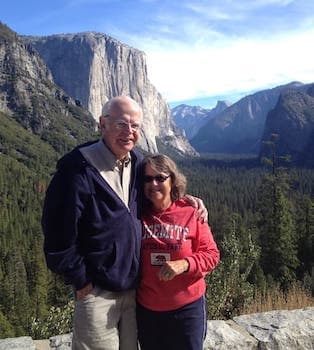
Curated with aloha by
Ted Mooney, P.E. RET
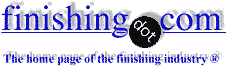
The authoritative public forum
for Metal Finishing 1989-2025
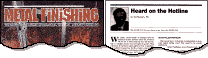
-----
How to drill EN7 AISI 100: carbide drill bits break
Question.
I have a project to make a part of an aircraft. The raw material is stainless steel EN7 Aisi 431 100 mm rod. It is very hard to machine it with High speed steel drills. I used a carbide bit drill but bits were broken. Tell me how to drill this material in easy way.
- Islamabad, Punjab, Pakistan
December 7, 2011
Drilling a hole in a 1 cm rod can be a bit of a problem, depending on the size of the hole. While it may not be time efficient, HSS should work and carbide should not have a problem as long as you have the proper feeds, speeds and lots of the appropriate cutting fluid.
You might want to try a couple of cobalt drills and make sure that they are sharp and properly sharpened.
- Navarre, Florida
First of two simultaneous responses -- December 9, 2011
It is not hard if you use the proper lubricant, speed, cutting edge and feed. Too much speed will cause overheat and hardening. Use generous amount of coolant and fast chip removal.
Guillermo MarrufoMonterrey, NL, Mexico
Second of two simultaneous responses -- December 10, 2011
Tahir, You do not say what diameter hole you want to drill, but it may be a good idea to cut the hole in stages, so you use a sequence of increasing sized drills. You should also consider what speed you cut at - there are tables available that will tell you the optimum cutting speeds for different metals and hardnesses. As the other respondents suggest - use a good cutting coolant/lubricant, but make sure the geometry of your drilling equipment is correct - you will be surprised at the number of broken drill bits that are caused by incorrect setups; the most common fault is not having the drill feed exactly perpendicular to the workpiece. One other suggestion - have a look at titanium nitride coated drill bits. They are very good a removing swarf as the bit cuts, but are only really effective if the drilling geometry is correct. I also believe that titanium nitride bits can also facilitate higher cutting rates because they are not so prone to overheating. As with all drill bits, make sure it is sharp and with the correct rake angle
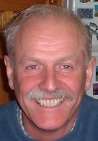
Trevor Crichton
R&D practical scientist
Chesham, Bucks, UK
December 28, 2011
EDM hole machine. Mechanical properties of the metal not important.
Dean Weathers- Medford, Oregon, USA
February 15, 2012
Q, A, or Comment on THIS thread -or- Start a NEW Thread