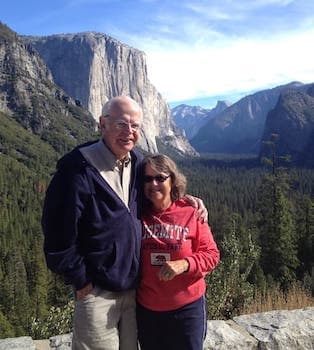
Curated with aloha by
Ted Mooney, P.E. RET
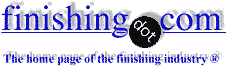
The authoritative public forum
for Metal Finishing 1989-2025
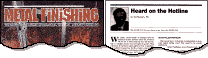
-----
Tin plating doesn't coat I.D. of tubing
October 31, 2011
During long types of copper, tubes from 40 mm to 90 mm in dia. the tin plating is not proper
as it doesn't reaches the center of the tube.
Please suggest some remedies for this.
Engineer - Mumbai, Maharahstra, India
First, "long" is a terribly relative term.
To plate the ID of a tube that is more than twice the diameter, you will need to use an aux internal anode which can be difficult
Then you probably will need to add solution flow to it either by pumping ir unique air agitation.
Pumped electroless solutions may work. Here again it requires good solution flow. If you can get strong air agitation directly under each tube, that may work. (like a percolator in a coffee pot)
It can be done, but it is neither easy or cheap.
- Navarre, Florida
First of two simultaneous responses -- October 31, 2011
Second of two simultaneous responses -- November 1, 2011
Hi Abhiraj,
Several things you may consider to improve throwing power:
1. Stronger solution flow inside pipe by increase circulation pump capacity, install sparger/nozzle, etc.
2. Reduce plating surface surface tension by running at higher temp and/or addition of wetting agent.
3. Longer plating time at lower current density.
4. Vibration and/or bumping of plating article (pipe) to get rid of trapped air bubbles and well as force plating solution inside the pipe.
5. Addition of proprietary plating additives to suppress plating at high current density (corner, etc) and accelerate plating at low current density region (center of inner pipe).
Regards,
David
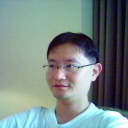
David Shiu
- Singapore
November 4, 2011
Have you considered using an alkaline tin plating bath? A sodium stannate plating bath has very good covering and throwing power. The plating efficiency drops at high current density so there is less tendency to get a heavy deposit in these areas. I plated cylindrical bushings with 0.05-0.1 mils of matte tin for a "flash" coating for both appearance and corrosion resistance. The ID's as well as the OD's were covered.
Lyle Kirman
consultant - Cleveland Heights, Ohio
November 14, 2011
I have a couple of suggestions. Firstly, use internal anodes, but this may be difficult to set up and jig; secondly, use an alkaline tin solution - this has much better throwing power than acid tin, and finally, try electroless tin.
Suggestions 1 and 2 can be combined and suggestion 3 may be expensive, but it should work if you have enough flow through the internal bore. However, when trying to deposit tin on the inner bore, make sure you have a clean internal surface, or nothing will adhere properly
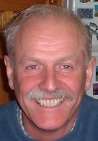
Trevor Crichton
R&D practical scientist
Chesham, Bucks, UK
Q, A, or Comment on THIS thread -or- Start a NEW Thread