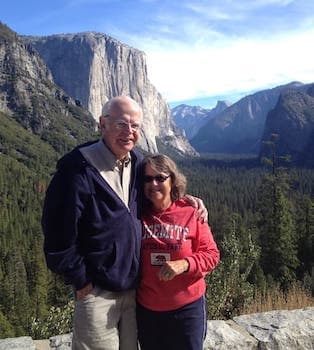
Curated with aloha by
Ted Mooney, P.E. RET
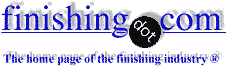
The authoritative public forum
for Metal Finishing 1989-2025
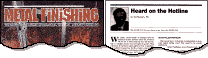
-----
Electroforming Copper onto Glass
November 18, 2011
Hello,
I am a PhD student doing research for school. I was given a task by my advisor to plate a glass cylinder with silver for use in a laser system. It needs to be a certain thickness for the EM wave to be trapped inside, essentially. We chose silver for it's high conductivity yielding a low thickness. This was several months ago.
After talking with a few people, I was told of a silver plating solution that would electroform above a certain temperature. To check this, I was able to electroform onto solid copper. I plated a few glass slides using vacuum evaporation with copper, silver, and even gold. The later two would dissolve off the slide as I placed them in the solution. The copper had better results, but it too would dissolve in places making it unusable. I now realize that this might be an adhesion problem, and that etching the glass in a HF solution might be a good idea.
But, instead, I was wondering if electroforming with copper might be a better idea. The conductivities of the two are close so the thickness would be as well. It also seems that dealing with the copper solution would be much easier. So, my questions are as follows:
1) Should I bother with trying to etch the glass in either case (silver or copper)?
2) Electroforming with copper, should I precoat the glass copper? (i.e. would it be harder to plate copper on copper rather than some other conductor?)
3) What solutions would you recommend? I am not going for shiny, just thick (about 10 microns)
Thanks for any advice and wisdom that you can offer!
Student - Chicago, Ilinois
For Glass you will need a layer of Chromium or Titanium as first layer, these can be sputtered with excellent adhesion on Glass. After that you should sputter a layer of a metal which is easy to activate for electroplating, copper should do fine. Maybe you need to sputter several layers with a cleaning procedure in between to avoid pinholes.
Good luck
- Zug Switzerland
November 24, 2011
I recommend that you contact a mirror manufacturing chemical supplier. They sell the necessary pre-treatment supplies and also copper and silver plating process chemicals for deposition onto glass.
Lyle Kirmanconsultant - Cleveland Heights, Ohio
November 29, 2011
December 14, 2011
Electroforming on a glass mandrel is quite commonplace. You first of all need to make sure the glass is as clean as possible by using conventional wet cleaning systems. Then you spray the glass using a twin headed spray gun - one jet sprays ammoniacal silver nitrate solution and the other sprays a reducer, such as dilute formaldehyde and glucose. The two jet sprays should combine about 6-10 cms from the glass surface; you will initially get a dark deposit, but this brightens up as the thickness increases. Keep the spray gun moving at all times. Do not overspray it or the deposit can become powdery. I would suggest spraying for about 30-45 seconds, but this will depend on the geometry and capacity of your system. Once coated, wash the glass and leave it for 24 hours to harden off.
Be careful - silver salts and ammonia
⇦ this on
eBay or
Amazon [affil links] solution can form a contact explosive, so make sure everything is thoroughly washed after use.
You can then electrodeposit metal onto the silvered glass, but you will probably need to ramp up the current. Make sure you have plenty of electrical contacts to the silver and start with a low current density. The precise current will depend on the metal being deposited. Once you have a reasonable deposit thickness (say 2-3 microns) you can start to increase the current to a more conventional current density. The trick to it is to take your time and be gentle!
Further information on this technology can be found in any technical article concerning the manufacture and production of vinyl records (if you remember them!) or CD's.
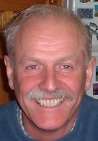
Trevor Crichton
R&D practical scientist
Chesham, Bucks, UK
Q, A, or Comment on THIS thread -or- Start a NEW Thread