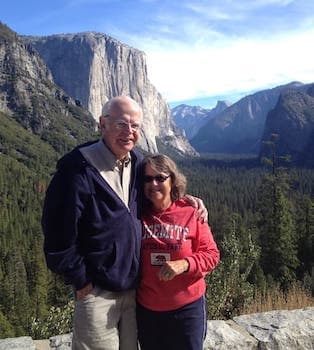
Curated with aloha by
Ted Mooney, P.E. RET
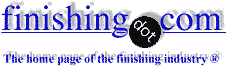
The authoritative public forum
for Metal Finishing 1989-2025
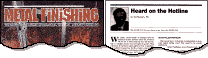
-----
Primer failed dry tape adhesion test
Q. We have two batches of detail anodized and primed parts. The primer is BMS10-11, Class A, Grade E. It was cured at 30 °C for more than 8 hours. But two months later we dry tape tested these parts and found many of them failed the test. Could you please offer me any possible cause?
Marshall Zhangspecial process control engineer - China
October 17, 2011
A. Marshall,
You really need to give us more details about the processes that have gone on, e.g. which anodising (chromic, sulfuric, modified sulfuric, phosphoric etc), whether the anodising was sealed or not, the length of time between anodising and painting etc. This way we may be able to give a reasoned explanation about what is happening.
In my experience paint adhesion problems can be caused by numerous reasons such as painting on aged or sealed anodising, contaminated surfaces, incorrect paint application or curing etc, etc...
Aerospace - Yeovil, Somerset, UK
October 19, 2011
Q. Details are as follows: parts were chromic acid anodized and sealed per BAC 5709. And the time between drying after sealing and applying paint,for some parts was more than 20 minutes, for other parts longer than 1 hour. At that period, the curing oven was broken, so all primed parts were cured at room temperature for more than 8 hours. Then environmental temperature was 30° C and humidity less than 65%. Most of the batch of 44 parts failed the dry tape adhesion test.
Marshall Zhang- China
October 22, 2011
A. Hi Marshall,
From what you have said so far there is no obvious reason for your failure of the dry tape test.
I am not a fan of sealing anodising prior to painting, it reduces the effectiveness of the anodising to act as a key. I personally believe it will reduce coating adhesion.
Your time delays between anodising and paint are fine. This shouldn't be the issue. Delay times between anodising and paint only really apply to unsealed coatings where you would want to paint within 16 hours (approximately) of anodising.
Did you tape test after curing? I am curious as to whether this is something that has developed over time or whether it has always been there.
Aerospace - Yeovil, Somerset, UK
November 3, 2011
Q. Yes, dry tape adhesion test had been done after cure of the paint. Paint inspectors said they did not detect any failure at that time. They also conducted other sampling tests, including aluminum rod test, wet adhesion test, solvent resistant test. All these tests was performed 48 hours after cure and all passed.
Marshall Zhang- China
December 1, 2011
A. Hi Marshall,
As your failures are happening two months after initial application of the paint and the parts pass inspection at time of painting you are going to have to look at the storage conditions during that two months.
I would personally look for evidence of excessively high humidity and/or temperature, any possibility of solvent attack or chemical attack and any other extraneous conditions which would not normally occur during storage.
Aerospace - Yeovil, Somerset, UK
December 5, 2011
A. There are three things that I would recommend, the first is the easiest. How is your tape test tape stored? The tape is required to be in a controlled environment. Are you sure its approved tape test tape? You can get a certification with the tape, I would recommend doing this. Has your tape expired?
Next, how is your paint being mixed? This might not even be an issue. I would think if it wasn't mixed properly it would fail right away. But you never know. Is your paint within it's expiration date? Your paint should also come with certifications.
Lastly, there is something wrong with your chromic anodize. While it is easy to titrate, it might be a real pain trying to fix the problem. Is there a good coating weight on the sample panels? Do you have enough free acid in your tanks? There could be an electrical issue and some fuses could need to be replaced in the rectifier.
I hope by now you've figured out what your issue was but if not, at least this is a starting point.
- Savannah Georgia USA
December 22, 2011
February 18, 2013
Q. Hello everyone,
I have a problem related to primed products of ours.
I am working as an R&D Engineer and we produce PVC, ABS (polymers) edgebands. We prime these edgebands and send to the customer. The customer then glues these to the other wooden products.
Recently we experience that the primer doesn't stick on the edgeband when the customer wants to glue it to its products (furnitures etc.) Honestly we don't have a practical test method to understand how good the products are primed. The primed products are only checked by the operators in a very primitive way (only by looking at it and scratching by nail) and in most cases even though the primed surfaces seem quite ok and ready to stick, either they can't be glued or they simply come off when the customer tries.
Do you know any practical quality control test, which enables us to understand if we have a good primed surface? And do you have any idea why we have this adhesion problem of primers?? (The surfaces are primed at room temperature/ we use a good quality of primers/we pay attention to the viscosity and the solid content of the primers)
Thank you very much for your interest in advance. I am open to your ideas and suggestions.
Kind Regards
- TURKEY
Q, A, or Comment on THIS thread -or- Start a NEW Thread