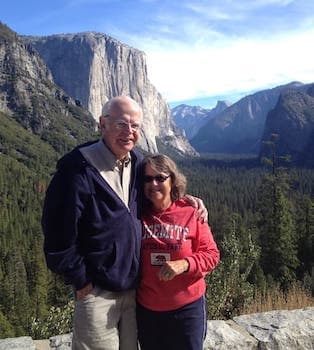
Curated with aloha by
Ted Mooney, P.E. RET
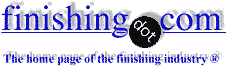
The authoritative public forum
for Metal Finishing 1989-2025
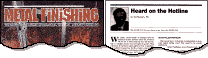
-----
Copper Alloy Corrosion Coming Through Gold Plating
August 21, 2011
I am working with a religious organization on a job of restoration. We contracted with a local plating company to gold plate a 32 light, rococo style, copper alloy (brass) cast, multi piece chandelier. Its size is 120 x 96 cm when assembled. The place of installation is outside under an open sided roof structure on near the seacoast.
The chandelier was taken apart, cleaned manually with wire brushes, then electrically stripped, given a copper strike, followed by a nickel strike, followed by a plating of gold (approx. .5 micron), and in the end sealed with a lacquer coating.
After a year small green spots started showing up and small streams of greenish white calcified deposits appeared, possibly condensation runoff (no rain has fallen on the chandelier). Now several months on, whole areas are giving off a greenish sheen. The plater's assessment is that this is not a plating failure but an impurity in the base material of the casting. We are told that the condition is the result of porosity in the castings and an extremely poor grade of alloy which is reacting with the atmosphere and oozing copper related corrosion. It seems, actually that there may be two different points of corrosion, one the pinpoints which start small and then the corrosion grows into larger round deposits and the second the "drips" from seams, which I suspect might be running out from the inside of the hollow chandelier pieces where the plating didn't cover.
The plater, though willing to help, is at the edge of their expertise and it is obvious that this treatment has not worked, is there an alternative treatment for the casting before plating that would neutralize the chemicals trapped in the porosity and/or seal the poor quality alloy and the porosity more effectively for a more successful plating?
Volunteer assisting with a restoration project - Haifa, Israel
Hi Kern,
Not sure how thick is the nickel strike. If at or above 5 micron, then should be a good diffusion barrier to retard copper/copper alloy elements migrate to gold layer over a long period.
Regards,
David
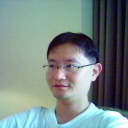
David Shiu
- Singapore
First of three simultaneous responses -- August 22, 2011
There should have been more than a "strike" of nickel, probably more like .001", however if there is porosity to start with, there may be nothing you can do.
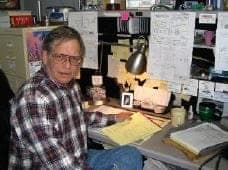
Jeffrey Holmes, CEF
Spartanburg, South Carolina
Second of three simultaneous responses -- August 22, 2011
Was that 0.5 microns of gold? Think in terms of 5.0 microns minimum over 5 microns of nickel.
You are not alone. I recall that the Dome of the Rock had a similar plating problem a few years ago.
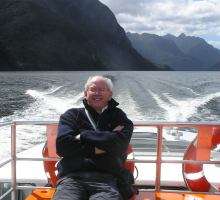
Geoff Smith
Hampshire, England
Third of three simultaneous responses -- August 23, 2011
1/2 micron on a less that very flat surface is not enough thickness to prevent corrosion from coming through. You only need about 0.0003 inch nickel to stop diffusion at room temperature, but you said "castings", that means porosity, so copper and nickel salts are corroding through. After copper plating let it thermal and humidity cycle for several days, then deox and nickel plate up to 0.0003 inch, then do you flash gold ($1900/oz today), then top off with CLEAR POWDER COAT.
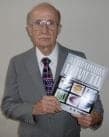
Robert H Probert
Robert H Probert Technical Services

Garner, North Carolina
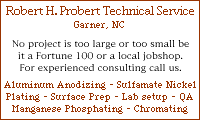
August 23, 2011
August 23, 2011
Wisman, Now-a-days Religious organisations spend lots of money. Spend a little more to deposit more gold!!
Tell the plater to first plate in cyanide copper to have a good build up deposit (10-15 minutes). Then let him plate Acid copper plating to get a good shine (10-15-20 minutes). Then let him give a 10 micron Bright Nickel plating (10-15-20 minutes) which will give a good barrier between gold and copper as copper diffuses if the thickness of nickel is less. Then comes gold. 0.5 microns is very less. Go for minimum 3 micros (450 mg of gold should be deposited on a surface of 1 DM square or 4.5 grams in 1 sq.ft.
In future, your children will remember you when they see this shining like a star!.. forever!!
Good luck.
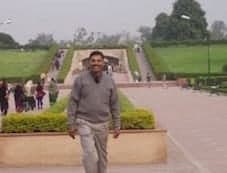
T.K. Mohan
plating process supplier - Mumbai, India
Q, A, or Comment on THIS thread -or- Start a NEW Thread