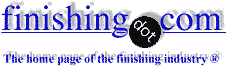
-----
480 Hour salt spray powdercoat steps
Hello All,
I work for a company who manufacture ancillary components for truck chassis. We currently spec 1000 hr salt spray on all drawings. I have found 2 problems with this.
1. Its an overspec
2. We are not getting close to this
I have experience working for large OEM manufacturers who write defined specifications nailing the suppliers to an exact process.
What operations from start to finish are required to powdercoat laser cut, welded and bent sheet metal components to 480 hour salt spray level.
Design Engineer - Newcastle, Tyne and Weir, England
August 26, 2011
First of two simultaneous responses -- August 26, 2011
Dear Angus,
I am not sure of your concerns when you state "it's an over-spec", is it because:
a) 1000 hours is not required for your particular items?
b) Your current process is unable to meet a 1000 hour ASTM B11
requirement?
To help others to advise you on this, please supply your current processing details, i.e. pre-treatment, type of powder applied and curing method, i.e. IR or convention ovens, time and metal temp achieved.
You should be able to achieve well in excess of 500 hours using a suitable cleaning, pre-treatment and top-coat regime.
Terry Hickling
Birmingham, United Kingdom
Second of two simultaneous responses -- August 28, 2011
You need to decide what you want out of this test.
It doesn't represent real life situations, but can be useful in measuring reproducible results.
There are several salt spray tests, using neutral salt solution and acidic solution.
You didn't mention if this is a test with a scored coating, or not.
So "xxx hours salt spray" without qualification doesn't mean much and doesn't specify anything precisely enough.
But in general what's required are to have a competent pretreatment system. This might be iron phosphate or zinc phosphate if painting on bare steel, and where corrosion isn't your concern, or to hot dip galvanize first then powdercoat if corrosion is an issue.
Laser cut material presents a special problem. The edges are quite accurately sharp, and most paint systems will have a thinner coating on this exposed corner (due to surface tension etc), so thinner coat there means less protection. And this is a vulnerable place.
Galv. however has a thicker coating on the corners, and when overcoated with powder (or paint) presents the aesthetics required.
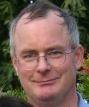
Geoff Crowley
Crithwood Ltd.
Westfield, Scotland, UK
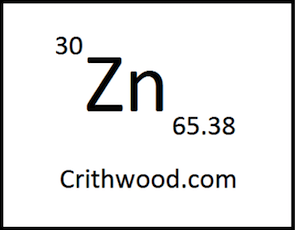
Q, A, or Comment on THIS thread -or- Start a NEW Thread