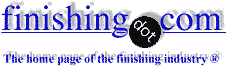
-----
Poor adhesion on nickel-chromium plating
September 18, 2011
Hello I'm a university student in Thailand. And I do research about reducing waste in the manufacturing process. Process is nickel-chromium plating on fuel cap.
Flow Process is
1. Semi-bright nickel 4 times 2.5mins/times
- Nickel Sulphate 280 g/L, Nickel Chloride 40 g/L, Boric Acid 45 g/L, Ni 2110 12 cc/l, Ni 2100 0.1 cc/l, Ni 2120 0.5 cc/l, Wetting Agent 2 cc/l
2. Dip in water 2.5 mins
3. High sulfur Nickel 2.5 mins
- Nickel Sulphate 300 g/L, Nickel Chloride 88 g/L, Boric Acid 36 g/L, Tri - Strike 15cc/l
4. Dip in water 2.5 mins
5. bright Nickel 4 times 2.5mins/times
- Nickel Sulphate 280 g/L, Nickel Chloride 40 g/L, Boric Acid 65 g/L, Ni 2720 4 cc/l, Ni 2700 0.6 cc/l, Ni 2710 4 cc/l, Wetting Agent 2 cc/l
6. dip in water 4 times 2.5mins/times
7. dip in CR Activator 5-10%
8. Chrome 6+ 2.5 mins
- Chromic Acid 200, Sulfuric Acid 0.54 g/l, Additive AG 20 cc/l, Additive BF 20 cc/l
Every step is continuous flow
Now, I think that peeling and poor adhesion problem occur from nickel to nickel (semi bright to bright layer of nickel, and bright nickel to chrome layer. But I don't know that problems are come from more.
And I have Questions, everybody would answer me, please.
1. What method I can examine the peeling from what layer?
2. Peeling problem occur mostly between layers?
3. What cause of the peeling problem from? I want to know both nickel to nickel (semi bright to bright layer of nickel, and bright nickel to chrome layer
4. And what's solution about that? I want to know both nickel to nickel (semi bright to bright layer of nickel, and bright nickel to chrome layer
Between plating bright nickel to chrome layer have dip in water 2.5 . It have effect to peeling problem?
Thanks in Advance.
- Thailand
September 19, 2011
Hi, Narinpat.
When you list plating times like "4 times 2.5mins/times", I assume that this is an automatic plating line with four continuous stations of plating time, and there is not actually a current interruption every 2-1/2 minutes? The rinse times seem too long and can lead to passivation. 10 minutes of rinsing after bright nickel plating sounds like a killer. I've never seen nickel rinsed for 10 minutes before chrome plating, and tend to believe that excess rinsing time is the cause of the adhesion problems.
Is there anything that can be done about that, or is this an automatic plating machine with a fixed amount of time per station?
Regards,
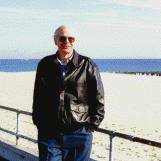
Ted Mooney, P.E.
Striving to live Aloha
finishing.com - Pine Beach, New Jersey
September 21, 2011
THANKS Mr Ted
Flow fixed amount of time per station. Every station are 2.5 min/times.
I want to know that if I cut out rinse process but I will still dip in CR Activator 5-10%, it have effect to peeling problem?
Thanks in advance for more suggestions
Student - THAILAND
September 22, 2011
Hi, Narinpat. Sorry, but I don't think we can say that.
There are two common causes of nickel peeling: the work not being clean enough, or the nickel getting passivated. I think you know enough about your situation to have ruled out the first possibility. I think you now need to find out at which step the nickel is passivating. Some ways to do that might include examining the blisters and the surface below the blisters to see if you can determine where the separation took place. Microscopic cross-sectioning might help if visual inspection doesn't do it.
Nobody can guarantee that changing something will cure the problem before we determine exactly what the problem is.
Regards,
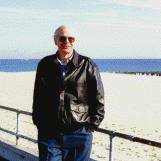
Ted Mooney, P.E.
Striving to live Aloha
finishing.com - Pine Beach, New Jersey
Q, A, or Comment on THIS thread -or- Start a NEW Thread