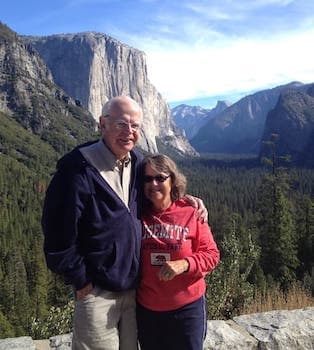
Curated with aloha by
Ted Mooney, P.E. RET
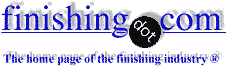
The authoritative public forum
for Metal Finishing 1989-2025
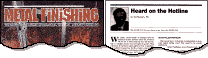
-----
Powdercoating heavy steel sections with one coat
We have investigated and seen the (exceptionally good) results of a single powder coat applied to heavy steel sections.
The process is to sandblast the steel, heat the product to get a full 'soak' and then apply one coat of powder electrostatically.
We are investigating doing the same, however we cannot find out if this is 'approved' or not, as we do not wish to make the investment and then find we need to apply two coats instead of one.
Applying two coats would render the operation uneconomical.
Luke
Manufacturer - Hastings, New Zealand
September 27, 2011
I'm not sure what is meant by 'approved'. The overall specification from your clients will be for the performance of the applied coating and not how it is achieved. I would suggest that some clients where this coated item is destined for interior locations will be quite satisfied with 'one coat'. Then you will have others requiring additional corrosion resistance and a 'one coat' finish will not meet with those needs. This is due to at point in the future some damage to the coating that will allow the elements to enter and cause rust creep. The only option for a 'one coat' finish that may satisfy all comers would be to apply a zinc rich powder primer that can be brush painted by a client to a 'in house colour' at a later date.
Terry HicklingBirmingham, United Kingdom
September 29, 2011
October 1, 2011
We routinely coat heavy steel sections with a single coat in powdercoating.
It is mostly galvanized steel, but sometimes shotblasted steel also. (Terry says there's only one option, a zinc rich undercoat, but galvanized steel is another option)
By "heavy" I mean typically 10-20 mm thickness, but we have successfully coated up to 50mm.
Some careful calculation of the curing time is required.
This is done to an "approved" method. Pretreatment is more important consideration that steel thickness.
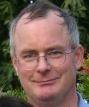
Geoff Crowley
Crithwood Ltd.
Westfield, Scotland, UK
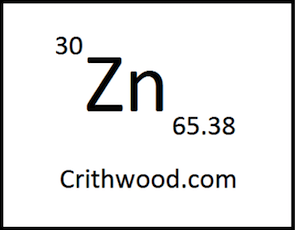
A. The problem, of course, is how do you maintain the integrity of pretreatment whist pre-heating heavy sections.
Most certainly it is possible to Blast, pre-heat and apply powder for aesthetic appearance.
To gain true anti-corrosion & aesthetic appearance requires chemical pretreatment because of the micro-porosity of normal polyester powdercoat consumables.
It might be worthwhile visiting Thermoplastic Coatings if UV resistance is required.
If UV resistance is not a requirement then Fusion Bond Epoxy could be the answer.
Hope this helps,
Regards,
Bill
Trainer - Salamander Bay, Australia
Bill,
not sure why you wonder about the integrity of the chemical pretreatment on heavy steel (as opposed to lighter weight?)
Surely it's the temperature reached that might compromise the pretreatment not the duration at a temp? And only real difference between heavy and lighter sections is a time element. Longer to dry, longer to cure - as it takes longer to get to cure temp.
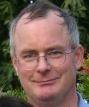
Geoff Crowley
Crithwood Ltd.
Westfield, Scotland, UK
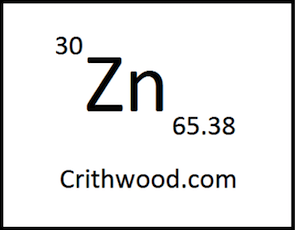
I totally agree regarding Temperature being a greater villain than time.
The problem I wrestle with is that it usually means introducing higher temperatures of convective air to raise high mass articles to lesser temperature.
This exposes the surfaces which are pre-treated to this thermal shock.
If you have the luxury of time to gradually build that temperature all would be fine.
I suspect not many have that luxury.
However, I am here to learn as well.
I would be really interested in your response to the request I made for your contribution to the debate about outgassing in Gal Substrates?
Regards,
Bill
Trainer - Salamander Bay, Australia
William: re outgassing on galv..
The research on this issue was slow to get going, but has now started. An advert has been placed for a researcher for a post for up to 2.5 years to solve this one.
The university are meantime analysing some samples to kick the job off.
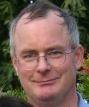
Geoff Crowley
Crithwood Ltd.
Westfield, Scotland, UK
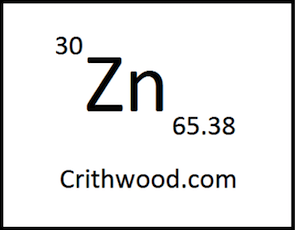
Q, A, or Comment on THIS thread -or- Start a NEW Thread