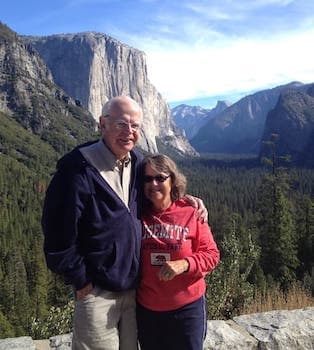
Curated with aloha by
Ted Mooney, P.E. RET
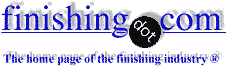
The authoritative public forum
for Metal Finishing 1989-2025
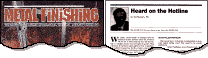
-----
Thick Plating on Complex Plastic Geometries
My name is Dave McCarthy. I am a graduate researcher at Virginia Tech in mechanical engineering investigating potential processes and applications for metal plating additively manufactured parts (i.e., rapid prototyped, 3D printed, etc.) with complex three dimensional geometries. As I am in the early stages of my work, I am hoping to hear suggestions from the finishing.com community on a few key points of my work.
The parts I'm attempting to plate are typically made of P400 ABS (used in fused deposition modeling) or DuraForm polyamide (used in selective laser sintering). Because the selective laser sintering process provides higher quality parts, I prefer to use the polyamide. The parts are complex cellular structures (picture a truss structure arrayed in three dimensions, creating a complicated mesh that is full of holes).
Due to the complexity of the parts, I have had little luck using a (hobby kit) standard acid copper electroplating method (preceded by silver paint or silver sulfide deposition to make conductive) because of the geometric dependency of the electroplating process (i.e., outer features nearest the anode receive a very thick plate while inner features receive no plate at all).
I am looking for suggestions on how best to go about plating these complex parts. My goal is to produce very thick plates on the parts (at least 250 microns, preferably closer to 500 microns) so that the plating would be self-supporting (plus some additional factor of safety) if I burn out the polymer structure (similar to electroforming).
Should I attempt a copper flash with a higher throwing power to help plate the inner features? My inclination is to attempt thick electroless nickel coats (despite the relatively high price) to obtain consistent plating layers throughout the geometry, but I need to complete an etching process first and I doubt the ABS or polyamide are plating-grade. I already have a hobby electroless nickel plating kit, but it's meant to be used after a copper flash that I'm not sure I'll be able to do. It's not clear if it's usable on an etched part, though I plan to work with their technical support to determine if that's possible. I also haven't come across any instances in my literature search where people have attempted thick layers exclusively from electroless plating (making me uncertain if it's possible).
Any suggestions are much appreciated. I have a copy of Standards & Guidelines for Electroplated Plastics on hold from the library and will have it available to me within the next few weeks.
Thank you in advance for your suggestions,
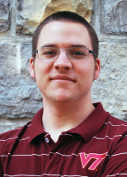
David McCarthy
Student/Researcher - Blacksburg, Virginia, USA
October 24, 2011
Q, A, or Comment on THIS thread -or- Start a NEW Thread