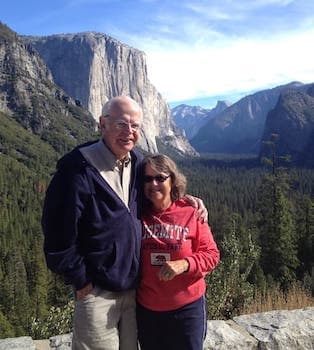
Curated with aloha by
Ted Mooney, P.E. RET
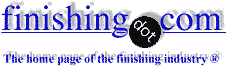
The authoritative public forum
for Metal Finishing 1989-2025
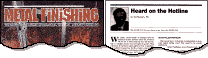
-----
Powdercoat Questions left unanswered in 2011
December 9, 2011
Q. There seem to be two questions of real significance to the Industry which keep re-surfacing:
(1) Has anyone worked out why the phenomenon of "outgassing" of HD Galvanised substrates occurs and how to totally eliminate it.
(2) Has anyone worked out how to duplicate the corrosion preventative properties of Hex Chrome Pre-treatment of Aluminium substrates especially the "self-healing" property"
I hope that these questions can be answered in the coming year.
Regards,
Bill
Trainer - Salamander Bay, Australia
A. The issue of "outgassing" (also known by several other names) is a mystery, but one with as many pet theories about it as theorists!
We have secured 2.5 years funding for a serious research program into this, and have just recruited the person who will conduct the research. We have the cooperation of a university and a major coatings manufacturer in the research, which will start in January.
(It has been delayed about 6 months due to governmental slow decision making in uncertain economic times).
I'll be encouraging the researcher, once he starts to use this forum to both share info and to seek observations, opinions, etc.
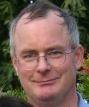
Geoff Crowley
Crithwood Ltd.
Westfield, Scotland, UK
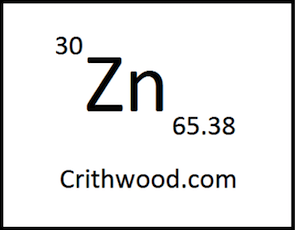
December 11, 2011
December 13, 2011
Q. That is a good start on question 1
I hope others will rally to answer that one.
My feeling however, is that such problems are best answered from the field.
The laboratory produces often unobtainable results in an industrial environment.
Can anyone venture an answer to question 2?
Regards,
Bill
Trainer - Salamander Bay, Australia
A. I agree that laboratories are not the best place to solve industrial problems, and that's why the research will be done in our plant, (but with analysis and inspection backup from University etc.)
The factory is where the problem is, and where the solution must be implemented, so in an operating industrial environment is where this research will be conducted.
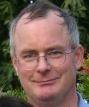
Geoff Crowley
Crithwood Ltd.
Westfield, Scotland, UK
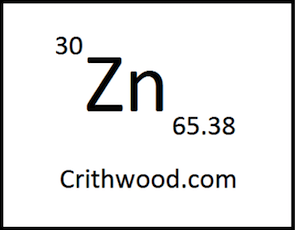
December 13, 2011
January 4, 2012
A. Hi,
I have worked for 5 years in an industry where we have to Powder coat on Hot dip Galvanized substrate. It was always a struggle against this "Out-gassing" issue.
The best way we have found was preheating the substrate at least 25° more than the max curing temperature (as per powder supplier). Also we keep the substrate inside the oven for longer duration at this temperature (we use batch oven for preheating). The greater the thickness of the material, the time will be greater correspondingly. After this operation we carry out pretreatment and normal drying before powder coating.
With this procedure we found the outgassing issue reduced up to 75%. But there are some materials, in spite of this procedure, that continue to release gas even on recoated substrates.
Different steel substrates at different HDG baths may give different results. Kindly share the experience if working in typical field.
Regards
- Chennai, Tamil Nadu, India
January 9, 2012
Q. I think that is the frustrating thing about the problem.
Preheating 25 ° C above Cure temp is common practice as is adding additives to the Powder to hold the surface open longer.
However, the problem still arises.
There is a factor that we are all missing I am afraid.
Regards,
Bill
Trainer - Salamander Bay, Australia
A. Our researcher has started this week, and while it will take a little while to get up to speed with our systems, process and procedures and other new job matters, I expect him to be on this case quickly. I don't anticipate a quick answer. There's funding for up to 2.5 years research.
We have identified 13 variables that seem to contribute to this issue, and guess that most need eliminating somehow, leaving the most influential variables needing controlled.
On so called "degassing" (preheating +25° C), for those using chromate or phosphate conversions, this is not a sensible solution, as it destroys the pretreatment. In any case it isn't the whole answer, as Bill has said.
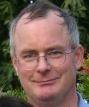
Geoff Crowley
Crithwood Ltd.
Westfield, Scotland, UK
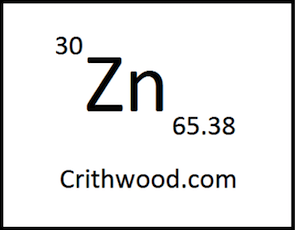
January 11, 2012
A. Preheating or special powders do not represent a definitive solution to the problem, there are too many variables. I think the only way to prevent this kind of defects is reduce the phenomenon itself by using less reactive steel grades for hot dip galvanizing in order to minimize the dendritic grow of the zeta phase and promote the presence of the final pure zinc phase.
Anna Telck- Berlin, Germany
January 12, 2012
"...by using less reactive steel grades for hot dip galvanizing in order to minimize the dendritic grow of the zeta phase and promote the presence of the final pure zinc phase..."
That's an interesting point, Anna. Do you have some experimental evidence that this is a gas evolving from the Fe/Zn alloy part of the galvanizing layers?
Is there a higher incidence of gassing in reactive steels?
We have not been able to correlate reactive and gassing yet.
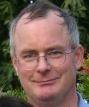
Geoff Crowley
Crithwood Ltd.
Westfield, Scotland, UK
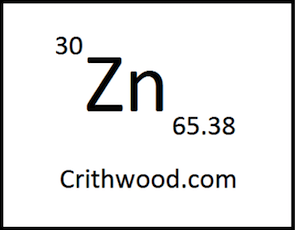
January 30, 2012
February 1, 2012
Hi Geoff,
The statement I made in the previous post is based both on experience in powder coating hot dip galvanized items and on metallographic microscopy observations of cross sections of coated samples.
I work for a powder coater and we sometimes coat huge hot dip galvanised girders; the steel used for such items is often a class C steel (according to afnor NF-A-35-503) with Si concentrations near to the upper limit of this class, and due to the thickness of the girders and the Si content of the substrate we always have to deal with zinc coating up to 300 microns in thickness, very fragile and with little or no pure zinc phase on top of the coating.
- Berlin
A. Geoff,
In our practical case we preheated the substrate and removed from the conveyor. Pre-treatment (phosphate or chromate) carried out after preheating. This eliminated heat effect on the treatment.
Our success rate was good even though there is a double handling of the product. We could not totally eradicate the problem but avoided rework to the maximum extent.
We have seen some metal structure created more gas issue in spite of above process. As everyone confirmed, this is a combination of many variables (steel, thickness, Zn thickness, etc.). Waiting for your further inputs.
- Chennai, Tamil Nadu, India
January 30, 2012
Powdercoat Unanswered Questions: self-healing alternative to hex chrome for aluminum, outgassing of galvanized surfaces
November 10, 2012Q. I have been involved in the Powdercoat Industry for more than 30 yrs.
I am a frequent contributor to this forum.
I asked these same questions ~12 months ago.
I still await an informed answer to either.
I understood some serious research was being done on these matters.
These are matters that confront every serious Powdercoater regularly.
Does any-one have the answers?
Q1: Has anyone come across a performance equivalent pre-treatment system to Hex Chrome for Aluminium (Aluminum for USA) especially with "self healing" properties after damage?
Q2: Has anyone come up with a solution to the outgassing problems when powdercoating HDG substrates (a solution not a minimisation as achieved by pre-overheating or adding wax additives to the consumable)?
I am really seeking answers to these problems.
Can any-one Help???
Regards,
Bill
Trainer - Salamander Bay, Australia
November 24, 2012
Q. Hello,
Is there anyone out there who can contribute to my questions?
I know the Hex Chrome question is not PC but if we allow all other nations to export superior performance products to us (i.e., Hex Chrome substrates) why do we penalise ourselves?
The outgassing Gal issue is also very important.
Cannot anyone offer answers?
Regards,
Bill
Trainer - Salamander Bay, Australia
A. Hi William.
As far as the U.S. government is concerned, MIL-DTL-5541 TCP trivalent chrome conversion coatings on aluminum are the full equivalent of hex chrome, even though you are correct of course that: they do not offer self-healing properties; they are not as robust & trouble-free; they are less reliable; they are not even visible such that an operator or QA inspector can catch defective parts which missed chromating.
opinion!
The only answer to your rhetorical question of why we impose Draconian limits on our own small businesses while letting megacorps import garbage from around the world is this disgusting one: megacorps own both the media and our government, while small business and the people don't.
After decades of U.S. cadmium discharge limits in the ppb range, which resulted in the closure of thousands of domestic plating shops and the loss of tens of thousands of American jobs, the megacorps imported Chinese children's jewelry with up to 70% pure cadmium, and Wal-Mart sold it. I naively expected outrage that would bring a sea change. So many shops closed for letting less cadmium down their sewer in a year than a toddler could lick off of that jewelry in a minute. I honestly expected a scandalous public recall that would cost those importers, jewelry companies, and big-box retailers hundreds of millions of dollars for their irresponsibility. Instead, the retailers were permitted to just silently remove the product from their shelves with no public announcement at all. The parents who found out were just quietly told to throw this bio-cumulative toxin into their household trash (at a thousand times the concentration which demands disposal in a secure toxic landfill).
And the situation never improved -- see
www.huffingtonpost.com/2012/10/14/cadmium-in-jewelry_n_1965192.html
I don't side with the Huffington Post often, but it utterly defies belief that our press and TV and elected officials absolutely refused to cover widespread poisoning of our children for fear it might offend the megacorporations. In the USA today, the lobbyists for a handful of megacorporations control both political parties, they run all of the regulatory agencies on a revolving door basis, and they own every major radio & TV stations and the major newspapers.
Whatever mega wants, mega gets; and mega wants you ... and me to just shut up and go away :-)
Regards,
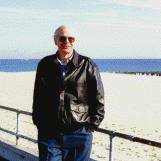
Ted Mooney, P.E.
Striving to live Aloha
finishing.com - Pine Beach, New Jersey
November 27, 2012
I think there were a lot of cranky old bums like us before Pearl Harbor as well.
Regards,
Bill
Trainer - Salamander Bay, Australia
A. Re. outgassing in galvanized steel substrates under powder coating:
We've had a materials scientist working on this issue for nearly a year. Its part funded by a government research grant.
The answer is not yet defined by this research, but some interesting factors have been uncovered. The steel chemistry is one of the apparently important factors, perhaps surprisingly. Another is the surface treatment of the zinc.
As this shapes up, we'll advise more, but a large randomised multifactorial trial is underway.
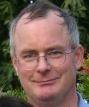
Geoff Crowley
Crithwood Ltd.
Westfield, Scotland, UK
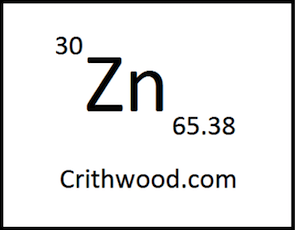
November 26, 2012
A. Geoff,
I observe the recent release of ASTM D7803.
I point this out just in case your own research programme might have hindered you from observing other efforts.
I also am aware that is unlikely, but just in case.
Regards,
Bill
Trainer - Salamander Bay, Australia
3rd year running the same enquiry re. Powdercoating
January 14, 2014Q. I wondered if anyone has come up with an equivalent to hex chrome for corrosion protection pre-treatment of Aluminium especially as to self-healing properties?
I also wonder if any progress has been made in identifying the causes of out-gassing on galvanised substrates?
Regards,
Bill
Trainer - Salamander Bay, Australia
January 17, 2014
A. Bill,
You might remember that I mentioned in this forum doing some research on outgassing.
In the UK funded by a Government outfit called the Technology Strategy Board, there are research grants available to part fund research in industry.
We applied for and got one such, a 20 month assignment to research the outgassing question. We're about 3/4 way through that time, during which we have had a scientist, supported by a university based in our place. He had conducted a number of trials, investigations and analysis. As suspected there turns out to be several contributing factors, and several categories of gassing showing several mechanisms. Some of these are far better understood, some still quite mysterious. One aspect that immediately came up was that good practices that management think are happening don't always, and that shortcuts are sometimes taken without authorisation. So a benefit to our company has been to sort those out. Next is to classify the mechanisms, and look at them to gain better understanding.
The outcome of this, in about June / July this year will be a full report on this topic, with the findings.
Its premature for me to say any conclusions, but I can say that there's no magic fix for the problem, rather the outcome will be a list of practice aspects, and material attributes that give rise to increased frequency.
One perhaps surprising aspect is steel chemistry. This is known in galvanizing to have an effect on galvanizing, but often not known that this effect moves on to powder coating on top of that galvanizing. Certain silicon levels lead to "reactive steel", which produces quite porous galvanising, which leads to moisture entrapment at a microscopic level which then leads to outgassing.
But these are not the only sources of problem.
Thats a long round-about way to say "watch this space".
Geoff
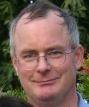
Geoff Crowley
Crithwood Ltd.
Westfield, Scotland, UK
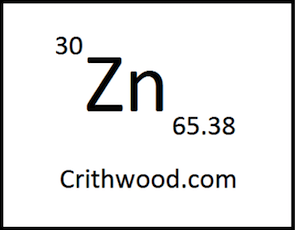
Q, A, or Comment on THIS thread -or- Start a NEW Thread