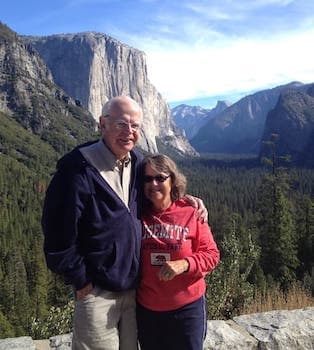
Curated with aloha by
Ted Mooney, P.E. RET
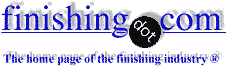
The authoritative public forum
for Metal Finishing 1989-2025
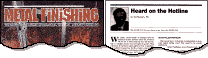
-----
Welded stainless - rusting issue after powder coat
Q. Part is 304 SS welded with 308L wire. There are parts that are Tee welded with stitches. Powder does not migrate into the joint, and it is not visible. It is in an environment where it is splashed with chlorine water regularly. The problem is that an unsightly rust gets washed out of the joint, and stains the white powder coat. If left in the chlorine water, the white powder coat around the weld turns black. Adhesion does not appear to be a problem in this case. What can you suggest as a cost effective method of avoiding the rusting?
Ben WolfProject Engineer - Rock Falls, Illinois, USA
July 16, 2012
A. Hi Ben,
Stainless steel is very resistant to corrosion because it contains more than the 12% of chrome.
The area near a weld on stainless steels is usually not "stainless" because the chrome in the heat affected zone will form precipitates with Carbon. If you want the welded zone to be stainless too you can use low-carbon stainless steels (less precipitates) or steels containing stabilizers such as Titanium or Niobium that will precipitate with carbon more easily than chrome. Powder coating on stainless steels is still a crime to me, but lately it happens very often.
- Berlin, Germany
July 19, 2012
A. This is a design issue.
The designer is incompetent.
Your product has designed in faraday cage effects and metallurgical defects.
Change your designer.
Hope this helps,
Regards,
Bill
Trainer - Salamander Bay, Australia
July 24, 2012
A. Hi, William.
You make a good point, but I don't think I'd put it that strongly :-)
For one thing, every design is a compromise and we don't have a full list of the objectives, to know how well the design is functioning from other standpoints. Secondly, we don't know that the designer has control over the welding procedures, or that there was an intention to powder coat this item. It does sounds like a higher grade of stainless steel should have been used for chlorine water.
Hi, Ben.
You might consider applying a thermoplastic powder, like nylon, from a fluidized bed, as that is often done on wire goods. Alternately, e-coating for full coverage sounds like a possibility that will minimize rust stains, although probably not eliminate them long term.
Regards,
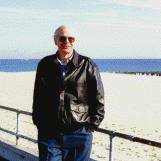
Ted Mooney, P.E.
Striving to live Aloha
finishing.com - Pine Beach, New Jersey
Q. This was an existing design by our customers, and of course since cost is an important marketing tool for them, the stainless grade was determined by them as well. They are not able to produce larger quantities, and that is where we come in.
We don't have a "Designer" and they don't either. Frankly this is a problem we have not run into in the past, and the Faraday issue is new to me.
Ben Wolf [returning]- Morrison, Illinois, USA
July 25, 2012
A. The chlorine water (swimming pool?) is a bad environment for stainless steel. 304 is okay, but 316 would be better in this situation. Most importantly, are you saying there is an area that is not getting covered by powder coat?
This is the problem with any coating. If it is not perfect or gets broken by wear and tear you have a worse problem. What happens is that you get an anodic effect. All corrosion is electrical, as you know. When the electrical attack takes place over a wide area it is miniscule to any one area, so the corrosion does not happen easily. But, when you have a small area that is open all of the electric current goes to that small point and corrosion is MUCH faster there.
Adding a passivation treatment prior to the powder coating may help for a short time, but I think the main downfall here is the gap in the powder coat.
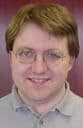
Ray Kremer
Stellar Solutions, Inc.

McHenry, Illinois
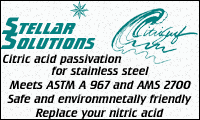
August 13, 2012
Q, A, or Comment on THIS thread -or- Start a NEW Thread