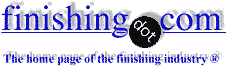
-----
Martensitic Stainless Passivation
Thank you for the summaries.
Q. I have a different issue with BG42, 3.5" diameter: I can't get any. Carpenter Steel is way out in lead-time. Is there another stainless alloy that is comparable in performance characteristics to BG42?
Anyone's comments would be greatly appreciated.
- Tualatin, Oregon
May 7, 2024
A. Hi Chris, you haven't mentioned which properties of BG42 are important to you. From what I can tell BG42 is a high speed steel, but you are referring to it as a stainless grade (it is both) so presumably you aren't looking for it's high temp hardness.
A quick look says 154CM is a fair analogue although without the vanadium so your hardness and wear properties will suffer. Material selection is always a compromise and without knowing what properties you want it is hard to provide you with an equivalent, as the only alloy which matches the properties is that alloy itself.
- Ballarat, Australia
May 22, 2024
⇩ Related postings, oldest first ⇩
Q. First off, let me apologize as I know the citric vs. nitric acid debate has been discussed ad nauseum on this forum. I'm hoping my question is different/specific enough to spark some new thoughts.
We passivate all our stainless steel parts here. That encompasses exactly two grades of stainless, 440C and BG42. BG42 is a high temperature variant with about 14.5% Cr, 4% Mo, and 1.2% V; it is covered under AMS 5749.
Our facility uses citric acid exclusively rather than nitric. I believe we use a proprietary formula rather than a straight citric acid (as I understand, citric alone will not work so well). We have recently discovered a problem with our BG42 parts where passivation, particularly extended times, leads to intergranular attack on the surface of our parts. Anywhere from approximately 15 minutes leading to 0.0001" deep to 8 hours of passivation time resulting in 0.0015" deep. However, we have no such problems with our 440C parts. citric acid passivates them just fine without any sort of attack.
We've done some testing regarding cleaning and passivation time and quite a few other variables and it seems that passivation time is the largest factor causing this attack. We have also found that nitric acid passivation (AMS2700 Type II, 50% nitric with sodium dichromate) does not cause this attack on our BG42 parts.
Based on my research so far, I understand that nitric does oxidize the parts in the bath while citric only cleans and must oxidize the parts in air after removal. Does anyone have an idea of how long this process takes with high alloy stainless steels? I don't believe it is nearly instant like aluminum but do not have any evidence either way.
I'm a metallurgist whose experience is in heat treating of the steels but I'm trying to do my best to help solve our current issues with IGA and was hoping someone could lend me some insight. I've been reading quite a bit about citric and nitric acid passivation but I assume most of it applies to more everyday stainlesses, like 304 and 316 and 17-4PH. Is it possible that we're overlooking a major difference between citric and nitric acid or that the special alloying of BG42 is for some reason incompatible with citric?
Thank you for any help you can provide!
- Peterborough, New Hampshire, United States
April 26, 2012
A. Aiden,
I believe I am already working with your compatriots on this issue, but I would like to hear if anybody else has any comments. Intergranular attack is almost completely unknown with citric passivation, though this BG42 grade isn't something I've run across before either. If anybody else has experience with it I would be happy to listen.
Regarding oxidation in the bath, which is of course one of the main areas of the old nitric vs citric debate. Of course ALL acids have the ability to oxidize, that is the mechanism through which the H+ ions remove atoms of metal from the surface of the parts. Nitric acid is doubly oxidizing though, especially in high concentrations, because the N in the NO3- ion is at a high oxidation state and is eager to act as an oxidizing agent all its own.
However with stainless passivation we need two kinds of oxidation. First, the removal of iron in the bath (in nitric baths all other metals get removed as well, to a lesser extent), and second, the formation of chromium oxide through the joining of oxygen to the metallic chromium on the surface WITHOUT dissolving it into the bath. I remain unconvinced that the second type can occur within a nitric acid bath regardless of its greater ability for performing the first type.
Sodium dichromate is also used, both as an additive to the nitric acid or as a post treatment, due to it being a strong oxidizing agent. However again there is the same question, regardless of how much oxidizing power you have in a bath, are you actually forming a metallic oxide surface or are you just dissolving metal into solution? I suspect that peroxide is the only bath additive that has a decent potential for surface oxide formation while in solution. Beyond that, it's probably not going to happen until the surface is exposed to gaseous oxygen in the air.
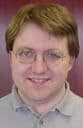
Ray Kremer
Stellar Solutions, Inc.

McHenry, Illinois
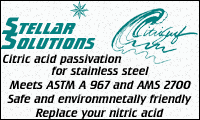
May 4, 2012
Q. You are correct, sir, I believe we have some people working with you directly to help us figure out what is causing this problem that we have. As I have learned a lot about passivation from the Finishing.Com letters, I was hoping that I could get some more information by posting one of my own. Hopefully, someone will have more to add as this is a somewhat difficult situation for us now. We are looking at all options but may very well be forced to bring nitric acid passivation back in house to solve our problems.
For reference in case it helps anyone, the steel we are seeing problems with is BG-42, this is a trade name of the material produced by Latrobe. As far as I understand, it is chemically equivalent to Carpenter's CTS-B75 and both match UNS S427000. I don't know if anyone has heard of any of the other names but I thought I should add them for clarity.
- Peterborough, New Hampshire, United States
May 8, 2012
Q, A, or Comment on THIS thread -or- Start a NEW Thread