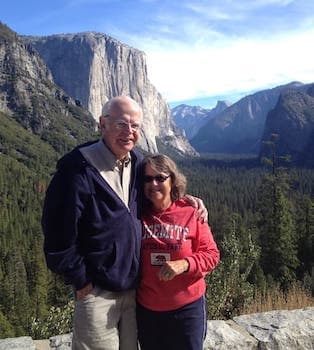
Curated with aloha by
Ted Mooney, P.E. RET
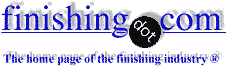
The authoritative public forum
for Metal Finishing 1989-2025
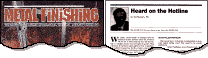
-----
Steel pretreatment type and scribe corrosion in salt fog
Greeting, my name is Robert Parker. I desire to improve paint performance and reduce variability in test results obtained from a manufacturing process.
An automotive shock absorber manufacturer uses both iron phosphate for some shocks and use a newer zirconium type pretreatment for other shocks. Comparative evaluation of scribe corrosion after 200 hours ASTM B117 yields inconsistent results when using the same paint. Neither pretreatment is substantially better than the other in prior testing with an alkyd / amino type product. Variable results have also been observed with 2K epoxy and 1K polyurethane. All paints are one coat DTM water reducible. Any suggestions on formulation or pretreatment would be appreciated.
Product designer / formulator - Bryant, Arizona, USA
August 11, 2011
Dear Robert,
Irrespective of the top coat applied (solvent, waterborne or to less a degree powder), once the top coat is compromised (damaged) then the extent that rust creep occurs depends upon a pretreatment to slow down any corrosion taking place. The pretreatment type that one chooses is one that first offers itself to be attacked by the corrosion elements in the surrounding atmosphere -- in this case salt, oxygen and water. These types of pretreatment materials are known as sacrificial coatings.
I think most people would agree that iron phosphate would not come within the scope of this category. However, it will clean the substrate and therefore improved adhesion of the following top coat.
Although I have little experience of zirconium phosphate I understand, used at 2% concentration, run at a temperature of 80° C with an immersion time of 30 seconds a 2 - 3 fold increase in corrosion resistance over that what can be achieved using iron phosphate.
I am informed by a pretreatment supplier that when using zirconium phosphate exceptionally clean substrates are necessary. I had a thought that your client could use the iron phosphate to clean the springs, then utilise the zirconium phosphate to create a rust creep preventative phosphate layer. I do not know if this is possible, but the concept seems to have some possibilities -- maybe it might prompt more input from the pretreatment experts.
I believe that a top coat using powder technology is more commonplace within your own industry than the ones you mention and where environmental issues are not too rigorous a pretreatment from the zinc phosphate range is used -- test results of 500 hours should then be commonplace.
Birmingham, United Kingdom
August 15, 2011
Q, A, or Comment on THIS thread -or- Start a NEW Thread