per ISO 2135) for a period of 10 or more years? If so, how can we be certain that the process they pick is sufficient?
Thanks for your help!
- Newark, Delaware, USA
Q, A, or Comment on THIS thread -or- Start a NEW Thread