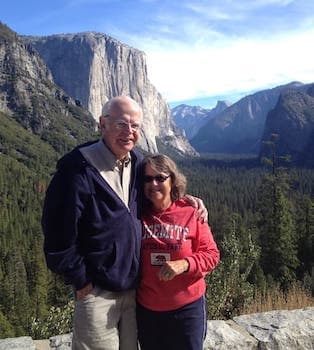
Curated with aloha by
Ted Mooney, P.E. RET
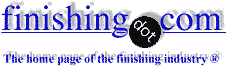
The authoritative public forum
for Metal Finishing 1989-2025
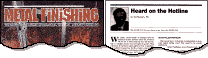
-----
More metal deposited than Faraday's law predicts
Hello Community! I'm David, and I'm no expert in this area, and I'm a high school student in need of answers for some questions that may seem a little too basic for you guys to want to bother, so I apologize for them.
Yes it's a school Investigation (I know you guys probably only want to talk about the Industry) but, I had set up 2 electrolytic cells with a normal 2M CuNO3 electrolyte bath (no smoothing agents, cyanide or anything) The 1st cell had a current of 1.35 A supplied to it, the 2nd had a current of 0.35 A. A copper tube was the anode (about 6cm in length), and a stainless steel Wood screw was the cathode (about 9 cm in length). There were 3 trials for each cell, and on average there was a 5.162% increase in mass for the screw under 1.35 A, but Faraday's law states that with a current of 1.35 A, there should be only a 5.145% increase in mass (assuming all trials had gained the theoretical amount). This was the same for the 0.35A test , where it had an average gain of 2.038%, but theoretically it should have only had a 1.222% increase (assuming all trials gained the theoretical amount of coating).
There were some weighing errors afterwards, and that is the only non-scientific reason I can come up with. What scientific reasons are there for this? We polished the anode and cathodes with steel wool before hand, and I think there may have been some impurities.
Help would be much appreciated. Thanks in advance!
David
Student - Miami, Florida, US
July 28, 2011
August 2, 2011
Hi David,
The deviation could be due to:
1. Weighing error - Weighing balance accuracy is just one point. The other point is to ensure Cu plated stainless steel is fully dried (put in oven for certain time) and cool down to room temp (put in dessicator to avoid water moisture absorption) before weighing.
2. Rectifier accuracy - The display ampere on rectifier may not be the true ampere applied to cathode. You need to do some kind of calibration/measurement of rectifier to ensure actual output same as display setting.
3. Bath contamination - If Cu bath is metallic contaminated then certain heavier metal(s) might co-deposit with Cu and results a higher weight gain.
Regards,
David
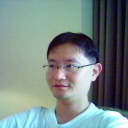
David Shiu
- Singapore
August 2, 2011
Copper nitrate
⇦ this on
eBay
or
Amazon [affil links]
is not a common chemical for electroplating, but it should work. Copper will plate out on steel with no current from a copper sulphate
⇦ this on
eBay or
Amazon [affil links] solution. It might also from a nitrate solution which will bias your answers.
Guess one is that your ammeter is not accurate enough for a fine measurement.
As you plate out the copper, the amperage will change slightly, so unless you have a constant current power supply, there will be inaccuracies.
You need to dry the part and let it cool in a desiccator both before and after plate. I will guess that you have some trapped water in a rough area of the plate.
You would do better if you used a piece of steel plate for your cathode and have the same amount of copper for the anode. Actually, for this type of experiment, I would use a very clean piece of copper sheet for the cathode and avoid the auto catalytic plate out mentioned in the first paragraph.
Use scotch brite rather than steel wool to clean it. If you have to, use 600 grit wet and dry carbide sandpaper. Be aware that almost all copper has a clear coat or similar on it to keep it from turning green/brown.
No electroplating is 100.0% efficient. You will exceed the hydrogen and or the oxygen over voltage potential and some gas will be liberated giving you less than calculated amount of deposited metal.
Before you write a report, pay attention to significant digits. You appear to have abused it in your calculations of %.
- Navarre, Florida
Some immersion plating is a likely cause of the deviation from Faraday's Law. Copper will immersion plate onto iron in your electrolyte with simultaneous dissolution of the iron. Since copper's atomic weight is higher than iron's, there would be a net increase in mass from this reaction.
Lyle Kirmanconsultant - Cleveland Heights, Ohio
August 5, 2011
September 7, 2011
Hi David
Please do not use copper nitrate for your experiments. The reason that nitrates are never used in industry is because electrolysis of the nitrate ion can create very nasty oxides of nitrogen.
Acid copper sulphate reliably plates at 100% faradic efficiency and can be used to calibrate an ammeter.
Some of the probable causes of your unexpected results have been explained but I would also question the accuracy of the ammeter in the second decimal place unless it was a very sophisticated instrument and carefully calibrated. Many instruments have an impressive meter that is far from accurate.
You also quote efficiency to three decimal places. You can only do this if your measuring systems (weight, current etc.) are accurate to at least ten times this! (top research grade kit!) Ask your teacher to explain cumulative errors. It is very tempting to think that all those numbers on your calculator are meaningful but mostly they are not.
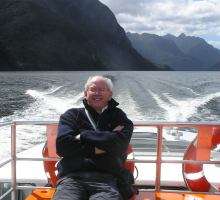
Geoff Smith
Hampshire, England
Great response, Geoff. Thanks.
Regards,
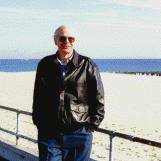
Ted Mooney, P.E.
Striving to live Aloha
finishing.com - Pine Beach, New Jersey
September 8, 2011
Q, A, or Comment on THIS thread -or- Start a NEW Thread