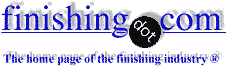
-----
No current in my nickel electroplating bath
Q. We use a nickel sulphate, nickel chloride and boric acid solution to plate steel components. We usually run at around 700-1000 Amps (19 V) but can now only get a maximum of 200 Amps. The pH of our bath has been dropping or at least not increasing; we usually run at around 3.8-4 but have recently been getting as low as 1.5. We have added nickel carbonate to increase the pH but have not had much success - reaching only about 3.
We have tested the ions in the bath and the nickel sulphate and boric acid are a little low but within spec. The nickel sulphate is a little low at 24 g/L. After a lot of searching we thought that the problem was with our current. We have checked all the external elements and the current supply is correct. The only other thing left is anode passivation. We have soaked the anodes in 5% hydrochloric acid for 24 hours to try to activate the anodes but we are still getting no current.
What else could be wrong?
- Krugersdorp, Gauteng, South Africa
May 30, 2012
A. There is a very very high probability that you failed in solving the "polarization" problem
I would recommend putting one layer in a wash tub or tank and pressure washing them with a pressure washer
[affil links] using a tiny bit of whatever anti pit you use in the tank. Then rinse well and soak for an hour or so in a 20% by volume of HCl. Repeat as required. The chips form a slime layer as they polarize.
- Navarre, Florida
May 31, 2012
A. Hi. You have no current because your nickel solution is not enough conductive. 24 g/L of nickel sulphate is very very low, your problem comes from this wrong value.
Best parameters for nickel Watts are :
- 280 g/L nickel sulphate
- 60 g/L nickel chloride
- 40 g/L boric acid
- pH = 3,8
- T = 60 °
I hope this can help you. Best regards ;)
- France
A. I would agree with Francois - your bath composition looks wrong to me as well. However, James also has a good point - your anodes may be passiavating and need reactivating. I assume you are using soluble nickel anodes, although you do not say so. If you do wash them in hydrochloric acid, ensure they are thoroughly washed to prevent an increase in chloride concentration, as this will induce stress in the nickel deposits. I would also suggest washing them in acidic waster -use sulfuric acid to acidify the water and minimise any further passivation. Your comments about seeing a decrease in pH suggests the anodes are passivating and discharging either chlorine or oxygen in preference to dissolving the nickel. I would also suggest that you recheck and clean all your electrical connections for corrosion and/or a dead connection. Spend some time cleaning and repairing your electrical joints and contacts.
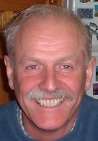
Trevor Crichton
R&D practical scientist
Chesham, Bucks, UK
June 6, 2012
A. Hi,
regarding your question, I have some suggestions regarding your problem.
First, you need to do carbon treatment on the bath to remove any organics breakdown and impurities that affect your plating current to flow. This is important because you are plating steel. Other option is use activated carbon filter cartridge but you have to change it every 4-6 hours depending on your bath size (volume).
Second thing is you have to adjust your bath composition. The best concentration is:
NISO4 between 290-300 g/liter
NiCl2 between 62-65 g/liter
Boric Acid between 43-45 g/liter.
Plating line - Malaysia
Q, A, or Comment on THIS thread -or- Start a NEW Thread