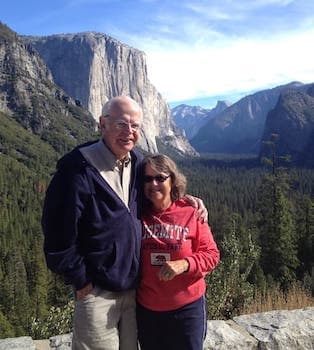
Curated with aloha by
Ted Mooney, P.E. RET
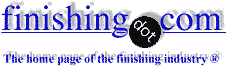
The authoritative public forum
for Metal Finishing 1989-2025
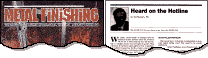
-----
Replace electroless nickel plating on aluminium heatsink
August 31, 2011
Hello,
I am wondering if somebody could help me on a recurrent problem. I am a mechanical designer in France. I have been designing aluminium heatsinks for press-pack high power semi-conductor for 10 years now.
example:
www05.abb.com/global/scot/scot256.nsf/veritydisplay/51237a995b14a4ffc1257332002be211/$file/5sya2036-03%20june%2006%20mechanical%20clamping.pdf
Most of our customers used to ask us a chemical nickel coating on their products.
Get a look on that:
For applications with
hard component stress, ABB recommends chemical plating rather than electrolytic plating. Bare copper or
aluminium is not recommended due to corrosion that rapidly deteriorates the contact surfaces. Nickel and silver do corrode, however nickel and silver oxide do not deteriorate the interface to the same extent as
aluminium oxide. The ABB press-pack high power semiconductors have pole pieces of copper with a nickel
plating of approximately 5 µ. When using nickel plating it is recommended to use the same plating thickness on the heat-sink area that is in contact with the device.
However our treatment nickel is really weak against moisture, humidity and so on. Even one single droplet could screw up a whole product. As far, in this system the nickel treatment is used only for the electrical contact.
Thus I am wondering if you'd know a coating that can respect:
- Corrosion layer won't affect the electric contact (as explained in ABB extract)
- Admit contact with the nickel plating (component)
Designer - France
Hi, Motch.
My first impression is that electroless nickel plating is the correct coating but that 5 µ is not nearly enough for a cast aluminum component. That might be enough for a machined copper component, but for cast aluminum I think more like 25 µ (0.001") would be appropriate.
Regards,
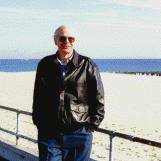
Ted Mooney, P.E.
Striving to live Aloha
finishing.com - Pine Beach, New Jersey
August 31, 2011
It sounds like the electroless nickel deposit is too thin and/or has defects (porosity, etc.) if corrosion readily develops in moist, humid air. Typical thickness for aluminium heat sinks is at least 10 micrometers. Also, do you know what type of electroless nickel is being used, meaning low-, mid-, or high-phosphorus? The best corrosion resistance is obtained with mid-P (6-9% P) or high-P (10-13%) coatings. I suggest having some of the plated parts cross-sectioned to determine if the coating is continuous, or if it has extensive porosity or other defects.
Toby PadfieldAutomotive supplier - Michigan, USA
September 8, 2011
Q, A, or Comment on THIS thread -or- Start a NEW Thread