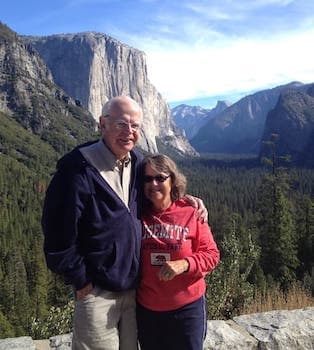
Curated with aloha by
Ted Mooney, P.E. RET
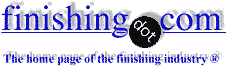
The authoritative public forum
for Metal Finishing 1989-2025
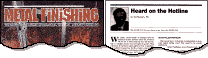
-----
Most durable, long life coating for aluminium castings
October 7, 2011
I would be very grateful for advice on some coating issues we have had - we 'think' we have resolved them but I am always keen to try and improve our products wherever possible and wondered if anyone might have any thoughts that could help us regarding the powder coat degradation that occurred (since rectified as far as we can tell by Alochroming pretreatment prior to powder coating)
When we started making our aluminium sand cast cigarette bins we were using a company in the UK to coat the bodies and doors and they used a two pac wet spray process (presumably with a zinc chromate primer) and this worked well.
We then moved to powder coating at our metal fabrication and assembly factory (also great suppliers) at TOC in Coventry - at first they were powder coating straight onto a sand blasted aluminium surface but coatings started to flake off after a year or so. A client suggested we try an etch primer before powder coating but this seemed to make the problem worse. We even tried stove enameling but the finish the supplier provided was so bad you could actually blow it off (so we stopped exploring anything with them).
Since we started we have always specified an anti-graffiti element in the coatings as we want to make the bins as resistant to vandalism as possible. I am never sure whether it was this element that meant the coatings did not last or the wrong primer being used.
For a brief period we had so many problems we ended up reinvestigating the whole thing again and moved to Aluchrome dipping the bins after they were sand blasted - then powder coating within 18 hours of Aluchroming.
This process seems to be working very well now (it looks to be working as well or better than the original two-pack coatings) but we have only had bins on trial with this process for about 6 months. You can see the two images here that are of bins that were Aluchromed which look fairly intact compared to the others which show the powder coat has degraded very badly in a matter of months.
What I am interested in is any advice that may help us deliver bullet proof coatings, that resist stickers and graffitti and last for 10 years plus - which are cost effective to apply and give great wear and corrosion resistance (even in presence of cigarette ash) and UV resistance. We want to coat them once and be confident we can forget about them. They must be sef-healing in cases of scratches as bins suffer from considerable abuse on the street.
Questions:
1. Is Aluchroming followed by powder coating the most durable finish for our exterior products (which involve a lot of ash)
2. What powder coat formulation you might recommend?
3. Should powder coating be thicker? Is this possible? Will this increase the resistance to corrosion and degradation of the coating? How might we achieve this?
4. Is a two pac wet spray coating more reliable than powder coating? Is it cost effective?
5. How might we offer a refurbishment on site process - e.g., would we sand the bin down on site, paint on a chromate anti corrosion liquid and then paint when dry to match a RAL colour? Any advice on suitable materials would be very welcome - not sure where I can source RAL specific satin top coat paints for this refurbishment on site.
6. Finally - is there anything than can be done to make the final coatings repel stickers as well as graffiti? The current anti-graffiti coating does not seem to stop paint being sprayed onto the bins - I am guessing it just makes it a bit easier to get the graffiti off? Not sure what the anti-graffiti element in our powder coatings is adding at the moment. We have tried tpfe coatings and they do repel stickers very well but are extremely expensive and seem to attract dust.
Note: All our coatings come from hmgpowdercoatings.co.uk in the UK. We have looked into some coatings from other suppliers but they seemed massively expensive and not to improve the performance much. I wondered whether using Qualicoat architectural systems would be overkill or affordable. We want our products to be bullet proof, resist stickers and graffiti but Council clients won't pay unlimited sums for bins as you can imagine. We still have to be competitive.
I also wondered if any grades of aluminium might be better for our purpose - I know our foundry seemed to have trialed different grades of aluminium without telling us they were experimenting (which will be very frustrating if the coating problems were partly down to the aluminium grade (e.g., more magnesium in one grade than another affecting the coating in the powder coat ovens under temperature). I also wondered if degassing the castings before coating them would make any perceptible difference.
It's very difficult to get to the bottom of coating issues as everyone has a different view - we have got to where we are now by trial and error (at some cost as we have had to refurbish bins when the etch prime and powder coat system proved unsuitable).
For example - looking at the bins enclosed - what might we do to restore these as well as possible on site e.g. sandpaper down the affected area, apply some sort of painted on chromate or other anti corrosion primer (specifically for aluminium) and then paint on a RAL colour satin finish paint or coating which will stay looking good? Do you think this is possible as a self-refurb option that Councils could effect themselves instead of returning the bins to base.
Most of our bins are black but we have had various RAL colours and it would be good to have the same colours in a paintable format (or spray cans but I am worried about this being used on the street blowing around).
Apologies for the length of this posting and very grateful for any advice
Thank you!! A
Product Designer/Manufacturer - London, UK
Q, A, or Comment on THIS thread -or- Start a NEW Thread