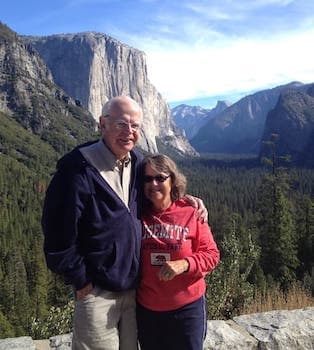
Curated with aloha by
Ted Mooney, P.E. RET
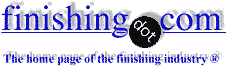
The authoritative public forum
for Metal Finishing 1989-2025
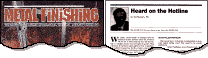
-----
Electroless Nickel Plating of Mn-Cu-Ni Alloy
September 8, 2011
I have a manganese-copper-nickel alloy (72%-18%-10%) washer that was originally designed with an EN/PTFE coating. Our current supplier has said that the treatment of this alloy is contaminating his plating bath and now wants to charge 5 times the original unit price plus charge us for chemical disposal and new bath make up. Understandably my company balked at this idea and have asked if it is possible to investigate whether we can use other coatings.
The coating is purely for corrosion protection so I was thinking that EN would be much easier to to source, if nothing else. My question: what would be the best pre-treatment for this alloy so that it could be successfully EN plated (preferably without killing the bath and incurring huge disposal costs)?
This query is similar to letter no 53855, but there wasn't an answer to that query.
Any help greatly appreciated.
The guy stuck in the middle between Purchasing and Design!! - Yeovil, Somerset, UK
If it is for corrosion protection, why the mega expensive EN/Teflon and not the less expensive plain EN?
As far as it killing his tank, that is his problem, because he took the job knowing what the metal was. That said, I would love to know why he thinks that your metal killed it. It is possible, but I have never heard of it so would like to know.
I can not find a published pre plate process for manganese.
I suspect that it will require a nickel strike prior to EN to protect the tank and/or get adhesion. It might possibly take a copper strike followed by a nickel strike.
If he had adhesion with the plated parts, he could always use a low voltage jumper for the rack and go in hot for a min or so. This way, the chemicals would not attack the parent alloy-IE instant coverage.
Finally, what in the world is this alloy used for. It has to be expensive as it is "exotic".
- Navarre, Florida
First of two simultaneous responses -- September 9, 2011
Hello, Brian. I had a similar experience with a different alloy at one time. Our solution was to initially apply 3 volts or so to the parts with a live entry using a portable rectifier. After a few minutes, we turned off the rectifier and plated electroless to the desired thickness. The live entry got a thin plating of nickel immediately started and prevented any of the basis metal from souring the nickel bath. This may not be the best solution in your case, but I thought I would throw it out there for consideration.
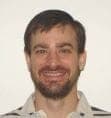
Jon Barrows, MSF, EHSSC
Independence, Missouri
Second of two simultaneous responses -- September 9, 2011
Hi James,
You are right, haven't got the faintest idea why the designer picked EN/PTFE for corrosion protection, I just have to pick up the pieces when it all falls over!!
I want to go to straight high phos EN as this is purely for corrosion protection. I think striking with nickel or copper and nickel is probably the best way to go (must admit to being a little surprised that the supplier isn't doing that already, if he was there wouldn't be a contamination issue), any ideas on activation prior to strike?
Hi Jon,
For a few jobs I have used the going in live for a minute or so, well worth a look.
Before we do anything here I have to convince the designers that this is the best way to go, not as easy a task as it sounds :)
Aerospace - Yeovil, Somerset, UK
September 13, 2011
Q, A, or Comment on THIS thread -or- Start a NEW Thread