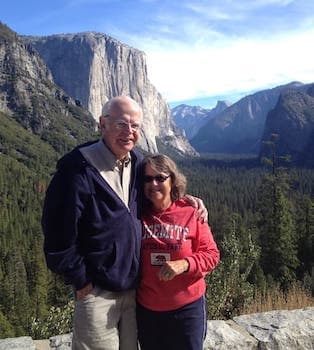
Curated with aloha by
Ted Mooney, P.E. RET
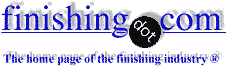
The authoritative public forum
for Metal Finishing 1989-2025
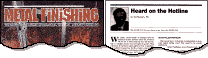
-----
HDG for Threaded Rods for 12 ft
March 1, 2012
Q. Hi readers,
We have been doing the HDG at bath temperatures at about 450 degrees , and using furnace oil for firing the bath , our kettle is about 14 ft long x 2 ft wide x 8 ft deep .
We are hand vibrating the rods after dipping them in the molten zinc , before water cooling it , now this process bend the rods to a certain degree in the 5/8" thickness . The higher thickness from 3/4" and above have clean threads .
However the problem comes while galvanizing the 3/8" or 1/2" rods as the threads are completely filled with the zinc in them even after vibrating with hands the rods are partially bend at about 20 degrees up to 30 degrees . Which make the rods completely useless.
We also tried blowing air at the threads , after the bath but it's not a practical solution as threads are not cleaned even though the uniformity of the rods are better.
We can't centrifuge such long rods , now considering that we need to galvanize about 8 mt of these rods on daily basis . Please inform us a practical solution to be able to have clean galvanized coating on the smaller sizes with uniformity .
Thanks
Atul
- Ludhiana, Punjab, India
A. Considering your quantity of threaded rod to galvanize, it is worth doing something special.
Have you considered an air knife? Using an annulus ring type, you could pass the rods through the ring and blow off the surplus zinc. You said you'd tried air, but not how you tried that.
You'd have to have the rods going through singly, and lengthwise, and straight from the zinc. This would blow off the extra that's clogging the threads. It would fire blobs of zinc about, so you'd have to arrange this safely, inside a canopy of some type.
Pipe and hollow sections are often done using a similar technique.
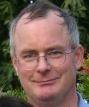
Geoff Crowley
Crithwood Ltd.
Westfield, Scotland, UK
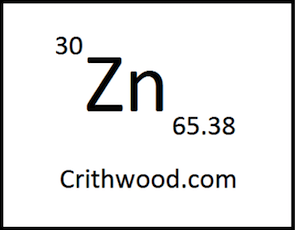
A. Sir:
Put two or three "U" shaped saddles into the kettle cross-wise and slightly sloped downward toward the product flow. The downward side of the saddles are straight and nearly horizontal. The threaded rods are put into the kettle one or a few at a time. The rods are taken out one at a time via hooked rods and laid on an inclined plane (about 30 deg.) and allowed to roll down the inclined plane. The rotation of the rod removes the excess zinc. The top of this inclined plane is near the top of the kettle furnace and the bottom is in the quench tank. The length of the inclined plane is about 6 to 8 feet. The bottom of the inclined plane is in a water trough to quench the zinc. This water will get hot rapidly and requires changing or circulating. The inclined planes (two or three angles or channels) need an oak (wood) top so as to provide traction for the rods.
Quadraflux at about 13 deg. baumé and 71 deg. C will provide easy entry into the zinc to prevent excess zinc spatter. Some additives (but not too much otherwise white rust will occur) will increase the zinc fluidity of the zinc and give better thread-ability. This method is called rolling rods. There are other methods.
Regards,
Galvanizing Consultant - Hot Springs, South Dakota, USA
A. Geoff:
With an air ring, magnetic rollers are also needed. The air ring is about the size of a doughnut with holes on the inside (in the doughnut hole). These holes are approximately 1/16 inch diameter and "face" backward in the hole toward the incoming rods at about 20 degrees from perpendicular to the rod length. The doughnut hole is about 1/4 inch larger than the rod being blown off. The rod should drop off the magnetic rolls (the upper ones) just after being blown, into the quench to solidify the zinc. One worker is needed (the fisher) to draw up each rod (one at a time) to the first magnetic roll to get it started into the blow ring. Hot air works better than cold air. Shields keep the zinc blowings away from the workers. Most zinc is blown right back into the zinc kettle. The blow ring and shields can be nitrided to keep the zinc from sticking. The rods can be introduced into the molten zinc using a "star wheel."
Regards,
Galvanizing Consultant - Hot Springs, South Dakota, USA
Q. Dr. Thomas,
We tried the rod rolling process as described by you the results are encouraging, but the production rate is too slow, we are unable to achieve 8 MT per day.
You mentioned other process, for thread cleaning of the rods; could you explain briefly on the different processes?.
So we can try the same.
Thanks
- Ludhiana, PB India
May 22, 2012
A. Sir:
I suspect that automation with some "star wheels" and "walking beams" to get threaded rods into the zinc and to withdraw from the zinc and then down a rolling ramp would likely work. The narrow kettle would not allow very large diameter star wheels. Thus the "cogs" of the wheels would have to be quite close together (okay for small diameter threaded rods; where you have the most trouble. The star wheels would have cogs that point upward on the side going in and point downward at the output side (like rotary saw blade). Around each star wheel you will need to have side traps to prevent the threaded rods from falling out of the star wheel cogs. Actually I have never seen this equipment exactly, but it would be a combination of threaded rod equipment and automatic pipes equipment. Thus what is basically done by hand now (with too low of production would be done via equipment faster). Definitely quadraflux would be best due to little zinc spatter and much shorter "cook off" time. Automatic skimming would also be needed but NOT a mechanical skimmer.
Regards,
Galvanizing Consultant - Hot Springs, South Dakota, USA
Q. Dr. Thomas ,
I would like to have your suggestion on American spin a batch, to do galvanizing of threaded rods .
Is it successful? As all previous attempts though have been more successful than our earlier practices thanks to your kind knowledge that you have shared with us. And in turn our rejection rates have decreased drastically , but we still have to check each and every piece manually, which is very time and labour consuming .
I shall wait for your kind comments .
Thanks
Atul
- Ludhiana, India
September 28, 2012
Q, A, or Comment on THIS thread -or- Start a NEW Thread