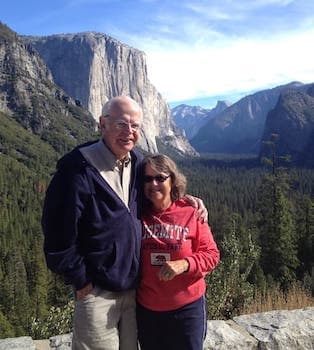
Curated with aloha by
Ted Mooney, P.E. RET
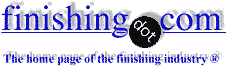
The authoritative public forum
for Metal Finishing 1989-2025
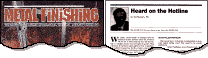
-----
Hardcoat with inconsistent finish
August 26, 2011
I recently had 8 components 2024 alum hardcoat anodized with Duplex Seal.
Three components are black. two are greenish black and one is gray.
(Photos added 8/30/11)
I am trying to determine which components are correctly coated or if they are coated incorrectly and why is the color/finish different?
Is the seal the issue or is it the process?
toolmaker - Groveland
August 27, 2011
I'll assume that all 8 pieces came from the same lot of material. You didn't mention if all 8 pieces came from the same vendor/anodizer, so I'll assume they did not. 2000 series aluminum can be difficult to hardcoat due to the high copper content, so there are quite a few different processes out there that anodizers use to process this alloy. All of which, can certainly conform to Mil-8625F type 3.
Things (significant) that can effect the color of a Type 3 class 1 coating. I'm also assuming that you specified Type 1, and not Type 2 (dyed):
1. Alloy
2. Anodizing bath temperature (some anodizers "hardcoat" at a higher bath temperature than others)
3. Current density
4. Coating thickness
5. Sealing process (you mentioned a duplex seal, which is typically Ni acetate followed with a DI water seal..but other sealing methods are certainly available which may have an effect on the color).
If all 8 parts came from the same vendor, and are from the same lot of material then I'd say they have a process control issue. If they came from different vendors, than the results you are seeing is not surprising. Anodizing is not like painting where each painter uses the same color paint. An anodizer has a myriad of process options at his fingertips to conform to the Type 3 specs, all of these options, as pointed out above, can and will have an impact on the look of the finished product.
So, if I were you, I'd select the piece/color that you like the best, and go with that anodizer as your vendor. But, if all 8 parts came from the same vendor, and were from the same lot of aluminum, then I would look elsewhere for an anodizer that can give you a consistent product.
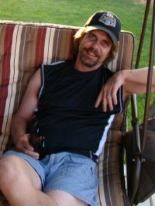
Marc Green
anodizer - Boise, Idaho
Marc, above, stole my thunder, and he is absolutely correct. Let me add. Air agitation hitting the parts, differently from part to part can change the thickness and the pore size, hence the color. Also, two "dual seals" are mentioned in my book, one that Marc describes, and the other is nickel acetate followed by sodium dichromate (color?) When you come back to us, let us know the thickness variances versus the color variances. In any case, the anodizer should never have sent back different colors for one job without volunteering to offer an excuse.
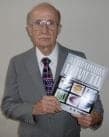
Robert H Probert
Robert H Probert Technical Services

Garner, North Carolina
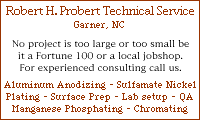
August 29, 2011
First of two simultaneous responses -- August 30, 2011
Yea!! Pictures!!
Well, now that it's obvious this is a class 2 coating (dyed) I'd hazard a guess that the "off-colored" parts have either a poor rinsing issue, inconsistent coating thickness issue..or a myriad of other options (poor quality control). This does not appear to be a sealing issue, in my opinion..as the off colors are lighter towards the middle.
I/we really need more info from you.
Same vendor?
All parts anodized at the same time/load?
Same lot of material? (this does not appear to be the issue)
Same coating thickness?
If these parts are from the same vendor, regardless if they were all of one load or not, that vendor has quality control issues. I personally, would never send out such an inconsistent product to a customer (again, assuming it all came from the same vendor)
If they aren't from the same vendor, obviously choose the vendor that supplied the product in the upper left hand corner for future work.
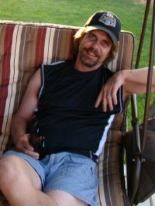
Marc Green
anodizer - Boise, Idaho
Second of two simultaneous responses -- August 31, 2011
You both are quiet experienced at this; for me this is a learning phase.
The color is not the problem.
I was contacted be the vendor and by the way, all material was from the same lot, 2024 bar stock.
What was stated to me was a part, which in the example picture right photo greenish/black had lost contact, and apparently the thickness of the coating was thinned out.
that is not acceptable.
I don't have a way to measure the thickness. Their excuse is: The parts were processed/anodized at different times.
The left photo (black part) is the part that came in with a consistent coat , some spotting, but acceptable and the result expected.
The vender said that they could be stripped and recoated, so I agreed. When I received the part two parts looked exactly like the part in question that was initially thinned out. and like I said, the other part is Gray and seems to be a consistent coated part.
Is it possible to re-strip the parts again and re-anodize them?
Will it effect the structure of the material?
And can the re_coated parts achieve that consistency alike the left photo.
They offered that option. What advice , if any, do you guys have , to ask of them to get the job done correctly?
your help is very much appreciated
- Groveland, Massachusetts, USA
There are two common problems possible here. (1) Most "job shops" do not understand that 2024 is 25% less conductive than most other alloys, hence needs 25% more voltage to "get the current on the part" and you need 12 amps per square foot. (2) the other problem is the racking (a) it must get the current on the part and (b) must not steal the current (as in a 6061 rack will get all the current and the 2024 goes hungry, low thickness means a different shade dye.
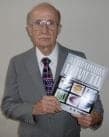
Robert H Probert
Robert H Probert Technical Services

Garner, North Carolina
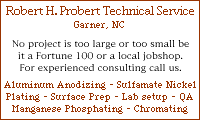
First of two simultaneous responses -- August 31, 2011
Second of two simultaneous responses -- August 31, 2011
My first response would be to find another anodizer. The part lost contact (which unfortunately does happen in our business on occasion) but that's not an excuse for sending you, the paying customer, a bad product hoping that you'll accept it, or won't notice without at LEAST notifying you of the problem before hand.
If you sent all 8 pieces of this job into your vendor at the same time, judging by the pictures they appear to be small parts (roughly 6" X 2" x 2" ??), I'd have to call BS on your vendor not processing them all at once, that simply makes no sense if you sent them all in at once. An anodizer makes money by maximizing his loads. And for a small 8 piece job like this, they would have been processed in the same load, again, assuming all 8 parts arrived at his shop at the same time.
It does make sense that the bottom right part was reworked. However what should have happened after stripping the original "bad" coating would have been the part should have been re-buffed/finished prior to re-anodizing to the same finish it would have been if it were new.. It appears it was not...and the finish on a part to be anodized is very important to the final look of the product.
The color really should be an important part for you, as you have the right to expect the same results from your vendor..but that's your call.
As far as re-working again...really, as long as your tolerances on this part aren't very tight, this should not be a problem (you will lose dimensions with each strip and re-anodize)...but I strongly suggest that after stripping the coating, that the part(s)are re-finished/buffed/grained to look like they were as they were prior to the first anodizing.
I hate to hammer another anodizer like this . . . as I've "been there and done that" for 25 years now, and I fully understand the problems that can arise in our business . . . but there's no excuse, in my book, for sending out poor quality work . . . especially when they obviously knew they had a coating thickness problem.
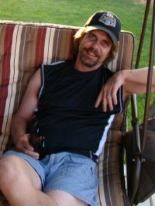
Marc Green
anodizer - Boise, Idaho
Thank-you Mark and Robert.
I have contacted the vender, still getting some excuses from their quality dept. I am going directly to their customer sevice with better information to get the parts reworked. thanks again
- Groveland, Massachusetts, USA
September 9, 2011
Q, A, or Comment on THIS thread -or- Start a NEW Thread