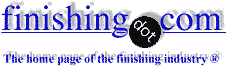
-----
Burnishing & corrosion-proofing zinc diecastings in one step
February 27, 2012
Q. I am wondering if there is such a sealer that can be used DURING the vibratory burnishing step. Currently, we are a captive die caster and for functional (non-decorative) die castings, we vibratory burnish and then we apply a rather traditional yellow chromate for some moderate corrosion protection. The chromate is primarily there to prevent white rust before our final customer installs the product (after which the corrosion protection isn't necessary.
We would like to delete the chromate step, especially the old barrel line we use to apply it. So if we determine that we cannot delete the sealer entirely, is there a way to apply corrosion protection in the barrel burnishing?
- Indianapolis, Indiana, USA
A. Yes, but how much protection is enough is the question. There are all kinds of additives that can be applied both wet and dry. Everything from a few hours of protection to days. Then there are other factors such as humidity and environment.
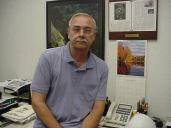
AF Kenton
retired business owner - Hatboro, Pennsylvania
February 28, 2012
Q. I am trying to come up with a formulation for copper burnishing. So far I have 12% citric 5% glycolic acid 5% soap 5% corrosion inhibitor. Running this at a 1 to 120 for 5 min the copper is still not as bright as it should be. I was thinking of adding some phosphoric acid. Any ideas would be helpful. Thanks Chip
Chip Sayre- Staunton, Virginia, USA
April 24, 2012
A. You mentioned that your parts were not bright enough earlier after vibratory process. There are a couple of factors that effect that. Also the resulting surface finish will be somewhat of a factor for the sealing treatment. What media are you using?
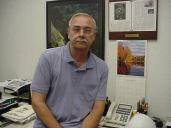
AF Kenton
retired business owner - Hatboro, Pennsylvania
April 26, 2012

Q, A, or Comment on THIS thread -or- Start a NEW Thread