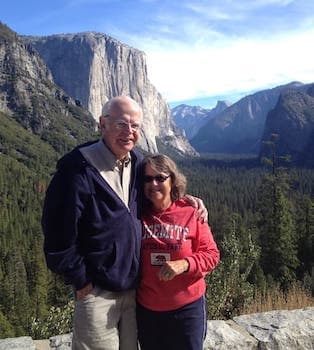
Curated with aloha by
Ted Mooney, P.E. RET
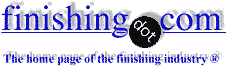
The authoritative public forum
for Metal Finishing 1989-2025
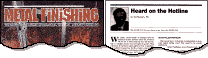
-----
Electropolishing parameters for maximum burr removal with minimal stock removal
Q. Hi,
Can anyone point me toward literature which experiments with the various EP parameters to find optimum setting whereby burrs are removed while minimising stock removal?
r&d - Ireland
January 16, 2012
A. Interesting question, Alan.
I don't know of such a paper offhand, but the topic is food for thought. There is a "polishing range" vs. an "etching range" for electropolishing, and that may suggest the minimum current density to start with.
Electropolishing should follow the current in accord with Faraday's Law, and the current can be controlled through the resistance by Ohm's Law. So it occurs to me (without any actual experience) that a closely spaced mesh anode might be a good way to steer the current towards the asperities rather than the general surface.
Regards,
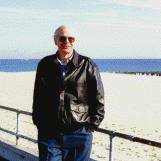
Ted Mooney, P.E.
Striving to live Aloha
finishing.com - Pine Beach, New Jersey
January 17, 2012
Q. Thanks Ted,
In this case the OD (stock) is very close to the feature to be deburred so localised or specialised cathodes like ECD may not help.
The part is a hollow tube where one end has teeth ground, hence the burrs. So really the goal is to remove the burrs without removing too much stock from the OD and without rounding the teeth too much.Obviously there is a tradeoff but I am hoping to find optimal settings (current density, electrode spacing, agitation, %Fe) along with good burr seeking electrolyte which may help.
On an aside I hope to produce a paper if this type of optimisation has not been investigated before. Most of the work I have looked at is on polishing stents
- Ireland
January 25, 2012
A. Alan, we use very low specific current to cut burrs first, and then a few minutes of general polishing to smooth the surface. In every electrolyte you can experimentally find specific current values when metal burrs start dissolving, but no polishing takes place, and at the same time no etching either. In many regular electrolytes that short area of parameters can be hard to find or hold.
We have developed an electrolyte where we feel the burr removal regime takes place on a large interval of specific current. Please contact us to discuss our proprietary electrolyte if interested.
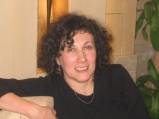
Anna Berkovich
Russamer Lab

Pittsburgh, Pennsylvania
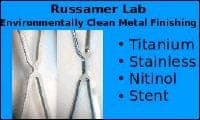
January 24, 2012
A. Hi Alan,
You should most certainly operate in the electropolishing range rather the etching region: apart from appearance, burr removal will be much more efficient. Cathode size and positioning should be optimized for good current density distribution. Beyond this little can be achieved unless you are prepared to use very closely conforming cathodes to bring the source of the current very close to the burrs. How close? Well, it depends on the burr. In general we are talking about 1-3mm. Perhaps, at this level, the process should be called electrochemical machining
I once worked on a project for removing burrs from punched holes in a jet engine actuator ring. We built a cathode assembly and installed a pilot plant. It ran extremely well when I was there supervising. But when I left the engineer's fear and loathing of chemical processes kicked-in and the project was abandoned and they continued to use what they understood - abrading with emery paper!
Harry
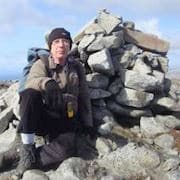
Harry Parkes
- Birmingham, UK
January 21, 2012
-- editor accidentally delayed the posting of this entry
A. You'll have to do a bit of experimentation; maybe there's no problem at all. Without knowing how much burr you need to remove, and how much loss is acceptable on other surfaces, it's hard to say. You'll certainly remove material faster from the stressed burr than on plain surfaces. Maybe as much as an order of magnitude.
If all else fails, can you use partial immersion or masking?
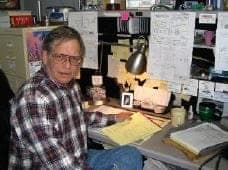
Jeffrey Holmes, CEF
Spartanburg, South Carolina
January 31, 2012
Q. Thanks for the above comments. Certainly a lot of experimentation required. With the large variation in ground geometries I will be going with a universal cathode. One round cathode (with round jig) outside the parts with the ground geometry facing out toward the cathode.
Do people think that low %Fe in the electrolyte will give better burr removal and less stock removal. My theory being that the higher the electrolyte resistance the better masking of even surfaces and the higher current density at high peaks (burrs and teeth). I believe there are some high resistance electrolytes based on glycogen with acid?
- Ireland
February 3, 2012
Q, A, or Comment on THIS thread -or- Start a NEW Thread