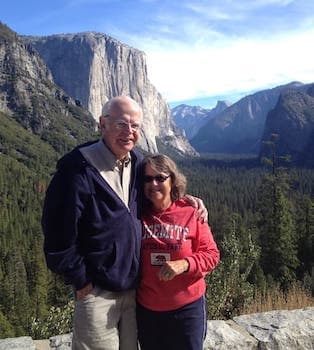
Curated with aloha by
Ted Mooney, P.E. RET
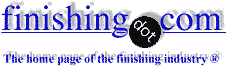
The authoritative public forum
for Metal Finishing 1989-2025
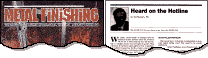
-----
Design of the dipping screws for a pipe galvanizing line
October 18, 2011
We have traditionally used a profiled plate design for the dipping screws used in our pipe galvanizing plant.
One of our managers recently visited a pipe factory where the dipping screws are made from round bar instead of the conventional profiled plate design. The production manager at the galvanizing line claimed this is a newer design and that it has many benefits over the plate type.
It is the first time we learned about the bar design and I've been asked to look at this as an option. Please can you give us some guidelines on this from your experience?
- Are there real advantages or disadvantages of one over the other?
- If the bar-design is preferable, would it possible to retrofit this?
- Are there any interface or operational problems when changing the design?
I approached our regular supplier and they are loathe to discuss this ... Please help!
Galvaniser - Johannesburg, South Africa
October 20, 2011
Sir:
I believe the screws you require are the ventilated, progressive screw type, which are excellent.
Galvanizing Consultant - Hot Springs, South Dakota, USA
October 24, 2011
Thank you Dr. Cook.
Yes, our screws are progressive (larger pitch on first 3/4 turn) and ventilated (oval draining holes every 90 degrees on middle 3 to 7 spirals, depending on the pitch of the screw).
Our current design is 15 mm plate, increased from 10 mm in the original design to reduce mechanical damage and improve life. The alternative is a similarly progressive screw fashioned from 30 mm diameter round bar with 50 x 20 flat bar spokes every 90 degrees. *Claimed* (i.e. unconfirmed) befits are:
- Mechanically stronger hence less damage
- Longer useful life (smaller contact area, less wear and tear)
- Less dross and ash formation (smaller surface area)
- Less energy absorbed when inserted in the bath (lower mass
- Less damage on thin wall tube and pipe (larger "landing area" of 50 mm flatbar vs edge of 15 mm plate)
Some of these claimed benefits are very attractive. However we have not tested this design and cannot vouch if these are real.
I am wondering if someone has experience using the roundbar-type spirals and if these claimed advantages are real. On the flip side I'd like to know if there are significant disadvantages to changing the design (decreased vertical clearance, i.e. size range, is one).
Thank you.
Francois
- Johannesburg, South Africa
Q, A, or Comment on THIS thread -or- Start a NEW Thread