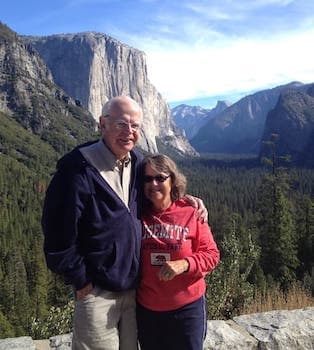
Curated with aloha by
Ted Mooney, P.E. RET
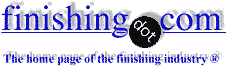
The authoritative public forum
for Metal Finishing 1989-2025
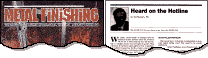
-----
Reducing variance in galvanizing coating thickness
August 23, 2011
How does one reduce variance in coating thickness due to double dipping of steel articles longer than the length of the bath. We use hydrochloric acid for degreasing and pickling and dry fluxing (based on triple salt) before hot dip galvanization in the bath which is 8 meters long and 2.4 meters deep.
Does top flux compensate for variance due to sandelin curve and if not, is there another alternative ?
Is there any standard way to measure the surface roughness before dipping in molten zinc bath so that it could be fine-tuned ?
employee - Gujarat, India
Sir:
Top flux does Not affect the Sandelin curve.
For double dip some galvanizers do the first half and then turn the product over (or around), go back to the flux tank and flux just above the zinc on the first half, and then galvanize the second half. Other galvanizers do the first half and then after brief cooling, flux the burn line with flux on a paint brush. The product must be cool enough to accept the painted-on flux. The product is then turned over (or turned around) and the second half galvanized.
Done properly with proper flux the double dip line is virtually non-detectable.
Regards,
Galvanizing Consultant - Hot Springs, South Dakota, USA
First of two simultaneous responses -- August 26, 2011
Its not clear what you're asking.
Do you mean how to avoid the extra thickness at the joint between the two parts of a "double dip" ?
Or what?
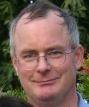
Geoff Crowley
Crithwood Ltd.
Westfield, Scotland, UK
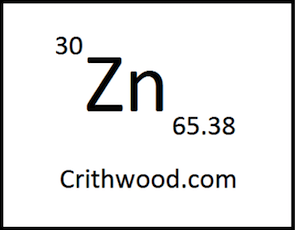
Second of two simultaneous responses -- August 28, 2011
August 30, 2011
Yes. My question was on how to reduce the extra thickness between the two parts of a "double dip". My other questions were on how to reduce the variation in coating thickness due to Silicon content in steel courtesy Sandelin curve and also due to variation in the surface roughness.
I understand that if crane operator is an expert, he could reduce the width of overlapping portion between the two parts of a double dip. But, that's difficult. The method suggested by Dr. Cook is cumbersome, as there will be cooling and fluxing time involved for fluxing before the remaining part is dipped in zinc bath. So, I guess, the choice is between a little more zinc pickup and dross with better productivity or lesser zinc pickup and dross and lower productivity.
Regarding reducing variation due to unfavourable silicon contents, I understand that certain liquid additives in the pre flux tank, help. Sorry, I wrote that as top flux.
Regarding variation due to surface roughness, is there any way to measure and see the influence of the same on coating thickness or is it worth ignoring ?
- Galvanizer, Gujarat, India
Thanks Dr. Cook for your reply on double-end dipping.
Regarding the measurement of surface roughness and studying the influence on coating thickness, what if I go by visual- based categorization into three categories of surface roughness and study the influence of each category on coating thickness?
Galvanizer - Gujarat, India
August 31, 2011
August 31, 2011
Flux the part to be dipped first, then dip it.
Using another crane, while the dipping crane carries on working, turn the long piece, and dip the ungalv'd end in the flux. It doesn't need cooling any more than it has in this time.
Then let the dipping crane take this piece again, and dip that freshly fluxed end.
The overlap should be 10 mm or less.
The overlap in zinc coating will be minimally thicker. It has the shortest immersion time of the 2nd dip.
Minimal dressing afterward should make the double dip mark almost undetectable.
Requires good operator, and good flux.
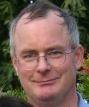
Geoff Crowley
Crithwood Ltd.
Westfield, Scotland, UK
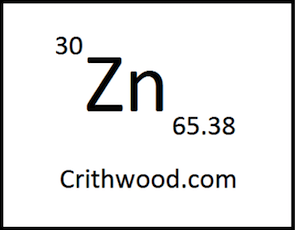
September 1, 2011
Sir:
I am not experienced in roughness, although I think their are gauges to measure roughness.
If the final zinc coating is dull grey, then it is likely that the steel is reactive and the zinc coating is thick. There are ways to get thinner and brighter zinc coatings. Some of these ways are good and some are bad.
Regards,
Galvanizing Consultant - Hot Springs, South Dakota, USA
Q. Sir,
Due to size restriction, we are doing DOUBLE DIPPING in our galvanizing practice of structural parts. Our Zn % is 4.8% and we need to reduce this. Does this DOUBLE DIPPING plays a role in Zn % ? Other than overlapping in certain middle portion , how else it affects the process??
- Gujarat, India
March 14, 2013
A. How do you calculate Zn % ? There are various ways, so your 4.8% might be good, might be medium, might be poor?
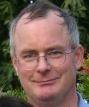
Geoff Crowley
Crithwood Ltd.
Westfield, Scotland, UK
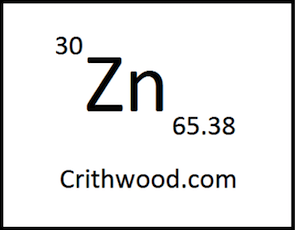
March 15, 2013
March 25, 2013
Q. Sir,
Usually Zn % consumption here in our area is calculated as,
Difference of 2nd and 1st weight taken, divided by the 1st weight and multiplied by 100.. e.g.
1st weight = 1000 kg
2nd weight = 1050 kg
Zinc % = [(50)/(1000)] x 100 = 5%
And how accurate this method is?
What other possible ways can be adopted to find out Zn% ?
Regards
- Dammam, Saudi Arabia
A. Sir:
You are reporting Net Zinc Usage Not Gross Zinc Usage. Net Zinc Usage is also sometimes Zinc Pick-up. For Gross Zinc Usage the zinc used divided by steel galvanized times 100% is the number. Your %Net Zinc usage probably would be 6% to 6.5% Gross Zinc Usage depending on how much dross and dry ash you produce.
Regards,
Galvanizing Consultant - Hot Springs, South Dakota, USA

Q, A, or Comment on THIS thread -or- Start a NEW Thread