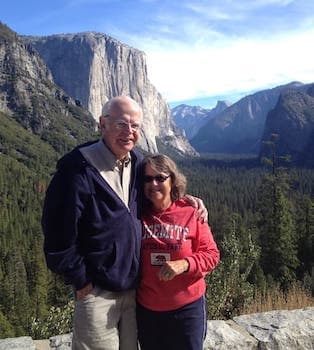
Curated with aloha by
Ted Mooney, P.E. RET
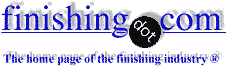
The authoritative public forum
for Metal Finishing 1989-2025
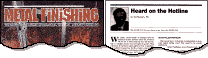
-----
Control of powder coat texture
August 31, 2011
Q. My questions are about quality expectations and control of textured powder coat.
My application involves:
1. A bright white color
2. A fine texture to allow fine-feature silkscreening. Some rather small text is involved--smallest being about .1" tall.
The situation:
1. I changed the specification from a gloss finish to a fine texture to mask out pressed-in sheet metal hardware and impurities which were visually unacceptable.
2. After consultation with the finisher, we arrived at a spec and ran samples, which I subsequently tested of silkscreening with very acceptable results.
3. The first articles, however, exhibited a different, much rougher, texture, which did not silkscreen well. In addition to having the less well-defined edges, the ink tended to settle in the valleys and make the color appear lighter.
4. The finisher claims that this is impossible to control due to factors such as humidity, etc.
My question:
1. Is this true and can I expect no better results from a specification like this?
2. Are there ways to control the fineness of the texture to the degree necessary?
3. Are there other alternative finish options you would recommend for the application, given the application requirements?
Thanks for your help.
Product Manager - Lenexa, Kansas, USA
![]() |
A. I will offer the guess that there is a paint shop in your area than can control it better. May be further away and may cost more. High quality normally costs more. James Watts- Navarre, Florida September 1, 2011 September 1, 2011 A. I would suggest you check comparative coating thickness and cure. Trainer - Salamander Bay, Australia A. It is very difficult for your powder coater to control the texture to accommodate the requirements of your follow-on system. Clients requiring just a decorative finish, this would be acceptable. Therefore, I would suggest that you also evaluate a matt version of a white powder and if you can't obtain the whiteness necessary, look for a wrinkle white version. As terminology may vary UK/USA--by a wrinkle white powder I mean it has a surface finish similar to sandpaper there are various grades (fine coarse) and I suggest that more continuity will be achieved. Terry HicklingBirmingham, United Kingdom September 1, 2011 |
Q. Thank you all for your responses.
First clarification--yes the thickness of the rougher parts was 4-5 mils, as compared to 2-3 mils for the 1st article (the acceptable parts). So thickness is a (perhaps the) differentiating factor.
Second clarification--this powder is a wrinkle finish, i.e., it has the rough sandpaper texture. This is what I meant by texture, but I know there are quite a variety of textures out there.
I'm not sure if its OK to post the exact powder spec--I could certainly email it if helpful.
Thanks, again.
- Lenexa, Kansas
September 2, 2011
----
Ed. note: Posting your powder spec isn't a problem, Carl, thanks. But it can encourage problematic "answers" which we can't post like: "You wouldn't have that problem if you used our powder" :-)
September 7, 2011
A. I thought as much.
The texture of a powdercoat is determined by formulation.
The only real ways you can achieve variance are:
Alteration of the formula.
Alteration of the Cure Schedule to influence flow.
Alteration of applied film thickness.
Obviously, applied film thickness is the culprit here.
In future you specify that your product is treated with powder from a batch production lot which is satisfactory.
(Powder Manufacturers will apply a batch no & usually a box no on every box of Powder they produce)
You specify a cure schedule and insist on a time / temperature graph of metal temperature (not oven air temperature)
You specify an acceptable coating thickness range (usually + or-10 microns is achievable.)
All of a sudden your problem is no more.
Glad to have helped.
Please send Kentucky Bourbon.
Regards,
Bill
Trainer - Salamander Bay, Australia
September 7, 2011
A. Hold the bourbon.
I neglected to advise that "special effect" including texture powders should always be fed from an aeration hopper feed not a vibratory system.
Special consideration should also be given to minimising the ratio of reclaim to virgin powder in a recycle system.
Both can adversely affect consistency of product.
I will try harder next time.
Regards,
Bill
Trainer - Salamander Bay, Australia
Again, thanks to all--such erudition.
I will look into all this, but it sounds like this route involves quite a bit of additional expense, and probably another powder coater.
But, very helpful.
Product Manager
September 9, 2011
- Lenexa, Kansas, USA
September 10, 2011
A. Au contraire!
There is no additional expense involved.
There is possibly no need to look for another coater.
There may be a need to set down a specification from which both you and the coater can benefit.
Maybe you can commercially benefit by providing the coater with an avenue for improvement.
In my experience, many of them quest for knowledge but no-one offers it.
Try it on.
You have nothing to lose and you both have a lot to gain.
I guess the Bourbon Question might arise again though?
Regards,
Bill
Trainer - Salamander Bay, Australia
September 14, 2011
William:
An Aussie who speaks French! Hence, no doubt, your interest in Bourbon.
I'll give it a try. I have been in touch with another local company that is more oriented to batch production, which seems like it might be promising.
Thanks again.
- Lenexa, Kansas
Powder coating has an exclusive light wrinkled texture characteristic.
If first coat is not sanded smooth, would this wrinkle texture multiply? That seems to be my problem. Even orange peeling occurs.
- Union City, New Jersey USA
December 14, 2015
A. Film thickness is the primary contributor to variations in the appearance of textured finishes, so controlling this is very important. Thus, recoating will really impact the variation from the standard.
Rather than providing the applicator with a shopping list of parameters to control, it is safest to simply state that the material specified (Manufacturer and Product Number) is to be applied per the manufacturers directions.
As to printing on textured finishes, I have found it helpful to lightly hand sand the print area with 1200 grit paper to knock down the high spots prior to printing. Then when you heat cure the ink the gloss will come back.
Metlfab Inc. - Frederick, Maryland USA
April 11, 2016
Q, A, or Comment on THIS thread -or- Start a NEW Thread