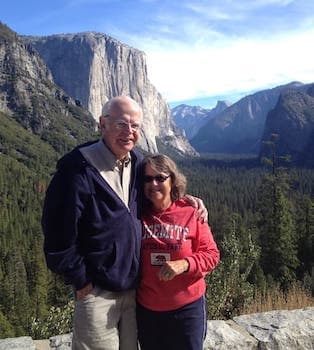
Curated with aloha by
Ted Mooney, P.E. RET
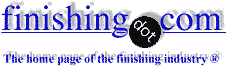
The authoritative public forum
for Metal Finishing 1989-2025
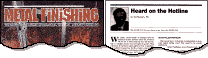
-----
Questions about plating onto aluminium
Q. We are a company dedicated to decorating components. At this moment we are plating gold, silver and chromium on brass, iron and zamak.
We are interested in expanding our business to plating aluminium, but we have some doubts.
First of all we are worried about the impact on wastewater treatment plant and we are not sure whether it will produce some troubles in precipitation due of chelation.
Apart from that, relative to zincate process, we are considering both processes cyanide and cyanide-free so we will be very grateful if you send us some information about these processes
Yours faithfully.
plating shop Manager - Valencia, Spain
February 16, 2012
A. The zincate step is the tough one as it does not have a good simple visual check. Double zincating is far better than single zincating. An alkaline electroless nickel strike immediately before follow on plating will be a major help.
A good vendor can provide you with hands on instruction as well as information on the effect of the additional chemical on your waste water plant.
- Navarre, Florida
I would prefer a non-cyanide zincate over a cyanide one, simply for reasons of easier effluent treatment. In about seven years of plating aluminium, I didn't notice a difference in adhesion between the two (I don't do this job any more).
All components were baked at 160 °C for 1 hour after plating so adhesion was tested fairly well.
One important thing I found with zincates is to ensure you test regularly for dissolved aluminium. It seems to be the only way we could tell when the zincate solution needed to be discarded. I don't remember the exact concentration of Al at which we began to have problems; perhaps someone with current experience could help you.
The alkaline electroless nickel preplate can have benefits however many contain ammonia which may cause issues with your waste stream. Plating directly with acid electroless nickel is possible however it will shorten the bath life. You will need to carefully monitor the dissolved zinc concentration in the EN bath as when it gets above a certain level, blistering will almost certainly occur.
Your cleaning process is also very important, as unlike brass & steel, aluminium usually cannot be electrocleaned. For this reason your soak cleaner needs to be in top condition all the time.
The final thing to consider is the etch - different etches are suitable for different alloys of aluminium, depending on which alloying components are used, e.g. 2011 will need a nitric-based etch to remove the copper smut and others need fluoride to remove high levels of silica.
- Brisbane, Queensland, Australia
February 28, 2012
Q, A, or Comment on THIS thread -or- Start a NEW Thread