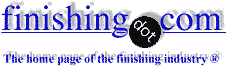
-----
Ways to untangle effluent treatment system mess
November 18, 2011
Hello,
I have, with no prior knowledge of metal finishing, inherited a plating shop that is in complete disarray. At the shop we do everything from electroless Ni to electroplating (Cr, Zn, Sn, Ni and Cu). The biggest challenge in trying to untangle this mess is the effluent treatment system.
We divide our waste water into 3 tanks:
1. Cyanide (treated using NaOCl)
2. Chrome (treated using Sodium meta bisulphite, soon to be replaced with Fe2SO4)
3. Misc
All of the following effluent lines are then combined and subjected to chemical precipitation (pH = 11 using Lime and then final pH = 7 using sulfuric acid)
After much tweaking we have managed meet all the discharge norms except for
A. free chlorine.
B. TDS ( average 6000 ppm)
C. SO4--
I have the following queries:
1. Are there any means of reducing TDS in the end of pipe effluent?
2. Will microfiltration be able to function with such high TDS?
3. Say microfiltration does work, will I then be able to pass the effluent through an RO system for recycling?
4. Are there any viable alternatives to chemical precipitation?
5. How can I reuse the rinse water from my room temp Zn-CN plating tank, because I suspect a large part of excess Cl is introduced during CN treatment.
I have many other queries but I shall save them for another post.
I will be eternally grateful if some would could give me some answers, or at least point me in the right direction.
I thank you for your time
Ravi
- Anand, Gujarat, India
November 18, 2011
Hi, Ravi.
Let me start with some general ideas on how to "untangle this mess" before going on to your specific questions. First, there are consultants who specialize in wastewater treatment for plating shops and who can guide you in this; obviously this costs money, which may be in short supply in a business that you've just taken over. In that case, at least talk to your chemical suppliers: it is in their best interest for you to succeed in business and even if they are not wastewater treatment experts, they may at least notice things that are obviously wrong. There are also excellent books on the subject, including Clarence Roy's "Operation and Maintenance of Surface Finishing Wastewater Treatment Systems" ⇦[this on eBay, Amazon, or AbeBooks affil links] and Kushner & Kushner's "Water and Waste Control for the Plating Shop" ⇦[this on eBay, Amazon, AbeBooks affil links]. These will help you understand how your equipment is supposed to work, and what it should be accomplishing in each step.
An important quasi-philosophical, quasi-practical thing to remember is that is your car won't start, the solution is not to replace it with a boat. By this I mean, don't address operational problems at this difficult time by changing technologies. Do that after things are no longer in "complete disarray". Thousands of plating shops successfully meet their effluent standards every day with conventional precipitation technology. It may not be the best solution for you for your long term future, but it is the best way to maintain sanity.
A. Free chlorine. The only place you should be using sodium hypochlorite is in cyanide treatment. Get some potassium iodide starch paper [affil links] (costs almost nothing) and frequently check that you are not over-chlorinating. If the paper is dark saturated purple, rather than lightly blue, you are overdosing. If the paper is white and you very strongly smell chlorine, there is the possibility that you are radically overdosing, so much so that you've bleached the paper while thinking you are undertreating :-)
B. If you have 6000 ppm of TDS, there is a good chance that you are not doing chemical precipitation properly. You should be doing "jar testing" in your laboratory to learn what is going on, rather than making running changes to the chemical treatment steps of the system. Often a cleaner or other process chemical exhibits a strong complexing effect.
C. I'm not sure about the excess S04--, but excessively raising and dropping pH expends SO4--, and again "jar testing" may help.
1., 2., 3., 4. Microfiltration is a fine technology but I would not introduce it until you thoroughly and completely understand, and have optimized, your existing treatment protocol. Similarly with other technology.
5. Although I have stressed that you should not jump to new technology to replace chemical precipitation, I do think you should get rid of cyanide zinc plating. It is just so unnecessary today. Talk to a supplier of an alkaline non-cyanide process. Good luck.
Regards,
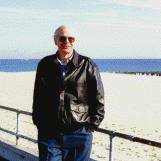
Ted Mooney, P.E.
Striving to live Aloha
finishing.com - Pine Beach, New Jersey
December 9, 2011
Thank you Mr Mooney,
Your advice was well sound, after much analysis of our WWTP system, we have managed to bring down daily out by close to 2000 liters. We are reusing close to 98% of our boiler steam distillate. Cyanide and Hexavalent chrome levels are under control etc.
Now to further reduce the effluent I have started looking into recovery technologies such as RO and electrodialysis,
I had a query about following electrolytic recovery processes:
1. Electrolytic oxidation of CN- and simultaneous recovery of Zn/Cu from their respective cyanide based plating rinses.
a. Is the addition of NaCl necessary to facilitate the oxidation of CN- or will the OH- generated be sufficient?
b. can I use a simple SS cathode to recover the Zn/Cu, and if so how can I separate the recovered metal from the cathode?
c. What are the normal process parameters? Should the solution be cooled so as to prevent the rapid evaporation of CL2 gas?
2. electrolytic removal of metallic impurities ( mainly Fe/Zn) from spent acid to prolong the life of a pickling bath.
a. I haven't actually read about such a process being employed for this purpose, but is the above possible? can the electrolytic 'cleaning' along with filtration prolong the life of my pickling acid bath?
I thank you for your time
Sincerely
Ravi
- Anand, Gujarat, India
Q, A, or Comment on THIS thread -or- Start a NEW Thread